Pressure die casting: Find suitalbe suppliers
Discover specialized suppliers for pressure die casting on Techpilot. Our platform connects buyers with suppliers who use advanced casting technologies to manufacture high-quality parts. Use the e-sourcing process to find the best suppliers.
341 suppliers for Pressure die casting
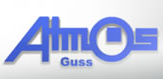
The Atmosform AG was founded on 01.01.1948 sen by Fritz Lüdi. founded. From the former Die-casting a modern die-casting operation has in its second generation, headed by Mr. HP Lüdi developed with its own mold design and machining department with 40 employees. Under the brand names we produce on the latest die casting machine with 50t to 420t clamping force, casting parts / semi-finished products of aluminum and zinc alloys from 10g to 2.5 kg in the highest quality, any shape and number of pieces.
Founded
Employees
20 - 50
Certifications
Selzach
Switzerland - 2545
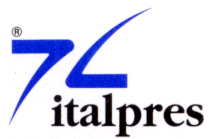
Aluminium high-pressure die-casting foundry, with in-house mold development and manufacturing - 100% made in Italy Modernly equipped foundry shop, with mostly fully automated die-casting machines (cold chamber) with locking forces up to 1400t Unit part weight (depending on projected area) up to approx. 14kg
Founded
1947
Employees
20 - 50
Certifications
Lumezzane Gazzolo (Brescia)
Italy - 25065
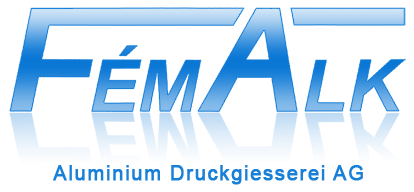
The predecessor of FÉMALK (Fémöntészeti és Alkatrészgyártó) Zrt. was founded in 1993 by Hungarian private individuals. Since then it has become one of the largest privately owned aluminum pressure foundries in Hungary. Its turnover exceeded 20 million Euro in 2006, and it employs 225 people. The main profile of the company is pressure die casting, and it also does several other task and work phases (product and tool design, modeling, tool production; machining, surface treatment and assembly of castings). The company exports almost all of its products. It provides mainly German, Swedish and Austrian suppliers of the automotive industry with castings.
Founded
1993
Employees
200 - 500
Certifications
Budapest
Hungary - 1211
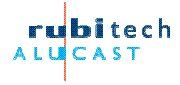
Rubitech Alucast is part of Rubitech Group, whose authentic, innovative and results-oriented corporate culture provides a solid basis. For more than 27 years Rubitech is active on the international market for aluminum high pressure die casting. Thanks our unparalleled experience in the areas of production processes, Supplier management, design and development, technical requirements, Innovation and product development, we offer our customers products and Services with which they can be distinguished from other market participants. Rubitech world The Rubitech Group has subsidiaries in the Netherlands, Great Britain, Malaysia and Romania. Our head office is in Steenwijk in the Netherlands together with our sales office in the UK is responsible for sales, Customer service and R & D. Our employees in Malaysia and Rumänian are for the Responsible local production, quality and logistics process. Sales and marketing business units Our sales unit Rubitech Alucast develops and supplies since 1983 Aluminum die-casting products.Thanks guarantee our supply chain management We offer our clients individual product solutions throughout the supply chain. Rubitech Heating was founded and developed in 2005 and produced Condensing heat exchanger for residential and commercial use. Rubitech Great Britain and Romania are Rubitech for sales, warehousing and Customer service in Britain and Central Europe responsible. Operational business units Monitor the production companies Rubitech Malaysia and Rubitech Romania and coordinate the flow and production in the relevant appendices. Both companies are responsible for production and quality assurance; also accepts our Romanian subsidiary sales and customer service for our Central European customers. Certificates available on request.
Founded
1985
Employees
50 - 100
Certifications
Steenwijk
Netherlands - 8331 TR
Would you like to know which suppliers are ideally suited to your requirements?
Register now and submit your request.
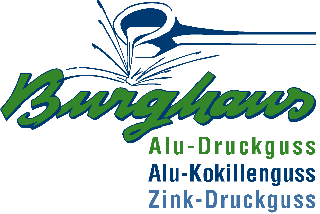
In more than 50 years came from a small family, a modern company. Our work is based on the latest technology in production, a customer-oriented organization and expertise in all areas of Al and Zn die-casting, as well as the Al-Kokillengusses. Customer satisfaction, short distances, quality, experience, flexibility, environmental awareness and innovation. This will make us a lot of customers to a major supplier for castings of aluminum and zinc. We help you in achieving your claims in the shortest possible time and in top quality. We have specialized in casting products in small and medium series. We assume not only casting production, but also the mechanical machining, surface treatment, assembly and logistics of pre-finished parts. A high degree of punctuality in through a personal contact person is the foundation of a successful partnership for us.
Founded
Employees
Certifications
Wenden
Germany - 57482
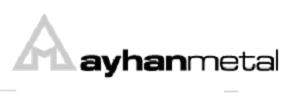
Ayhan Metal has been functioning in the die casting industry since 1991. Our production technology includes high pressure die casting presses with different locking forces within the range of 25 to 600 tons, which enable the production of casting weights from a few grams up to 2 kg. The main objective of Ayhan Metal is to ensure complete customer satisfaction and to be able to satisfy his or her implicit and explicit needs while supplying products and services in conformity with the agreed requirements.
Founded
Employees
Certifications
Kocaeli
Turkey - 41400
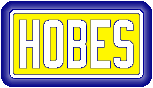
Our company is zinc-alloy die-casting company, we produce from ZAMAK parts according our customers designs. The we manufacture stainless steel furniture frames for garden furniture - we can machine, punch, stamp, turn, mill, weld, polish.
Founded
1994
Employees
50 - 100
Certifications
Trebisov
Slovakia - 07501
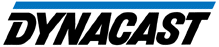
Specialist for precision small parts in zinc, magnesium and aluminum die-cast With 3,000 employees and 20 factories in 16 countries, Dynacast Group ranks among the leading manufacturers of die cast parts. An important success factor for the rapid development of the company is the so-called 4-slider technology that enables the production of very small parts with a weight of about 0.01 g with high precision and repeatability. With high-performance machines and innovative tool technology developed in Dynacast produces extremely complex die castings weighing up to 1,000 grams for clients in diverse industries around the world. Top.
Founded
1969
Employees
> 1000
Certifications
Bräunlingen
Germany - 78199
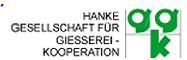
The HANKE Society for foundry cooperation mbH (HANKE ggk) specializes in the manufacture of precision aluminum die castings for the automotive industry. The company was founded in 1993 by President and CEO Siegfried Hanke and currently employs 50 people. The foundry provides steering and switching systems for leading automotive manufacturers. He is highly automated, flexible and largely. The investment rate is 26 percent and always ensures the necessary capacity building - particularly for large quantities - at low cost and consistently high quality. PPM = 0 is not a dream! The HANKE ggk operates according to a comprehensive quality management system is certified according to DIN EN ISO 9001:2000. During the entire production process, a continuous process monitoring takes place. From the careful selection of materials used on numerous intermediate checks to final inspection ensures that all products leave only as a guaranteed HANKE-quality cast the company. Due to their many years of successful cooperation and supply relationships with leading automotive manufacturers has the HANKE ggk extensive knowledge of the country-specific customer requirements including Japan, the UK, France, Brazil, Poland and Slovakia. Prerequisite for market success is the HANKE network - an international cooperative community of SMEs. In a project-based European network of 500 designers, mold makers, toolmakers and automation engineers from 15 partner companies in Germany, Sweden and Denmark are pooling their expertise for complex solutions in the design, construction, prototyping, tooling, aluminum die casting and process automation.
Founded
1993
Employees
50 - 100
Certifications
Eberswalde
Germany - 16225
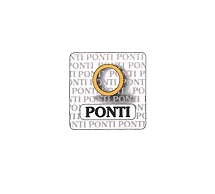
The Ponti Guarnizioni company, with its 40 years of experience, has achieved good skills in the process of transformation of elastomeric raw materials. It specializes in molding technical articles on customer's drawing, in various types of standard and special compound, also with restrictive regulations, using hydraulic injection and compression presses. The elastomeric materials are: ACM - AEM - AU / EU - CO / ECO - CR - EPDM - FKM - VMQ - FVMQ - HNBR - NBR - IIR - CSM - NR - SBR - FFKM. The management system conforms to the UNI EN ISO 9001: 2008 standard and from 2018 will be the certification of compliance with UNI EN ISO 9001: 2015 standard. The range of products is wide and includes: bushings, sealing rings, molded and / or cut washers, caps, solenoid valves, membranes, filter seals, coffee machine seals, binocular seals, rubber gaskets -metal, special o-rings for sizes, materials and tolerances. The sectors to which its products are intended are different, among the main ones: oleodynamic - pneumatic - electronic - optics - appliance - lighting - filtration - oenology - agricultural mechanization. The company interacts with qualified suppliers, specialized in the design and manufacture of molds, in supplying raw materials and in the finishing stages of the production cycle. It has competent staff, able to understand the needs of the customer, providing excellent consulting technical and commercial assistance. The Ponti Guarnizioni brand is present in several European and extra-European countries, with good competitiveness, thanks to a business policy tailored to meet the specific needs of the Customers, also accepting requests for small production lots, guaranteeing dimensional tolerance ranges and hardness of the materials more restrictive than the standards governed by the regulations in force in the rubber-plastic sector. For more information, please visit the website: www.pontiguarnizioni.com
Founded
1991
Employees
10 - 20
Certifications
Foresto Sparso (BG)
Italy - 24060
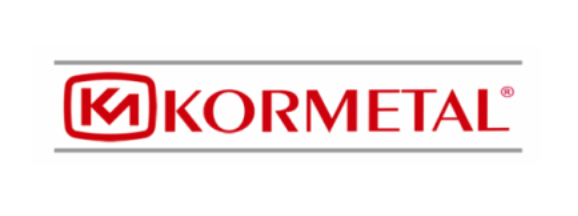
KORMETAL is a group in Turkey dealing with manufacturing, marketing and export import facilities was established in 1978 and started its activities producing parts for general purpose, which are alloyed out of aluminium and zinc using pressurised casting technique. Besides manufacturing high pressure die casting components with aluminum alloys for its customers, as of 1986 KORMETAL started to produce light alloy wheels rims produced from primary aluminium alloy and using the low pressure casting technique and soon became an interior market leader and started to sell its products to 44 different countries all over the world as a trademark. Date from 1994 KORMETAL continues its activities at Avcılar, Istanbul, Turkey and operates from a 30,000 square meter facility capable of producing 5000 tones/year aluminum alloy casting capacity via both high and low pressure method. Through the years, KORMETAL has proven to be innovative in its design, manufacturing, quality and management objectives, just-in-time manufacturing with zero defect and renovated its low pressure casting plant completely and using the high-tech die casting techniques with latest modern machines in general purpose production. KORMETAL, upon request, can design and produce your molds with high sensitivity using CAD-CAM technology and has qualified, highly skilled and experienced team members using AUTOCAD, UNIGRAPHICS, ANYS, SURFCAM. KORMETAL, which besides the ISO 9000:2000 Quality System Certificate, has many product and different quality certificates as well, exports approximately 80% of its production mainly Germany, France, England, Holland, Portugal, Russia, Ukraine. Also submit an application for TSE 16949 and we expect to get this quality system certificate in 2007.
Founded
1982
Employees
200 - 500
Certifications
Avcılar-İstanbul
Turkey - 34320

The company Grünefeld is a guarantee for high-quality die casting products and operates a continuous development of conventional die casting technology with aluminum and zinc. Green box is also your partner for aluminum gravity die for the highest demands. We produce parts weighing from 1 gram to 3.5 kg.
Founded
Employees
Certifications
Schalksmühle
Germany - 58579

Our company has over 25 years experience in foundry technology. Over time, the operation has grown to a size that required the legal form of a general partnership. Both partner Edyta Ordon and Bernard Siminski interest in the capital of the company to 50%. Our company produces iron castings in series production. In the foundry Siminski - Ordon is molded with the molding machine DISA 130. The molding machine has the following parameters: Shape measures 480/600mm maximum power 360 molds / h Length of the cooling system 28 m (AMC + SBC) Machining Foundry Siminski - Ordon offers a complex Servis, the machining, painting, assembly and packing of castings includes. In the field of mechanical processing, we work with many Polish and foreign companies. We engage over 2000 tons per year. Our finished products meet high quality standards
Founded
Employees
100 - 200
Certifications
Poczesna, Zawodzie
Poland - 42-262
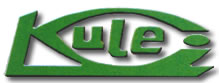
We are die-castings & gravity castings producer. The company was found in 1985 in Poland. Currently produced castings are made on 32 high pressure die casting machines (horizontal, vertical, cold- & hot-chamber) with the locking force range from 53t to 1100 t and vacuum vert-a-cast type 400t machine. We make castings from non-ferrous alloys (aluminium, zinc, brass and lead). Our company is equipped with vacuum-pressure resin impregnation line, shot-blasting and sand blasting machines, vibratory grinding machines, threading and drilling machines. Our toolroom is equipped with CNC machining centers, lathes, milling machines, spark erosion machine, surface grinding machines, cylindrical grinding machine etc. Quality control dep. is equipped with spectrometers, durability testing machine, hardness testers, X-ray machine and measuring machine. We cooperate with tool makers, electroplaters and painters (wet and powder). We export our products to Germany, France, UK, USA, Italy & others. ISO 9001 certificate was awarded to our company in the year 2000.
Founded
1985
Employees
50 - 100
Certifications
Klobuck
Poland - 42-100
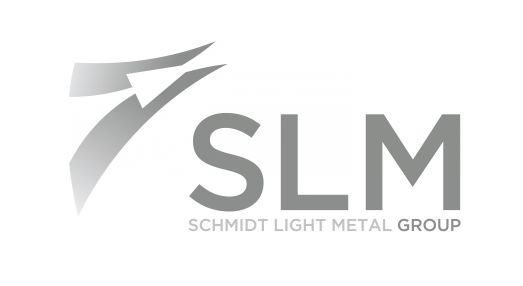
Strong all-around - SLM 360º We develop and manufacture complex aluminium die-cast solutions for the automobile industry and its system suppliers. As a Group, our strengths lie in the development of tools, products and processes as well as in our high level of flexibility and ability to take action quickly to implement solutions for our customers. We want to expand our business activities to increase flexibility, transformation time and cost-effectiveness in the provision of light metal components for our customers. Therefore, we are expanding our capacity for order-related assembling. From company to group The original and main activity of the owner-run Group is the manufacturing of aluminium die-cast products for the automotive and component supply industry. Created in 1989, the aluminium die-casting foundry originally made unfinished parts for the European automotive industry. Today as a Group, we are a competent partner to our worldwide customers for the entire process, from product development to the delivery of complex, ready-to-install light metal components. The right approach Our aim is to obtain full customer satisfaction and to build a business relationship designed to develop into a long-term partnership. It therefore goes without saying that we deliver products of the desired quality, in the agreed amount and at the required date. Our references are proof of the level of confidence we have established over the past years with our customers. The principle of error prevention always comes first in regards to quality measures and our quality objective is “zero defects”. Our numerous certifications are proof of our commitment.
Founded
1989
Employees
200 - 500
Certifications
S. Tiago de Riba-Ul
Portugal - 3720-501
Would you like to know which suppliers are ideally suited to your requirements?
Register now and submit your request.

Year of establishment: 1954 Delivery: 129 425 t Sales: EUR 289 million Export: 86% Sales / Employees: 293,000 EUR Owner: ELES 80% (ELES is the Slovenian state-owned electricity producer) Employees: 988
Founded
1954
Employees
500 - 1000
Certifications
Kidričevo
Slovenia - 2325
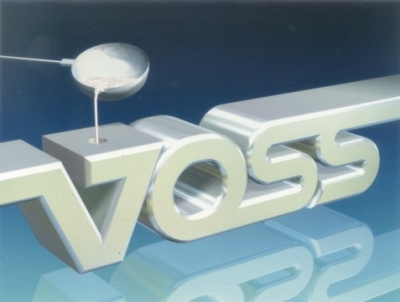
Our company is positioned as a delivery partner of small and medium series for cast aluminum products. The gravity die casting offers in lot sizes from 500 pieces, high strengths and high material density. However, seek a technically and economically optimal solution, so we offer the die casting process. It allows small wall thicknesses, weight and material savings, smallest tolerances and continuous production processes, with lot sizes from approximately 3,000 pieces. Through our own CNC machining the finished aluminum castings are order-specific processed and coated as desired. Our design department advises our customers on casting issues and coordinates the preparation of the printing and Kokillengusswerkzeuge with our own tool or the suppliers. Our quality management system complies with the requirements of the standard DIN EN ISO 9001 and is regularly updated through internal and external audits.
Founded
1957
Employees
20 - 50
Certifications
Finnentrop
Germany - 57413
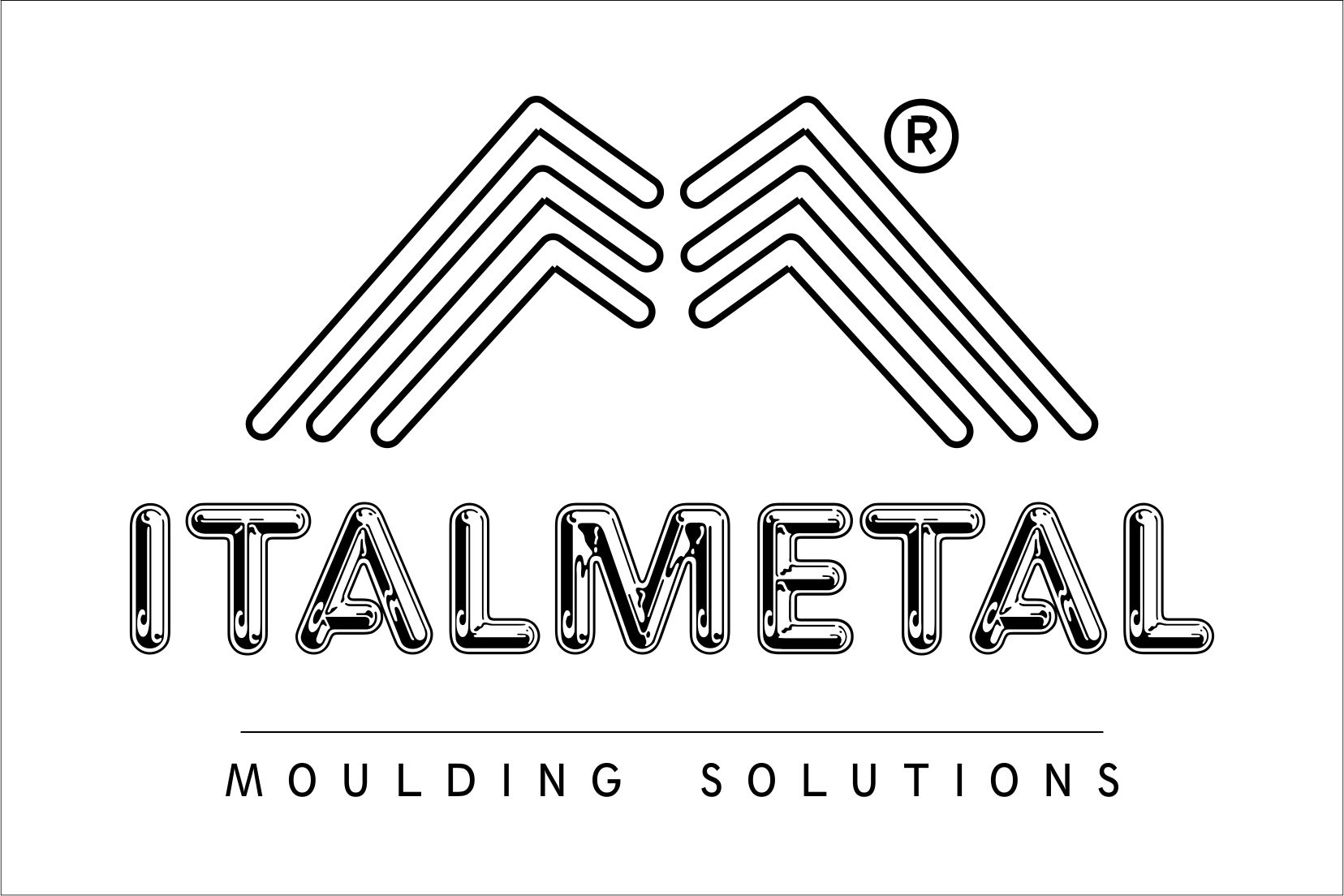
Founded in 1989 thanks to the brothers Luigino and Sante Cippitelli, Italmetal specializes at first only in the production of buckles and metal accessories for leather goods, quickly establishing itself as an important supplier for several national and international companies. Parallel to the production of accessories for leather goods, the company gives life to a technical department of design and development CAD-CAM for prototypes and moulds in steel, reaching important positions also in the production of technical details in zamak, in particular for the industry of furniture, automation and accessories. Currently the company, spread over a covered area of 5,000 square meters and with a workforce of 40 employees, is able to provide a complete service that goes from the study of the product up to the production of the same, passing through all the phases of the process work, which are carried out almost completely within the company itself. The types of processes that Italmetal can offer are almost exclusively addressed to the injection moulding sector. The two main production sectors are: Design and production of injection moulds for zamak and plastic materials. In the various phases that constitute the birth of an egg produced, the realization of the mould represents a crucial moment that will influence all the subsequent production phases of the product. The Molds department designs and manufactures moulds both for third parties and for internal needs. The department consists of a technical office that analyzes and studies the equipment commissioned to verify the times and technical specifications, and a modern workshop that follows all the construction phases. Together with the Stamping department, it carries out the testing of the equipment made up to the final set-up. Zamak moulding. The Stamping department, in addition to testing the equipment produced by the moulds department, takes care of the moulding and all the subsequent processing steps to which the parts are submitted before delivery. The technologies used in the department are two, by die-casting and by centrifugal moulding. Die-casting is used for the production of parts with high runs and for the production of technical parts with reduced dimensional tolerances, the centrifugal moulding is used for the realization of medium / small series and "pilot" parts. In almost 30 years of activity in the field of accessories production, the company has gained experience and expertise in the matter to be able, for each new project, to define with accuracy and safety the problems that may occur in the various production processes and consequently, advise the customer on the most suitable solutions to simplify or prevent these problems. Our strong point is this, a deep knowledge of the problems related to the development of new products, supported by years of experience and the use of the latest technology, which allow us to solve technical problems before the launch of the order and update our customers in real time already in the pre-industrialization phase of the product.
Founded
1989
Employees
20 - 50
Certifications
Servigliano (Fermo)
Italy - 63839

GÜRGENLİ Mühendislik Ltd started its activities in Bursa in 2000 in order to serve in the heavy industry sector. It aims to produce quality with the knowledge of the trained personnel with many years of experience in the sector. We are a company that has adopted the principle of working without compromising customer-oriented social responsibility and ethical values within the sectors we operate. GÜRGENLİ Engineering Ltd carries out design, manufacturing and assembly projects with its skilled engineer staff in the heavy industry sector.
Founded
2015
Employees
10 - 20
Certifications
BURSA
Turkey - 16110

We are a family owned light alloy diecasting foundry founded in 1974, which works in the ISO 9001: 2015 and IATF 16949: 2016 certified quality management system. The company has 2 melting furnaces and 11 die casting machine, from 400 to 1100 tons, all fully automated, and is able to do all the necessary processes to provide the customer with finished parts ready to be used in production adding all kind of machining, leakage controls, 3D tomography, painting, and many others. We have a long experience in the die casting of for chairs, and we collaborate with the major Italian manufacturers. In addition, recently, to ensure a complete service to the customer, it acquired the company Svea Stampi, which specializes in the construction of highly complex molds for plastics and aluminum die casting with an ISO 9001: 2015 certified quality management system. With its experience of over 35 years, Svea Stampi can offer you multiple services, including the choice of the most suitable materials for the specific product, choice and study of the type of feeding through the simulation of filling, solutions for the simplification of the mold, molds for prototypes, dimensional surveys, as well as after-sales assistance and modification interventions. We design molds with dimensions up to 1450 x 1200 mm for presses with clamping forces up to 1500 tons.
Founded
1970
Employees
50 - 100
Certifications
Lavenone
Italy - 25074
Find the ideal supplier in just 1 minute
Communicate directly with buyers
Unique market price comparison to realize the best prices
Existing processes, systems and suppliers can be easily integrated.
Buyers use the platform completely free of charge