Plastic injection molding
In the case of plastic injection molding, molten plastic is injected into the shaping cavity (cavity) of a tool, compressed under pressure, cross-linked or brought to cooling and then ejected as a molded part.
The injection molding is the most used method for the highly automated production of workpieces from plastic by the processing of powder or granules. Complexly shaped workpieces can be produced in almost any size. The high accuracy and short cycle times predestine the method for economical series production.
While injection molding is a cyclic process for producing workpieces with a specific geometry, extrusion is a continuous process for producing continuous profiles. During extrusion, the plasticized plastic is not injected into a closed mold, but is pressed through a die.
While injection molding is a cyclic process for producing workpieces with a specific geometry, extrusion is a continuous process for producing continuous profiles. During extrusion, the plasticized plastic is not injected into a closed mold, but is pressed through a die.
In plastic injection molding, the raw material – usually as granules – is first heated and plasticized in a screw cylinder. The plastic mass is then pressed into the tool with high pressure. This is then cooled to solidify the melt and finally remove the finished workpiece.
The most common processes for processing plastics include:
Urforms:
- Injection molding
- Extruding
Reforms:
- Deep drawing
- Bending forming
Five:
- Welding
- Adhesive
- Stick
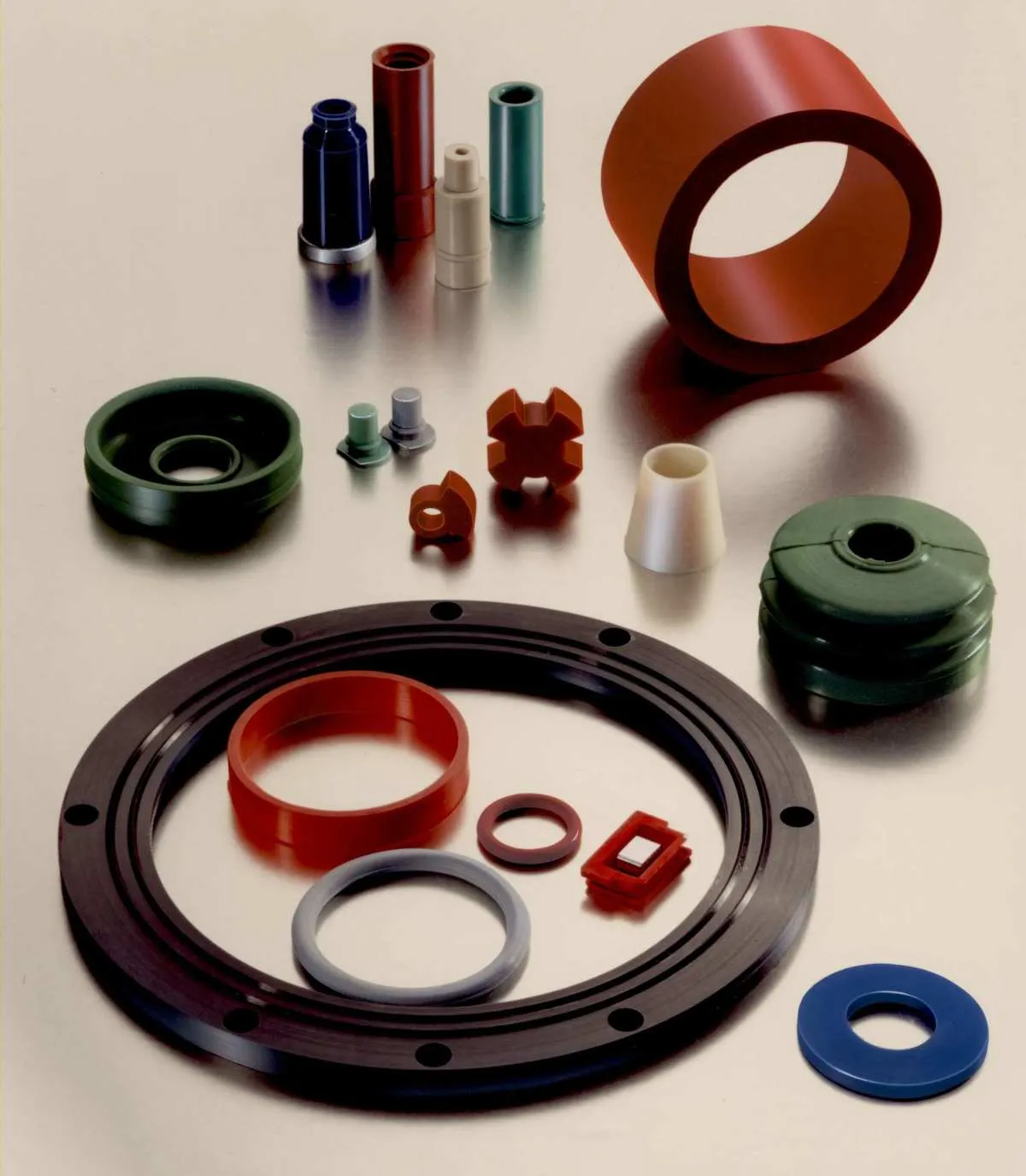
Rubber and silicone parts of the company nordform plastic
Because of the high expenditure for the production of injection molding tools, the method in the production of prototypes and small series can hardly be used economically.
Construction of an injection moulding machine
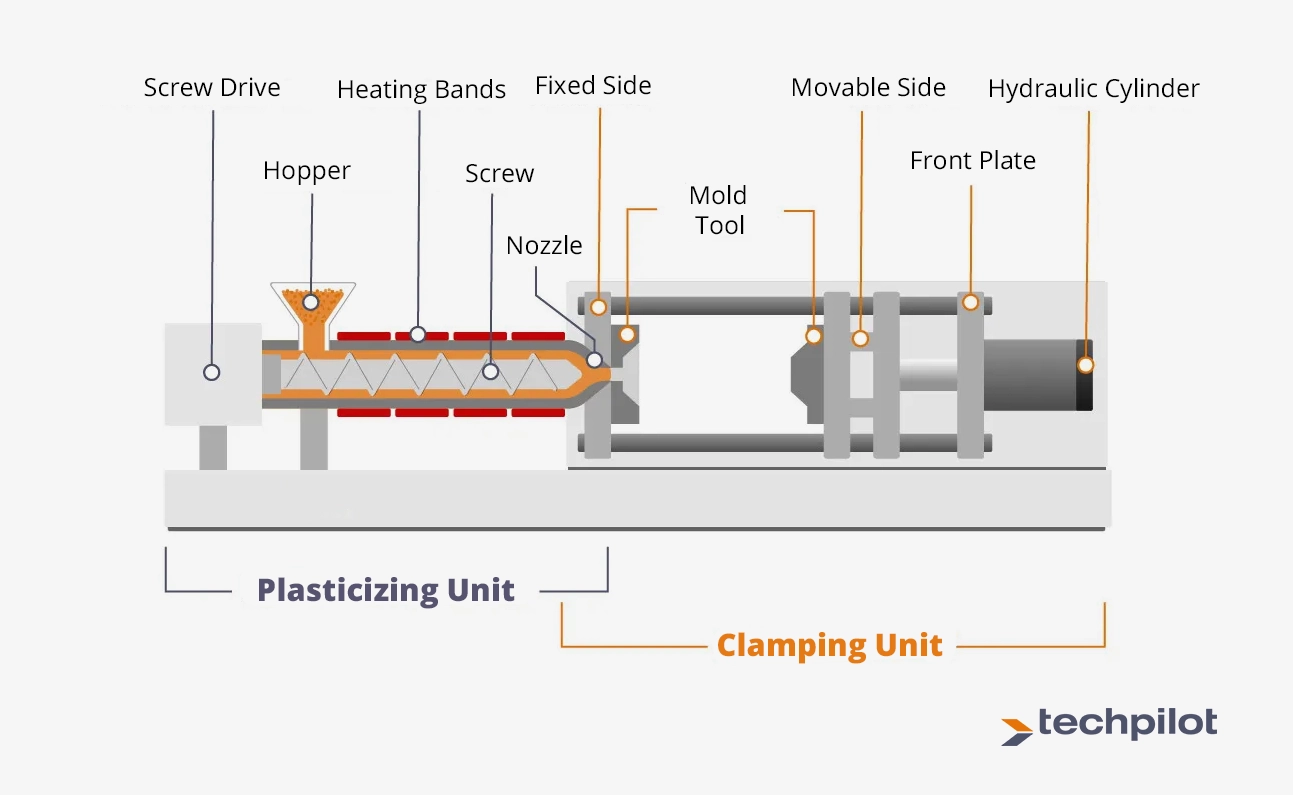
Process flow of plastic injection molding
The injection molding machine largely automatically coordinates the cyclic process sequence described with reference to the process variables. Determining factors for the settings on the machine are:
- Used plastic
- Form design (number and size of cavities, wall thickness)
- Machine (holding force, stroke volume)
Special variants of plastic injection molding that require individual process control include:
*Injection of inserted parts - Smoulding of an inserted carrier part
- Producing hollow spaces in injection molded parts
- Injection of foam parts
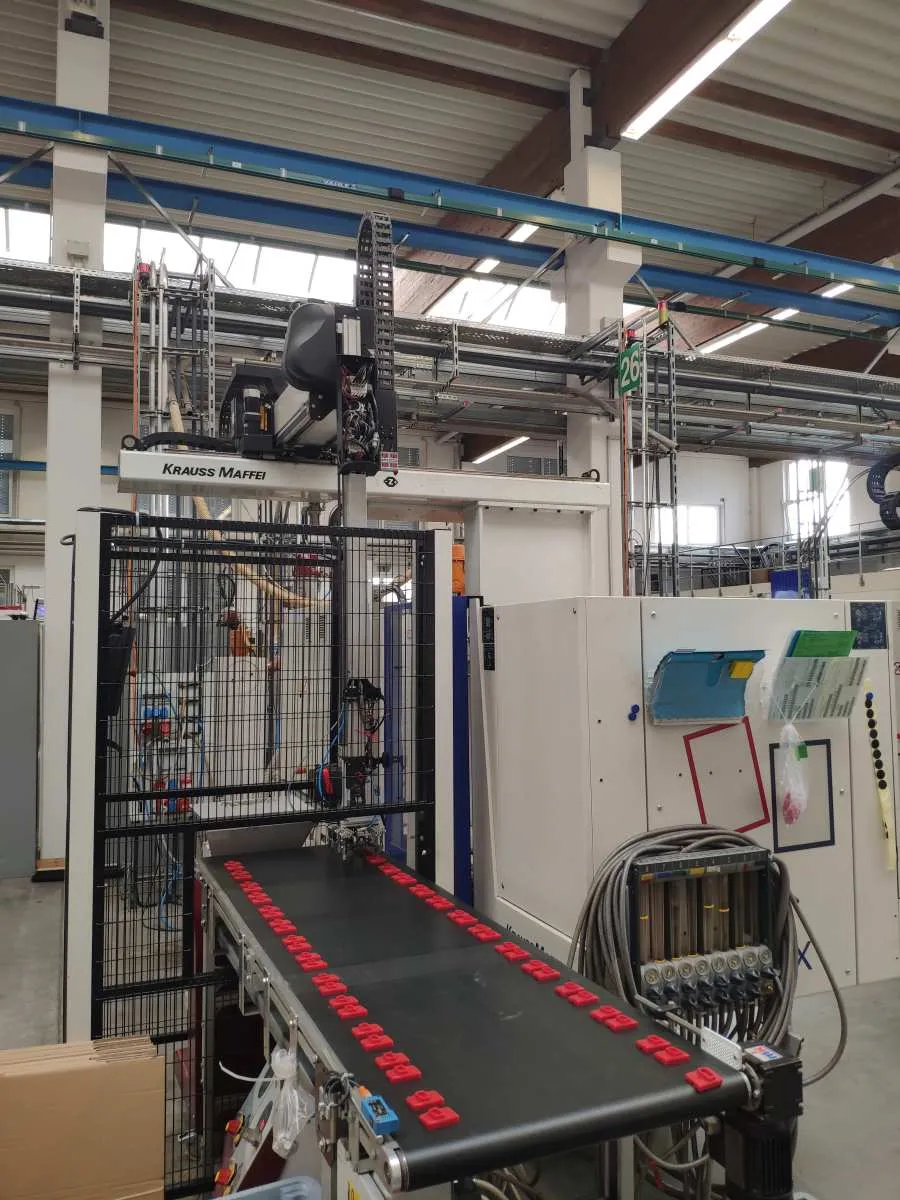
Plastic injection machine from RABATECH Kunststofftechnik
Different types of plastic put individual requirements on the tempering of the tool. The injection molding of a thermoplastic is described by way of example here:
1. Plastifying and dosing
At the beginning of the injection molding cycle, the tool is opened and a metered mass volume is present. The molding material is produced by drawing the plastic granulate from the funnel by a screw and melting it. The material is plasticized by the action of heat in the heated screw cylinder. The screw transports the material into the front cylinder part where it collects behind the nozzle. This results in a dynamic pressure which causes a reverse movement of the worm.
2. Injection
If the tool is now closed and a melt quantity sufficient for the tool filling between the nozzle and the screw tip, the injection can take place. For this purpose, the axially displaceable screw presses the plastic material into the mold. The pressure rises to a maximum value during filling and then decreases gradually.
3. Reproduction and cooling
In order to be able to compensate for the shrinkage of the solidifying melt, a pressure is maintained. The mass cushion remaining in front of the screw tip can thus flow into the mold. This serves to avoid frequent errors in injection molding: incidence points and lunkers. The tool is cooled to accelerate the cooling process of the injection molding.
4. Deforming and evaluating
The tool for ejecting the solidified injection can now be opened. In this case, the workpiece falls out of the mold or is removed from a handling device. Thereafter, the casting which is not part of the molding can be removed manually or automatically.
What materials can be processed in plastic injection molding?
Plastic injection moulding is suitable for processing all types of plastics:
- Thermoplastics
- Duroplasty
- Elastomers
- Thermoplastic elastomers
However, it should be noted that the different polymers require different tempering of the tool. The greatest economic importance is injection molding of thermoplastic materials, especially polyethylene.
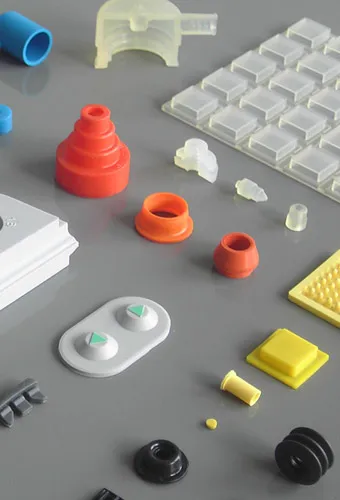
Injection molded parts made of silicone from Karl Kühnlein GmbH Gummi und Kunststoffe
Advantages of plastic injection molding are:
- High reproducibility of production
- No or only slight reworking of the molded part is necessary
- Fully automated method
Often the workpieces produced during injection molding can be used without further reworking. Accordingly, the direct path from the raw material to the finished part contributes to the attractiveness of the process.
Examples of jobs in the Techpilot marketplace
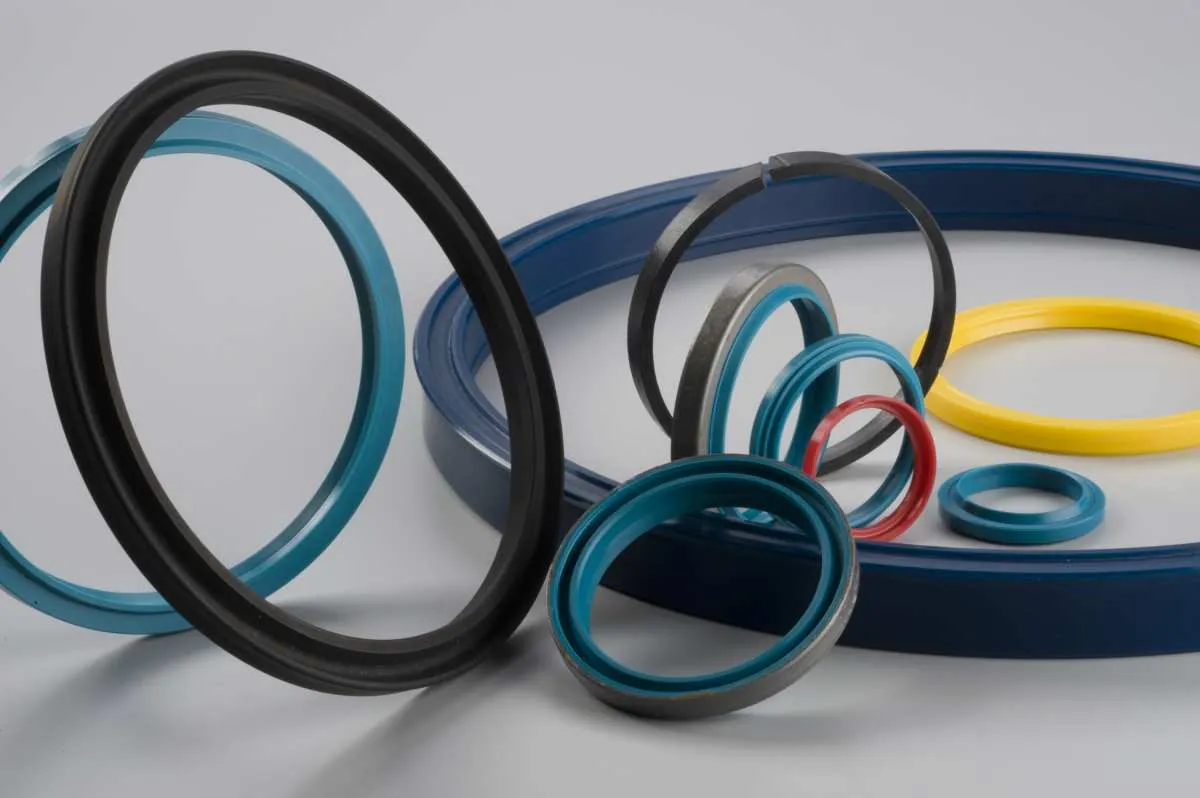
Elastomer rings from ALLTECH SRL
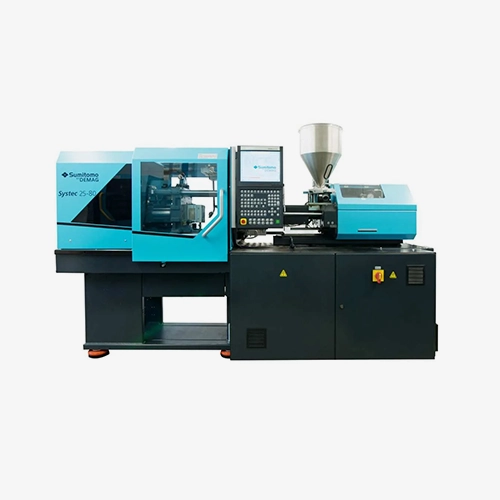
Injection moulding machine used by Stocker Kunststoff GmbH
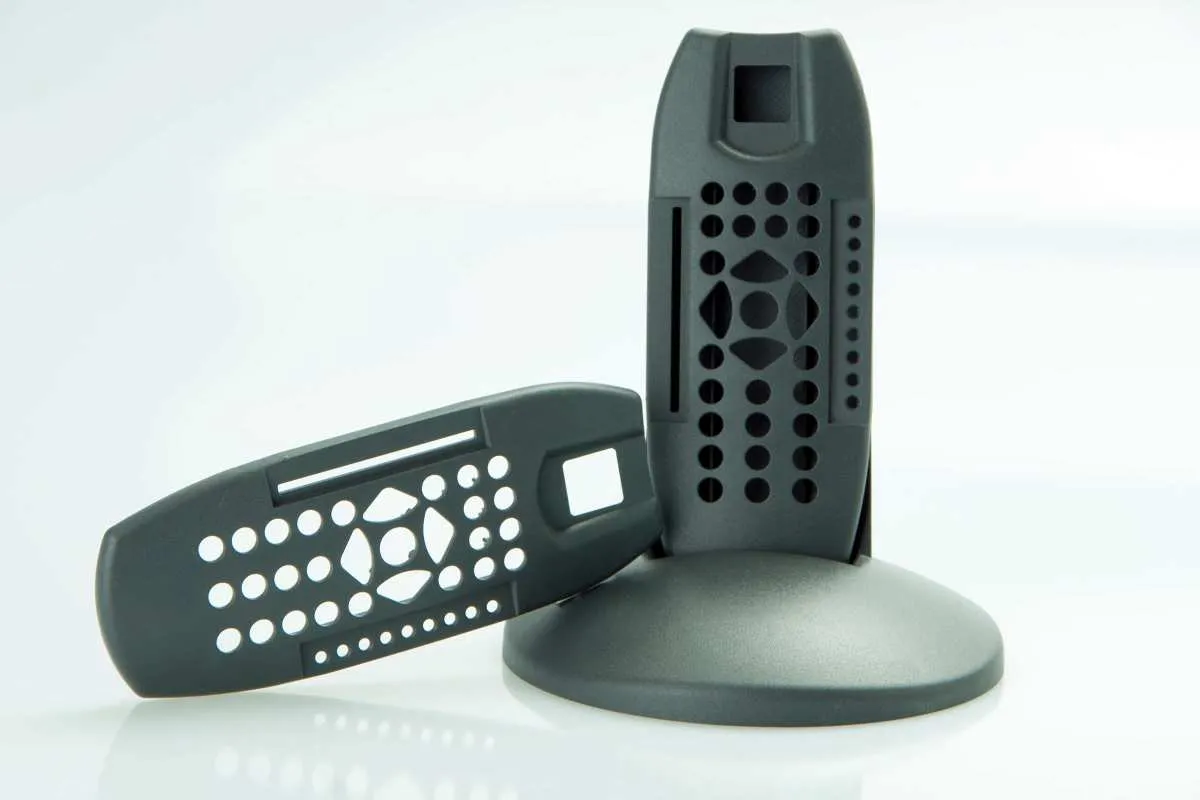
Injection moulding for remote control - Stocker Kunststoff GmbH
Find companies for plastic injection moulding
"Are you looking for a Plastic Injection Molding? At Techpilot you will find numerous contractors that offer plastic injection moulding. Europe's largest platform for drawing parts allows buyers to quickly and easily search for suitable plants for your parts.
The use of Techpilot is free for buyers. In addition to the detailed supplier search, you also have the possibility to write drawing parts online. You will then receive offers from suitable companies that you can easily and quickly compare with price, quality and delivery time.
Techpilot will support you at any time with your activities in the portal. The service team is extensively trained and technically extremely experienced. When you create your enquiries, you will receive a personal consultation by phone or e-mail on request.
More about plastic injection molding
Techpilot is Europe’s largest platform for the manufacturing industry.
For over 25 years, we’ve been connecting buyers, suppliers, and manufacturers that are the perfect match – enabling accurate price discovery for custom-made parts. Covering the full spectrum of mechanical components and supporting more than 280 manufacturing technologies, Techpilot is the market leader in Europe.Buyers gain instant access to qualified suppliers, full market transparency, and increased efficiency in their e-sourcing processes.
Suppliers benefit from high online visibility, extended media reach, and a profitable digital sales channel through Techpilot.
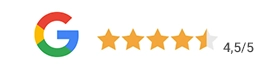
Lexicon Themes
- Metalworking (31)
- Plastic processing (8)
- Parts (8)
- Surface treatment (8)
- Welding (7)
- Machining (6)
- Sheet metal processing (6)
- Cutting (6)
- Turning (5)
- Manufacturing (5)
- Milling (4)
- Tool making (4)
- Suppliers (4)
- Casting (4)
- Procurement (4)
- Contract manufacturing (3)
- Profiles (3)
- Automation technology (2)
- Gearing & Thread (1)
- Forging (1)
- Wire processing (1)
- Heat treatment (1)