Sheet metal processing
Laser cutting, bending, and forming—sheet metal processing is complex and diverse. This part of the Techpilot Lexicon provides the foundational knowledge buyers need to assess manufacturing processes and ask the right questions during supplier communication.
Sheet metal processing
The sheet metalworking includes various for manufacturing custom sheet metal products. The starting material of the sheet metal processing is a sheet metal sheet or coarse sheet metal, which is brought into the desired shape and the desired design by cutting, forming, joining and finishing in various processing steps. Due to the multiplicity of different functions and applications, different methods for sheet metal processing are used in the metal processing industry. The most common methods include welding, cutting, bending, punching, shaping, rolling and joining.
> Learn moreFollow on composite tools
Woodening tools are manufactured in and are used to manufacture sheet metal components for industry. A follow-up composite tool usually comprises a plurality of stations on which a processing step or an operation on the component is carried out in each case.
> Learn moreLaser engraving
The laser engraving is a method of surface treatment using a high-energy laser beam for marking, marking or decoration of objects. The contactless method is characterized by high automation, durability and flexibility. The laser marking scores through versatile applications and is therefore very popular across the industry. engravings can be applied to many different materials and prove to be particularly durable and durable. Typical application areas are, for example, the production of type plates or the numbering of individual parts in series production.
> Learn moreLaser cutting
The laser cutting is part of the group of separating and is based on the separation of solid bodies by laser radiation. The method allows the user to cut complex contours from almost all conceivable materials. The use of continuous or pulsed laser radiation for cutting or cutting workpieces has far-reaching advantages compared to other methods. In the metal processing industry, laser cutting is particularly popular due to the high precision, efficiency and productivity. The combination of laser technology with highly automated CNC technology also ensures a high cost-effectiveness even with small batch sizes.
> Learn morePlasma fusion cutting
The plasma cutting is one of the thermal separation methods and allows the user to precisely cut sheets. The widespread method uses the thermal and kinetic energy of a plasma gas stream for liquefying and blowing out the material. The plasma cutting is used, in particular, when the material cannot be severed or only partially by conventional combustion cutting. The typical areas of application include cutting sheets of high-alloy steel, aluminium or copper. The method is distinguished by high cutting speeds, post-processing cuts, low heat input and low investment costs.
> Learn moreDeep drawing
We are the most important manufacturing technology in sheet metal forming. It can be used both for large series and for small series. Deep drawing with different metallic materials is also possible. Sheets that can be used in deep drawing include construction steel, stainless steel and aluminum, but also copper, titanium and brass. Deep-drawing is also possible for plastics, the technology being used here thermoforming. Deep drawing with tools The most typical variant of deep drawing is deep drawing with rigid tools from . These tools consist of a die, a die and a sheet metal holder or Holder. The cut sheet is fixed by the sheet metal holder. During the deep-drawing process, the punch presses the sheet over the die radius and presses it into the die, also called a drawing ring. The edges of sheet metal and stamps are rounded to prevent the sheet metal from tearing during forming. The change in the initial form is stronger in deep drawing than in most other forming methods. The finished product takes a completely new shape and hardly remembers the original workpiece. With correct application and the corresponding requirements, deep drawing is an extremely efficient, fast and proven method which is suitable for producing large quantities of uniform products. Deep-drawn parts are manufactured especially for the automotive industry, but there is also a need for deep-drawn parts in the gastronomy, the sanitary sector and the aircraft construction industry.
> Learn more
Techpilot is Europe’s largest platform for the manufacturing industry.
For over 25 years, we’ve been connecting buyers, suppliers, and manufacturers that are the perfect match – enabling accurate price discovery for custom-made parts. Covering the full spectrum of mechanical components and supporting more than 280 manufacturing technologies, Techpilot is the market leader in Europe.Buyers gain instant access to qualified suppliers, full market transparency, and increased efficiency in their e-sourcing processes.
Suppliers benefit from high online visibility, extended media reach, and a profitable digital sales channel through Techpilot.
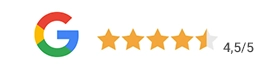
Lexicon Themes
- Metalworking (31)
- Plastic processing (8)
- Parts (8)
- Surface treatment (8)
- Welding (7)
- Machining (6)
- Sheet metal processing (6)
- Cutting (6)
- Turning (5)
- Manufacturing (5)
- Milling (4)
- Tool making (4)
- Suppliers (4)
- Casting (4)
- Procurement (4)
- Contract manufacturing (3)
- Profiles (3)
- Automation technology (2)
- Gearing & Thread (1)
- Forging (1)
- Wire processing (1)
- Heat treatment (1)