Welding
Welding remains a cornerstone in metal joining technology. This section explains key processes like MIG, MAG, and TIG—practically laid out to help technical buyers make the right supplier and process choices.
Component assembly
The concept of assembly assembly refers to the professional assembly of individual assemblies or components into a finished product. The assembly assembly is often carried out in industry on optimized assembly lines in order to realize time and cost advantages. The assembly is a very wide-ranging term that is used across the industry for a variety of assembly steps. The is applied both in the small and large series, depending on the complexity of the modules. The positioning of the assembly assembly in the production process is very flexible. The assembly can be used as an earlier intermediate step or can also represent the last step for the finished end product. In industry, assembly assembly is often carried out in wage production to rely on the expertise of specialized assembly experts.
> Learn moreManufacturing process
All processes for the production of geometrically determined bodies with predetermined technical properties and dimensions are referred to as manufacturing processes. In addition, material-changing methods such as hardening or soft annealing also belong to the manufacturing processes. Under the preamble of manufacturing methods, the individual methods are divided into six main groups according to their common features. These are described in more detail in DIN 8580 and categorized in subgroups and process variants. Manufacturing processes serve both for the production of semifinished products for further processing and for the production of final products.
> Learn moreLaser beam welding
The laser welding is one of the following and is used in the industry to connect metallic components and thermoplastics. The method is based on the punctual energy supply via a laser beam, wherein usually no additional material is used. Thanks to the energy-intensive laser beam, laser welding is characterized by a very high welding speed, a low thermal distortion in the component and a narrow and precise welding seam. It is therefore used in high-precision applications in , in the automotive industry, in steel construction, in shipbuilding, in aerospace and in other industries.
> Learn moreMAG welding
The MAG welding is part of the group of gas-protected metal arc welding processes, in which a wire electrode is melted under protective gas, and is widely used in industrial production for joining metallic materials. In the case of MAG welding, the permanent connection of metals is achieved using strong heat and welding aids. The heat input for the melting welding process causes an electric arc. The inserted wire electrode flows together with the melted base material as a welding additive and contributes to the formation of the weld seam. The method is distinguished by a high processing speed and the possibility of automation. It is therefore particularly suitable for industrial applications.
> Learn moreSpot welding
The spot welding is also referred to as resistance spot welding and is one of the welding methods without using protective gas. The method is based on the punctual heating and liquefaction of two workpieces pressed on one another by applying a strong voltage. Compared to other welding processes, spot welding is characterized by good productivity, a high degree of automation and a low material distortion. For this reason, the joining method is used primarily in bodywork and vehicle construction, in sheet metal processing and in the electrical industry.
> Learn moreFriction stir welding
The friction welding (see: Friction Stir Welding) belongs to the group of friction welding processes and is particularly suitable for joining non-ferrous metals with low melting temperature and mixed compounds. The method is based on the use of a rotating pin which is guided between the contact surfaces of two workpieces. The friction heat produced thereby ensures a plasticization of the material and allows welding of the workpieces. Stir friction welding produces particularly high-quality welded joints with excellent fatigue properties and is therefore very popular in the metal processing industry.
> Learn moreTIG welding
The tungsten inert gas welding (IG welding) belongs to the group of melt welding processes and is characterized by particularly clean processing, high seam qualities and almost universal applicability in the metal sector. Due to the particularly precise tuning of the welding current to the respective welding task, the welding method is particularly suitable for root positions and forced positions. For this reason, WIG welding enjoys great popularity in tasks with high standards of precision and seam quality, such as pipeline and apparatus construction, power plant construction and chemical industry.
> Learn more
Techpilot is Europe’s largest platform for the manufacturing industry.
For over 25 years, we’ve been connecting buyers, suppliers, and manufacturers that are the perfect match – enabling accurate price discovery for custom-made parts. Covering the full spectrum of mechanical components and supporting more than 280 manufacturing technologies, Techpilot is the market leader in Europe.Buyers gain instant access to qualified suppliers, full market transparency, and increased efficiency in their e-sourcing processes.
Suppliers benefit from high online visibility, extended media reach, and a profitable digital sales channel through Techpilot.
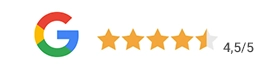
Lexicon Themes
- Metalworking (31)
- Plastic processing (8)
- Parts (8)
- Surface treatment (8)
- Welding (7)
- Machining (6)
- Sheet metal processing (6)
- Cutting (6)
- Turning (5)
- Manufacturing (5)
- Milling (4)
- Tool making (4)
- Suppliers (4)
- Casting (4)
- Procurement (4)
- Contract manufacturing (3)
- Profiles (3)
- Automation technology (2)
- Gearing & Thread (1)
- Forging (1)
- Wire processing (1)
- Heat treatment (1)