Metalworking
Metalworking includes a wide range of manufacturing methods such as turning, milling, grinding, and stamping. This Lexicon section explains key processes and terminology in a clear and practical way—ideal for technical buyers who want to understand capabilities and applications in detail.
Additive manufacturing
The additive manufacturing term refers to all , in which material layer is applied to a three-dimensional component for layer. The forming method has its strengths, especially in highly complex structures, and enables the user to have a high degree of design freedom and functional optimization. To date, additive manufacturing has been used predominantly in prototype construction and in the production of small batch sizes. Meanwhile, however, the technology is increasingly moving into series production, as it enables the strong individualization of products and gives the user the opportunity to differentiate themselves on the market.
> Learn moreComponent assembly
The concept of assembly assembly refers to the professional assembly of individual assemblies or components into a finished product. The assembly assembly is often carried out in industry on optimized assembly lines in order to realize time and cost advantages. The assembly is a very wide-ranging term that is used across the industry for a variety of assembly steps. The is applied both in the small and large series, depending on the complexity of the modules. The positioning of the assembly assembly in the production process is very flexible. The assembly can be used as an earlier intermediate step or can also represent the last step for the finished end product. In industry, assembly assembly is often carried out in wage production to rely on the expertise of specialized assembly experts.
> Learn moreBlacking
Brunning is a surface process for producing a black protective layer on iron-containing surfaces. The aim of the bronification is primarily to protect against corrosion, whereby a decorative, antique appearance is frequently also achieved. The Breasting is defined in the standard DIN 50983 and is usually based on the immersion of the workpiece to be treated into an acidic or alkaline solution, the broaching agent. This process forms a black mixed oxide layer on the surface of the workpiece, which is also referred to as “stainless grate”. Black-oxideating is therefore not a coating, but a conversion of material.
> Learn moreCNC turning
For CNC it is an automated for the production of rotationally symmetrical components. The process offers far-reaching advantages over conventional production on a rotary bench and is predominantly used in the metal processing industry. CNC lathe is characterized by a high degree of automation and convinces above all by a high repeatability as well as the possibility to efficiently manufacture even complex rotationally symmetrical geometries. The range of applications of CNC lathes is diverse and ranges from the production of CNC lathes for the automotive industry and machine and plant construction to the production of small parts for medical technology and electrical engineering. Both small and medium series and large series can be manufactured economically by CNC machining.
> Learn moreCNC milling
The CNC milling is one of the cutting and is based on the use of automated CNC machine tools that produce workpieces with high precision using modern control technology. Milling with CNC machine tools is nowadays used primarily in the metal processing industry and allows users to manufacture inexpensive workpieces with the highest demands of accuracy and complexity. CNC milling machines are able to realize cutting speeds of up to 10,000 revolutions per minute and thereby achieve economic advantages in particular in series production. The CNC milling is not limited to metal processing, but is also used in plastic and wood processing.
> Learn moreTurning
The turning is one of the most important cutting methods and is used to manufacture cylindrical components. A single-edged tool (e.g. a rotary chisel made of high-speed steel) is guided to a rotating component in order to remove successive chips and to achieve the desired geometric shape.
> Learn moreSurface hardening
The use hardness refers to a thermochemical process in which the mechanical properties of the edge layer of metallic components are improved in a targeted manner. In this case, the surface is first carbonized, then hardened and then let on. The use hardening is carried out in the hardening process and allows the user to impart a significantly higher surface hardness to the edge layer of the workpiece. Use-hardened components are distinguished by a correspondingly high wear resistance with increased bending fatigue strength and are thus particularly predestined for use in transmission technology.
> Learn moreAnodizing
The anodizing is a process for surface treatment of aluminum. By means of anodic oxidation, a protective layer can be produced on the metal, which prevents the natural, uncontrolled oxidation of the metal by reaction with oxygen from the ambient air. The special feature of the method is that, unlike for example in, no layer is applied, but a conversion of the uppermost aluminum layer takes place. This layer serves not only for corrosion protection, it can also be colored by means of an additional process step. Resistance and optics of the anodized layer can be influenced by the suitable choice of the process parameters.
> Learn moreExtrusion
The extrusion is a forming process which is mainly used for thermoplastics. The plastic is pressed through a shaping opening as a viscous mass under high pressure and high temperature. Extrusion is one of the most widely used processes in the plastics processing industry and, thanks to its wide range of advantages in terms of efficiency, has gained great importance in the production of plastic parts. An extruder is used for extrusion, which is also referred to as a screw press. In principle, a distinction is made between the single-screw extruder and the twin-screw extruder.
> Learn moreFollow on composite tools
Woodening tools are manufactured in and are used to manufacture sheet metal components for industry. A follow-up composite tool usually comprises a plurality of stations on which a processing step or an operation on the component is carried out in each case.
> Learn moreMilling
Milling refers to a cutting which is used for manufacturing components with a specific geometric contour. Thanks to its high efficiency, productivity and precision, milling is particularly popular in metal-processing production technology. The milling can be used both for the processing of planar surfaces and for the production of complex, three-dimensional contours. A milling tool with geometrically determined cutting edges is used and, during the milling process, material is removed from a workpiece by a rotating circular movement. Milling can now be carried out both manually and using state-of-the-art CNC machine tools with a high degree of automation.
> Learn moreElectroplating
The electroplating (also electroplating) is a process from surface and layer technology for electrochemical deposition of metals on metallic or metallized surfaces using an electrolyte and direct current. The galvanic coating usually serves to protect the workpieces from corrosion or to increase the wear resistance of their surface. The method is particularly often used for coating steels with metals of a suitable property profile. Such metallic coatings have a wide field of application since they obtain the metallic appearance of the workpieces and the electrical conductivity.
> Learn moreDrop forging
The forging is part of the group of forming methods. In industry, it is mainly used for the automated production of metal components that are subject to dynamic loads. The use of at least two shaping tools, or sinks, which move relative to one another is characteristic of the method. Forming by means of sinks is the most widely used forging method in industrial practice. The method is distinguished by the good material utilization, the die forging parts by the advantageous ratio between weight and strength. From the likewise widespread free-form forgings, the method is distinguished by the superior dimension accuracy.
> Learn moreGravity casting moulds
A mold is a metallic mold used for the production of precise workpieces with good surface quality. Moulds often consist of cast iron or copper plates and are widely used in metalworking industry. The mold is the technical basis of the mold casting process and has proved successful in the production of large forging blanks, slabs for sheet metal products, billets for wire, rod and profile products and other components. In the mold casting process, the metallic melt is poured into the mold via the above-lying injection and cures there. Depending on the casting process, a mold can be used up to 100,000 times, resulting in a high cost.
> Learn moreLaser engraving
The laser engraving is a method of surface treatment using a high-energy laser beam for marking, marking or decoration of objects. The contactless method is characterized by high automation, durability and flexibility. The laser marking scores through versatile applications and is therefore very popular across the industry. engravings can be applied to many different materials and prove to be particularly durable and durable. Typical application areas are, for example, the production of type plates or the numbering of individual parts in series production.
> Learn moreLaser cutting
The laser cutting is part of the group of separating and is based on the separation of solid bodies by laser radiation. The method allows the user to cut complex contours from almost all conceivable materials. The use of continuous or pulsed laser radiation for cutting or cutting workpieces has far-reaching advantages compared to other methods. In the metal processing industry, laser cutting is particularly popular due to the high precision, efficiency and productivity. The combination of laser technology with highly automated CNC technology also ensures a high cost-effectiveness even with small batch sizes.
> Learn moreLaser beam welding
The laser welding is one of the following and is used in the industry to connect metallic components and thermoplastics. The method is based on the punctual energy supply via a laser beam, wherein usually no additional material is used. Thanks to the energy-intensive laser beam, laser welding is characterized by a very high welding speed, a low thermal distortion in the component and a narrow and precise welding seam. It is therefore used in high-precision applications in , in the automotive industry, in steel construction, in shipbuilding, in aerospace and in other industries.
> Learn moreMAG welding
The MAG welding is part of the group of gas-protected metal arc welding processes, in which a wire electrode is melted under protective gas, and is widely used in industrial production for joining metallic materials. In the case of MAG welding, the permanent connection of metals is achieved using strong heat and welding aids. The heat input for the melting welding process causes an electric arc. The inserted wire electrode flows together with the melted base material as a welding additive and contributes to the formation of the weld seam. The method is distinguished by a high processing speed and the possibility of automation. It is therefore particularly suitable for industrial applications.
> Learn morePlasma fusion cutting
The plasma cutting is one of the thermal separation methods and allows the user to precisely cut sheets. The widespread method uses the thermal and kinetic energy of a plasma gas stream for liquefying and blowing out the material. The plasma cutting is used, in particular, when the material cannot be severed or only partially by conventional combustion cutting. The typical areas of application include cutting sheets of high-alloy steel, aluminium or copper. The method is distinguished by high cutting speeds, post-processing cuts, low heat input and low investment costs.
> Learn moreCon rod
A connecting rod is also referred to as a connecting rod or push rod and connects the crankshaft to the piston in a crank drive. The connecting rod converts the linear movement of the piston into a linear oscillating axial movement and thereby allows the force transmission in the vehicle train. As a rule, connecting rods are made from C70 steel or from microalloy steels. In addition, compensation steels or titanium are also used in the sports motor sector. Connecting rods in large series are frequently forged, sintered or cast, whereas in productions with small numbers a cutting production of metal pieces is preferably used.
> Learn moreSpot welding
The spot welding is also referred to as resistance spot welding and is one of the welding methods without using protective gas. The method is based on the punctual heating and liquefaction of two workpieces pressed on one another by applying a strong voltage. Compared to other welding processes, spot welding is characterized by good productivity, a high degree of automation and a low material distortion. For this reason, the joining method is used primarily in bodywork and vehicle construction, in sheet metal processing and in the electrical industry.
> Learn moreFriction stir welding
The friction welding (see: Friction Stir Welding) belongs to the group of friction welding processes and is particularly suitable for joining non-ferrous metals with low melting temperature and mixed compounds. The method is based on the use of a rotating pin which is guided between the contact surfaces of two workpieces. The friction heat produced thereby ensures a plasticization of the material and allows welding of the workpieces. Stir friction welding produces particularly high-quality welded joints with excellent fatigue properties and is therefore very popular in the metal processing industry.
> Learn moreSand blasting
The sandblasting is one of the processes of surface treatment and is mainly used for removing rust, soiling, colour residues and other impurities. In the method, a blasting agent is thrown at high speed onto the surface to be treated. Sandblasting enjoys great popularity in the metalworking industry and in construction. On the one hand, the method can be used for efficient removal of impurities and for the preparation of surfaces, but on the other hand also serves for the production of optical effects such as, for example, the matting of glass or stone surfaces.
> Learn moreWorm gear
A worm gear is a screw-rolling gear which transfers the rotational movement of a cylindrical shaft to a rotating gear which is offset by 90°. Snail transmissions allow a particularly high transmission to narrow space and are therefore outstandingly suitable for demanding space conditions. Snail gears work highly precise, are very powerful and in addition are able to reliably compensate for axial offsets. For this reason, the low-noise and insensitive transmissions are used worldwide in demanding applications such as conveyor systems, extrusion machines, separation machines or profile machining machines.
> Learn moreSteel profiles
Steel profiles are steel components which have the same cross-section over their entire length. Steel profiles are usually produced by rolling, drawing or pressing and are used as construction steel or for the production of rails, ladders or struts. When using steel profiles, it is crucial to tune the decisive material or component parameters to the application. It should be ensured that the static moment, the moment of resistance and the moment of inertia of the surface correspond to the load requirements of the respective application.
> Learn morePunching tool
The punching tool is one of the typical industrial needs and is usually manufactured by a . Stamping tools consist essentially of a die, a die and the scraper.
> Learn moreBar extrusion
The extrusion is one of the pressure-forming and is used to manufacture metallic profiles with different geometries. The process is used in the metal processing industry and in the construction industry, inter alia, for the production of hollow profiles. The extrusion allows the user to produce metallic profiles also with complex shapes such as irregular prismatic profiles. The technology is distinguished in particular by a high cost-effectiveness compared to alternative methods at low unit numbers. The extrusion is mainly used for aluminum components, but also for other materials.
> Learn moreTrowalizing
The trolling is also referred to as sliding grinding or sliding cutting and is a separating method of surface machining. In this case, metal workpieces together with a grinding means are usually introduced into a rotating drum in order to remove material in a targeted manner. Trowalization is described in the DIN 8589 standard, together with the lapping and polishing, and is referred to as sliding panels. The process is very popular in the metal processing industry, as it can perform several tasks from and rounding over smoothing and polishing to matting and grinding. The desired result of the surface treatment can be brought about in a targeted manner by the variation of the machines and grinding means used.
> Learn moreWater jet cutting
The water jet cutting is a separate , where water is used under high pressure to cut through various materials. The water jet cutting is regarded as a particularly environmentally friendly, economical and material-friendly separation process. Depending on the material to be separated, pure water or water with an abrasive addition is optionally used in water jet cutting. While pure water is suitable for cutting soft materials such as plastics, foams, films and paper, an abrasive water jet is required for separating steel, ceramics or glass. The water jet cutting has proven itself primarily in the cutting of composites and is applied across the industry due to its extensive advantages.
> Learn moreTIG welding
The tungsten inert gas welding (IG welding) belongs to the group of melt welding processes and is characterized by particularly clean processing, high seam qualities and almost universal applicability in the metal sector. Due to the particularly precise tuning of the welding current to the respective welding task, the welding method is particularly suitable for root positions and forced positions. For this reason, WIG welding enjoys great popularity in tasks with high standards of precision and seam quality, such as pipeline and apparatus construction, power plant construction and chemical industry.
> Learn moreMachining
The preamble of machining includes a series of , which are characterized by the machining of workpieces for producing a desired shape.
> Learn more
Techpilot is Europe’s largest platform for the manufacturing industry.
For over 25 years, we’ve been connecting buyers, suppliers, and manufacturers that are the perfect match – enabling accurate price discovery for custom-made parts. Covering the full spectrum of mechanical components and supporting more than 280 manufacturing technologies, Techpilot is the market leader in Europe.Buyers gain instant access to qualified suppliers, full market transparency, and increased efficiency in their e-sourcing processes.
Suppliers benefit from high online visibility, extended media reach, and a profitable digital sales channel through Techpilot.
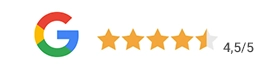
Lexicon Themes
- Metalworking (31)
- Plastic processing (8)
- Parts (8)
- Surface treatment (8)
- Welding (7)
- Machining (6)
- Sheet metal processing (6)
- Cutting (6)
- Turning (5)
- Manufacturing (5)
- Milling (4)
- Tool making (4)
- Suppliers (4)
- Casting (4)
- Procurement (4)
- Contract manufacturing (3)
- Profiles (3)
- Automation technology (2)
- Gearing & Thread (1)
- Forging (1)
- Wire processing (1)
- Heat treatment (1)