Surface hardening
The use hardness refers to a thermochemical process in which the mechanical properties of the edge layer of metallic components are improved in a targeted manner. In this case, the surface is first carbonized, then hardened and then let on.
The use hardening is carried out in the hardening process and allows the user to impart a significantly higher surface hardness to the edge layer of the workpiece. Use-hardened components are distinguished by a correspondingly high wear resistance with increased bending fatigue strength and are thus particularly predestined for use in transmission technology.
The individual working steps during use hardening
The technical basis for use hardening is the enrichment of the edge layer with carbon in a medium suitable for carbonization. This process results in a gradient with different carbon content in the workpiece: While the edge layer has a high proportion of carbon, the content decreases toward the core.
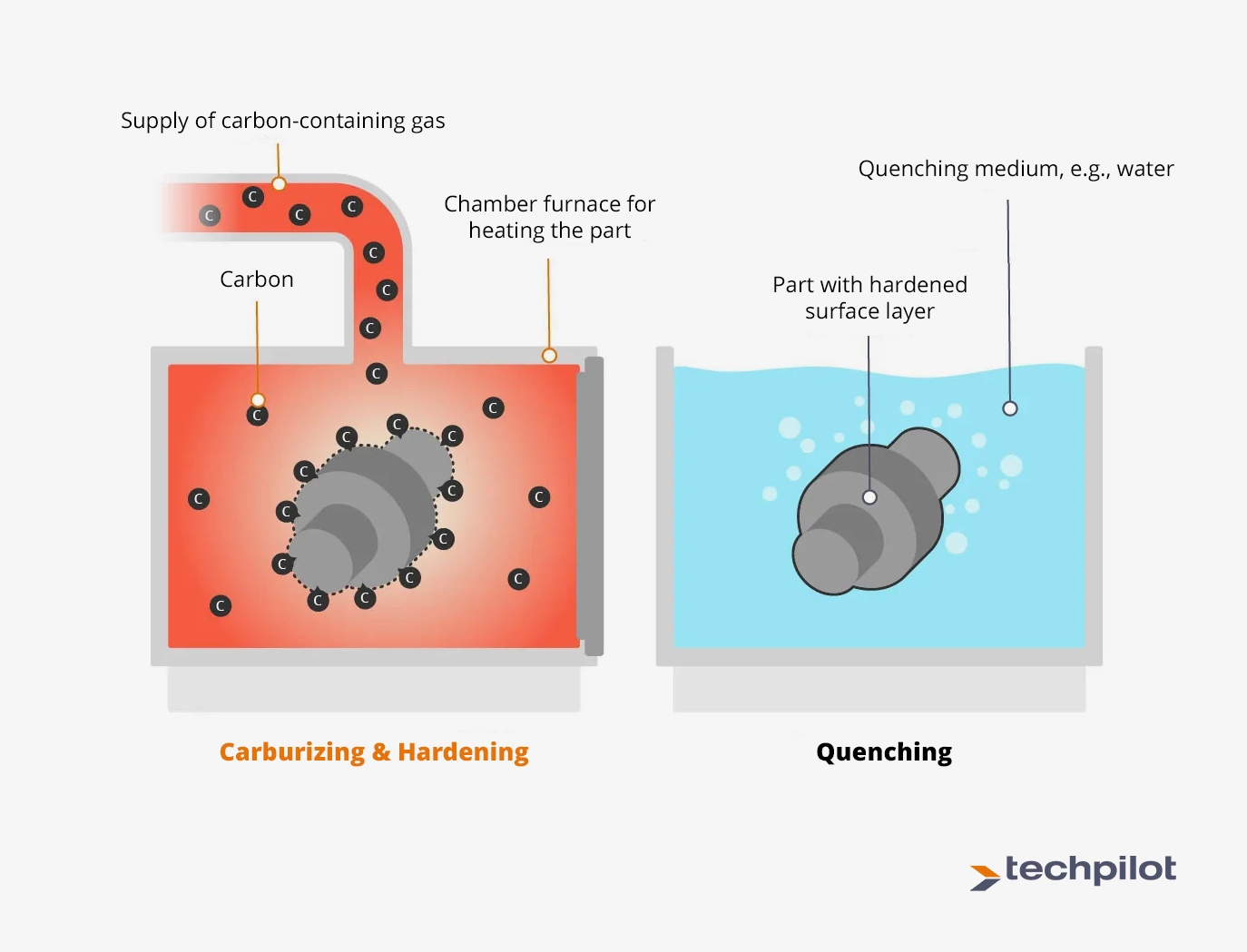
Use hardening by gas atmosphere
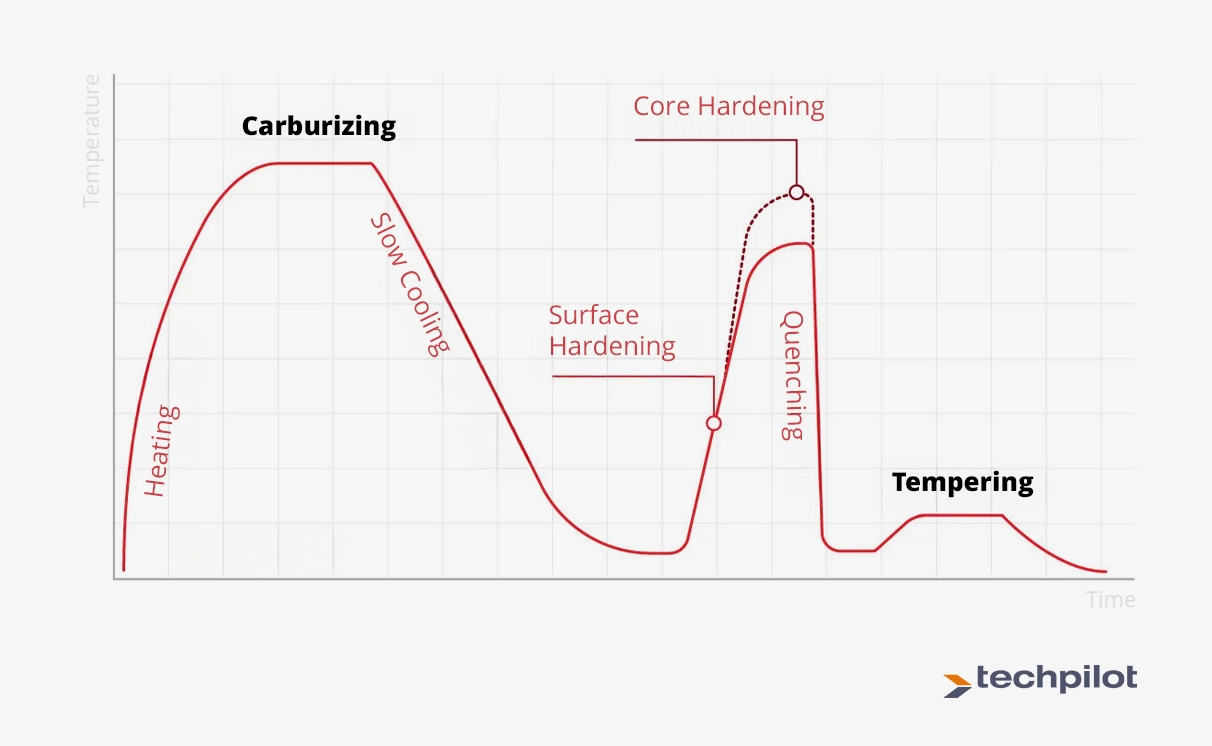
Application Hardening Phases
In the following, the individual steps are described in detail from coaling to starting:
Building
In the case of coaling, the workpiece is first exposed to a temperature of 880 °C to 950 °C (usually used use steels). By this heat treatment, the uppermost layer in the workpiece is first enriched with carbon. As a result, the carbon then also diffuses in the direction of the component core. The prerequisite for coaling is a suitable medium for carbon release. This may be, for example, a salt melt, a calcination powder or granules or a gas atmosphere. After coaling, we first slowly cooled the workpiece before hardening begins.
Hears
The subsequent hardening is necessary in order to impart the desired high strength and surface hardness to the workpiece, wherein the core retains its tough properties. The resulting hardness is decisively determined by the carbon content in the edge layer during use hardening. In addition, factors such as the toughness of the steel and the intensity of the quenching medium are crucial. Examples of suitable quenching medium are liquid media such as water, hardness oil, salt melt and polymer or also gaseous media such as nitrogen or helium.
Applause
The last step, the start-up of the workpiece, is used for the purposeful removal of stresses in the edge layer. During use hardening, the starting is typically carried out at temperatures of about 160° C. to 220° C., the edge layer gaining ductility.
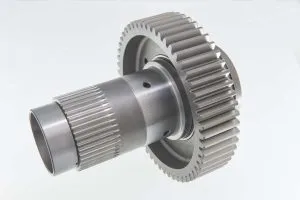
Spur shaft carbonized and hardened

Hollow drills hardened
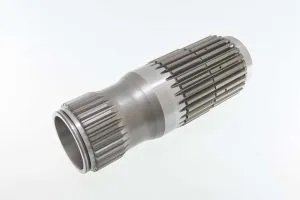
Hollow shaft carbonized and hardened
In the region of the heat-treating methods, the use hardening is distinguished by a number of advantages. These include, inter alia, the following aspects:
- Flexibility:
The method allows the precise adjustment of the desired hardness depths. - Material properties:
While wear resistance and hardness of the edge layer are specifically increased, the core remains tough. - Exchangeability:
Through the use hardening, both the bending resistance of the component
as well as significantly increase the fatigue strength. - Partial curing:
Depending on the application, a specific region of the workpiece can also be carburized in a targeted manner.
Other areas are covered with a special paste.
Carbonitriding is also used as an alternative to hardening. In this variant, not only carbon but also nitrogen is introduced into the edge layer.
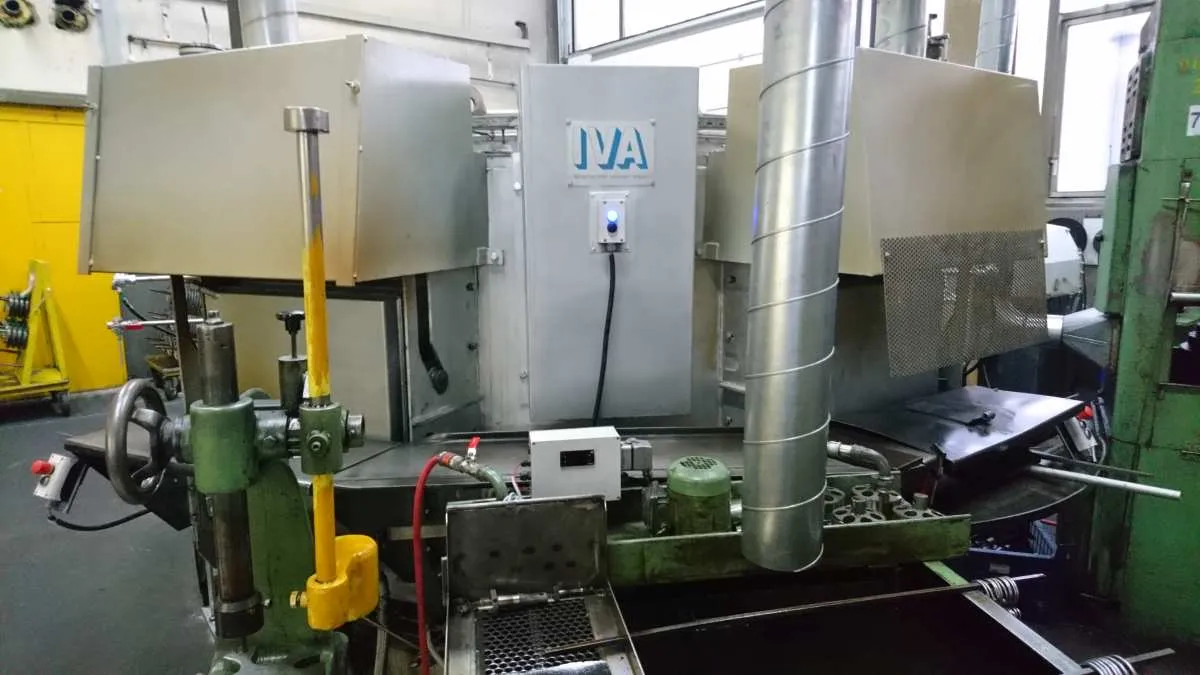
Rotary hardening furnace
What is the use hardness used for?
The use hardness is always used in the metal processing industry when components with high wear resistance and good bending resistance are to be produced with high durability. Typical applications include the production of drive parts such as gear components and gear wheels. Due to the dynamic load requirements and constant contact with other movable parts, these must meet the highest demands on bending resistance and wear resistance.
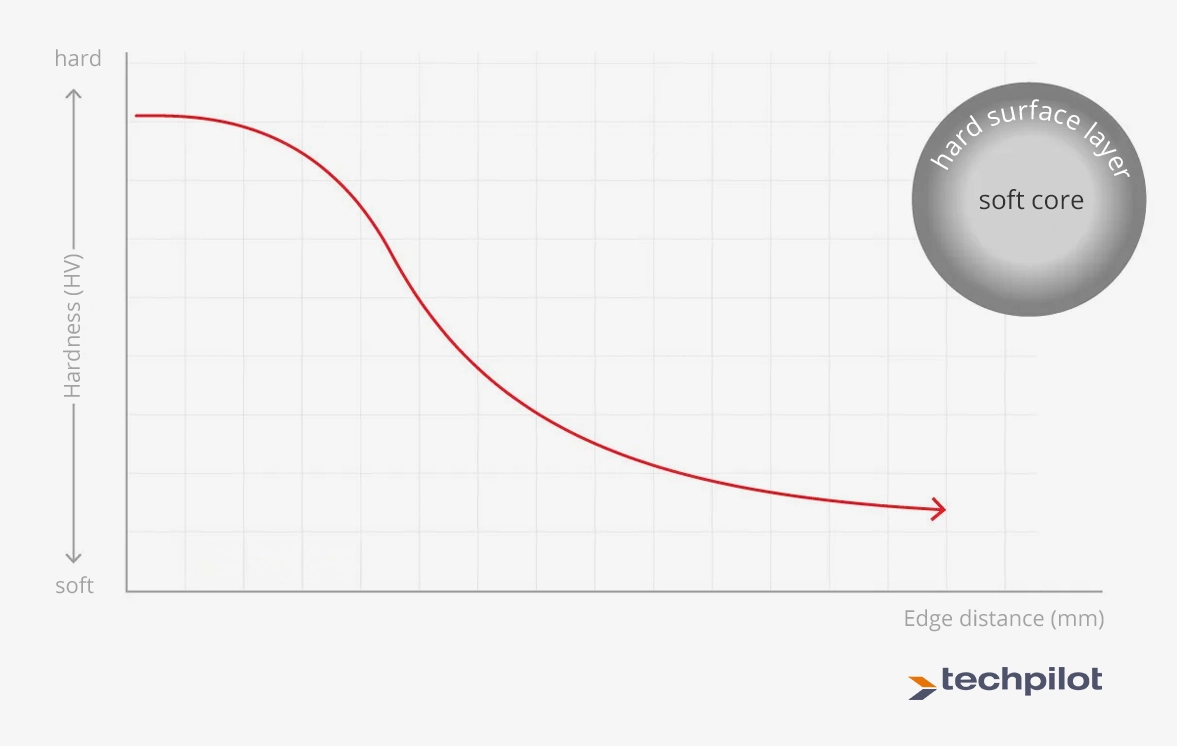
Application hardness depth
Which materials are suitable for use hardening?
Since the targeted increase in the carbon content is the focus during use hardening, use steels or stainless steels with a comparatively small proportion of carbon are predominantly suitable for the process. Unalloyed or low alloy steel having a base carbon content of less than 0.25% by mass is usually used. Typical materials for use hardening are, for example:
- 6587/18CrNiMo7-6
- 0301/C10
- 7131/16MnCr5
- 7147/20MnCr5
Find companies for toughening
If you are looking for Surface Hardening, Techpilot will find a variety of companies specializing in this field. More than 24,000 suppliers are registered at Europe's largest platform for drawing parts.
Buyers use all Techpilot functions for free. These include the extensive supplier search and the online request process. Write out your parts in a few minutes and receive offers from interested companies worldwide. The practical offer comparison makes it easier to choose a suitable company.
In order to support you in the best possible way, the Techpilot team is at your disposal at any time. The trained employees know themselves well in the industry and help you create your inquiries.
Examples of jobs in the Techpilot marketplace
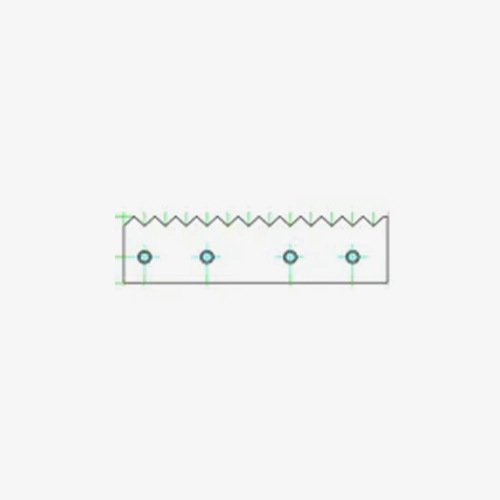
Application Hardening - Use/Construction Steel
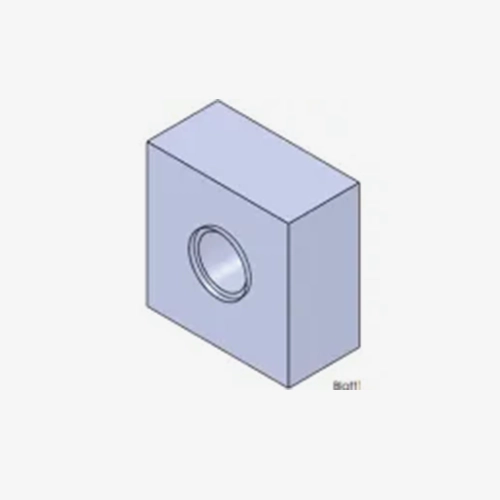
Request for hardeners - construction steel
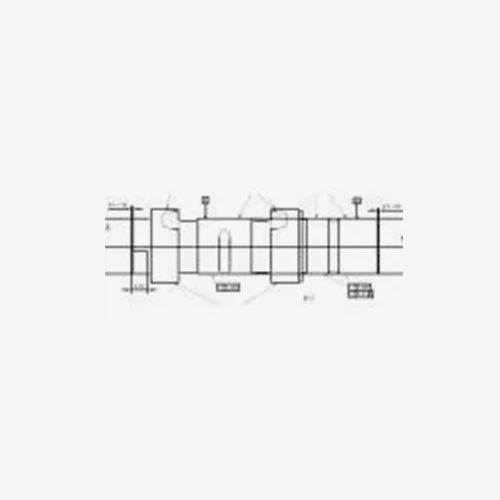
Request for use hardnesses -Motorradnockenwelle
More on the topic
Techpilot is Europe’s largest platform for the manufacturing industry.
For over 25 years, we’ve been connecting buyers, suppliers, and manufacturers that are the perfect match – enabling accurate price discovery for custom-made parts. Covering the full spectrum of mechanical components and supporting more than 280 manufacturing technologies, Techpilot is the market leader in Europe.Buyers gain instant access to qualified suppliers, full market transparency, and increased efficiency in their e-sourcing processes.
Suppliers benefit from high online visibility, extended media reach, and a profitable digital sales channel through Techpilot.
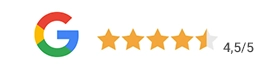
Lexicon Themes
- Metalworking (31)
- Plastic processing (8)
- Parts (8)
- Surface treatment (8)
- Welding (7)
- Machining (6)
- Sheet metal processing (6)
- Cutting (6)
- Turning (5)
- Manufacturing (5)
- Milling (4)
- Tool making (4)
- Suppliers (4)
- Casting (4)
- Procurement (4)
- Contract manufacturing (3)
- Profiles (3)
- Automation technology (2)
- Gearing & Thread (1)
- Forging (1)
- Wire processing (1)
- Heat treatment (1)