Manufacturing process
All processes for the production of geometrically determined bodies with predetermined technical properties and dimensions are referred to as manufacturing processes. In addition, material-changing methods such as hardening or soft annealing also belong to the manufacturing processes.
Under the preamble of manufacturing methods, the individual methods are divided into six main groups according to their common features. These are described in more detail in DIN 8580 and categorized in subgroups and process variants. Manufacturing processes serve both for the production of semifinished products for further processing and for the production of final products.
What does the term manufacturing process mean?
In principle, all methods used in manufacturing technology for producing a workpiece are referred to as manufacturing methods. The concept of the manufacturing process is to be delimited by the process technology which describes the production of bodies without a certain form.
As a rule, different manufacturing methods are combined with one another for producing a workpiece. The individual production methods can be carried out either manually or automatically.
In the metal- or plastic-processing industry, the production of a workpiece usually begins with a primordial process such as casting. A body with a defined shape is produced from an undefined material mass. This body can then be reshaped, machined, joined or coated in the further process steps. In the last step, depending on the desired result, the material properties of the material are often changed in a targeted manner.
What is the standard DIN 8580?
DIN 8580 is the valid standard for classification of manufacturing processes. The standard divides all manufacturing processes into six main groups according to the type of process. It should be borne in mind that this classification is mainly widespread in the metalworking industry and can only be used to a limited extent in other industries.
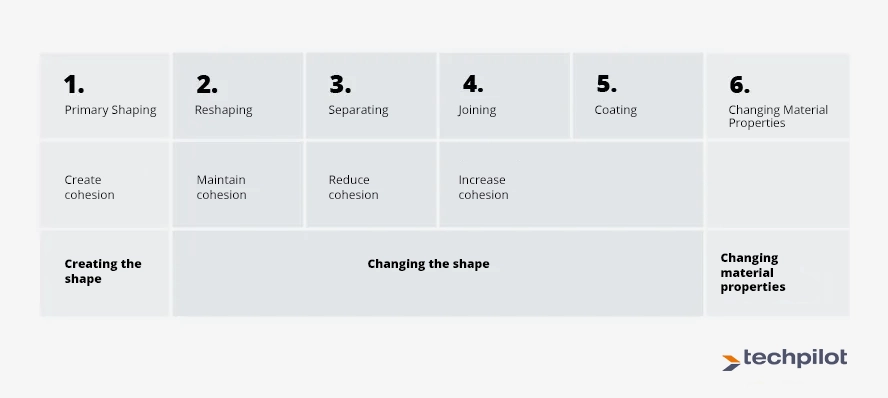
Manufacturing method according to DIN 8580
The categorization of the production methods in six main groups is essentially based on whether the process step creates, increases, decreases or maintains the material concentration of the workpiece. The six main groups are:
- Original forms
- Forming
- Separation
- Add
- Coating
- Change fabric properties
What groups are there?
The six main groups will be described in more detail below and deposited with examples from the production technology:
Urforms: The original form is used to produce a body with a defined geometric shape from a previously formless material. Depending on the method, the starting material can be either liquid, vaporous or also in powder form. Examples of original manufacturing methods are
- Casting (bloc or continuous casting, casting)
- Injection molding
- Rapid prototyping
- Pressing
- Powder metallurgy
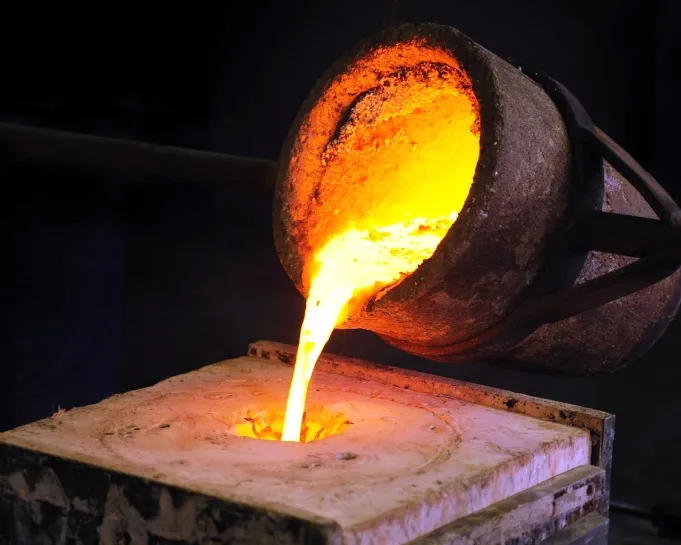
Sand moulding at proXplus AG
Reforms: Forming manufacturing processes aim to generate permanent shape changes in workpieces from solid raw parts. No material is removed or added, the mass of the blank corresponds to the mass of the workpiece after machining. The most important re-forming manufacturing processes include:
- Forging
- Rolling
- Flow presses
- Strange presses
- Deep pulling
- Bending
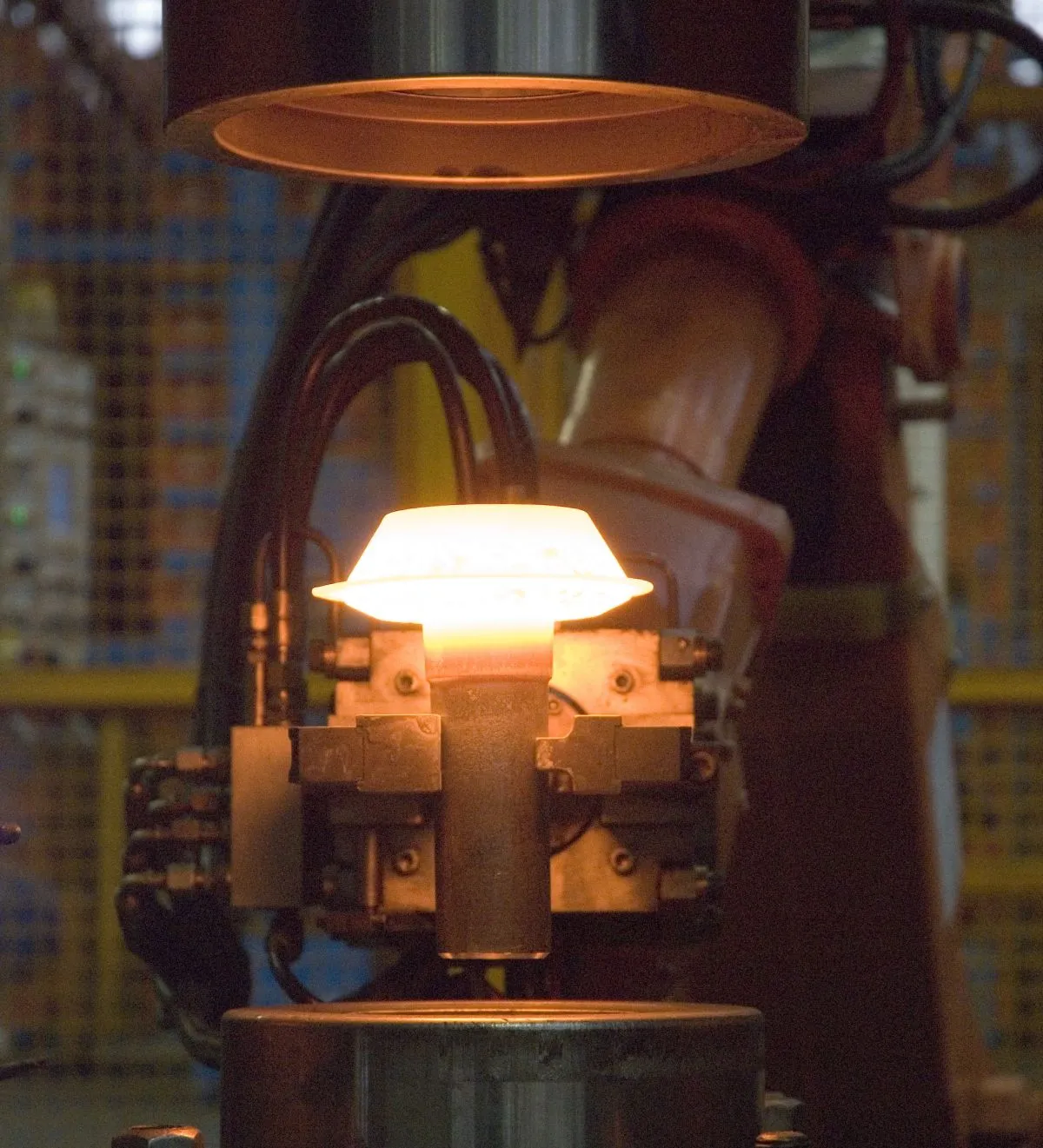
Forging with Poppi Ugo Euroforge S.p.A.
Traces: The separating processes are characterized in that the cohesion of the material is reduced during processing. All cutting processes, which are important both in the metal and plastics processing industry, are part of this main group. Some examples at a glance:
- Milling
- Sawing
- Plane
- Drilling
- Stamping
- Burning cutting
- Laser cutting
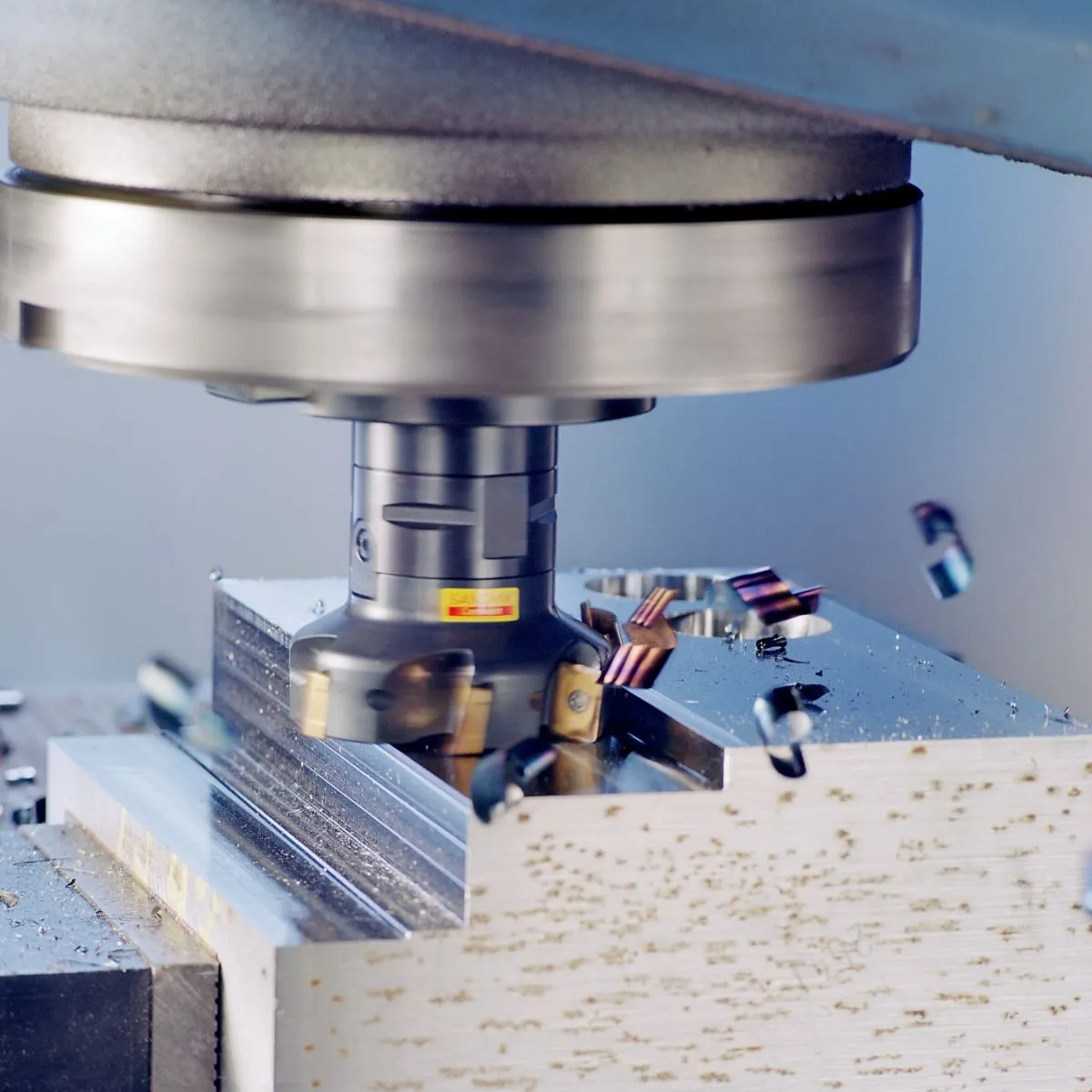
Milling at the company SIMON Parts Processing GbR
Five: Joining methods serve for the long-lasting connection of a plurality of workpieces and are characterized in that the substance concentration is increased. Some examples of joining manufacturing processes:
- Welding
- Soldering
- Adhesive
- Screws
- Rivets
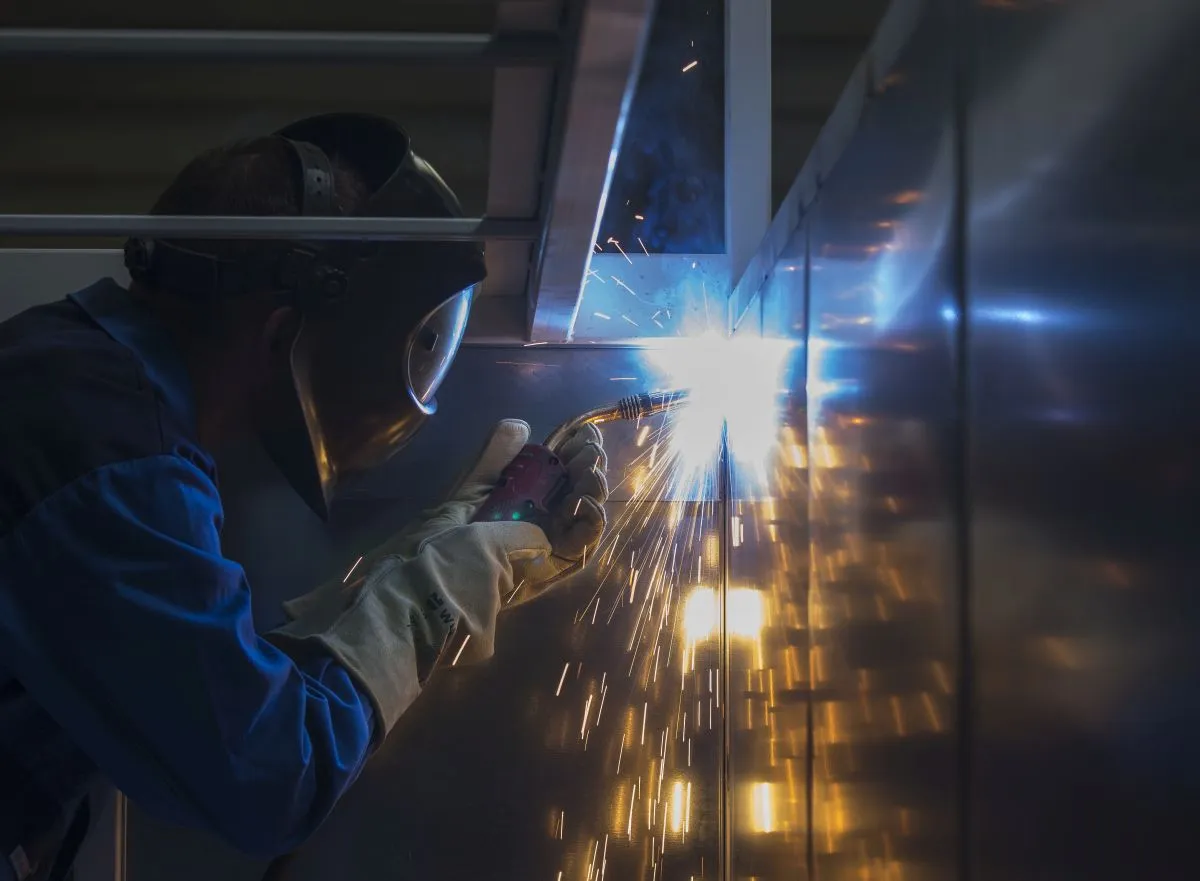
Welding at Gruber GmbH Metallbau & Blechbearbeitung
Coating: Coating production methods aim to produce a firmly adhering layer on the workpiece. The surface of the material can thereby be changed in its technical properties, such as resistance, corrosion resistance or conductivity. The typical procedures of this group include:
- Painting
*Electroplating - Application welding
- Powder coating
- Fire galvanized
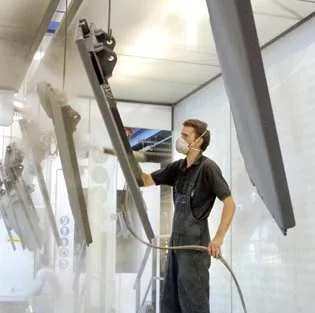
Powder coating at Jud GmbH & Co. KG
Change fabric properties: All methods for changing the material properties are assigned to the main group 6 . These include the following manufacturing steps:
- Lighting
- Curing
- Chemical reactions
DIN 8580 uses a subdivision system to facilitate the allocation and categorization of the individual production processes. A separate order number is assigned to each method: The main group determines the first digit and the subcategory determines the second digit.
An example: The main group joining is categorized by the order number 4. The subcategory of brazing carries the number 7 and the method of brazing is second within this subcategory. According to DIN 8580, the hard soldering has the number 4.7.2. Depending on the procedure, the order number is also up to five digits.
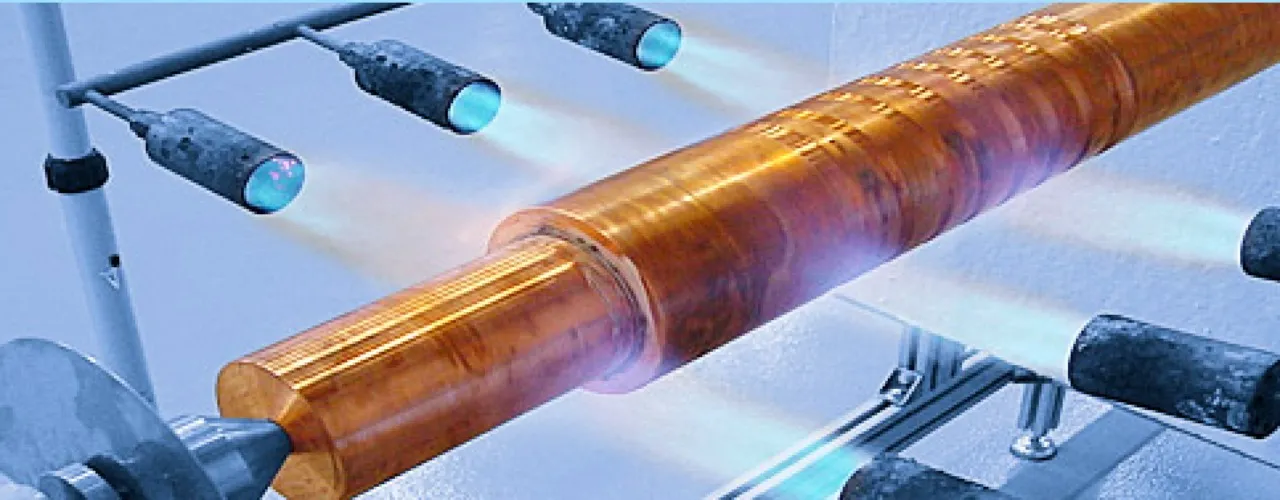
Hartlöten at Reltas AG
Find companies for 280 different manufacturing processes
Techpilot connects buyers and suppliers in the manufacturing industry. With the help of Europe's largest Supplier pool, exactly matching companies can be found quickly and easily. Various filter functions help to specify all requirements to the supplier in a structured manner. Interesting companies can then be contacted directly via the platform, if necessary also with a specific request. On the public database, buyers will submit your part requests to reach as many suppliers as possible. The incoming offers are quickly and clearly compared – this saves a lot of time and effort while offering valuable market insights.
The use of Techpilot is free for buyers. Telephone support from technically trained employees is part of the service, as is the help of creating inquiries.
Examples of jobs in the Techpilot marketplace
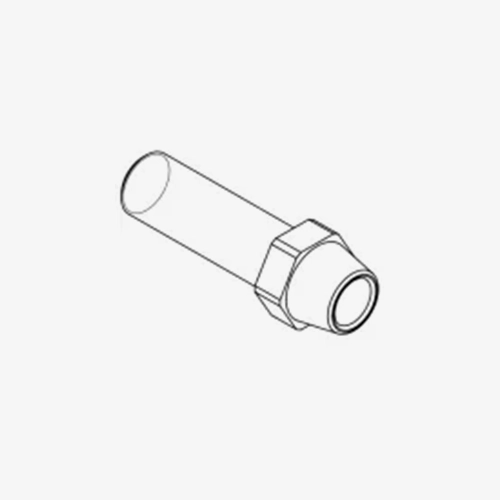
CNC turning clamping screw
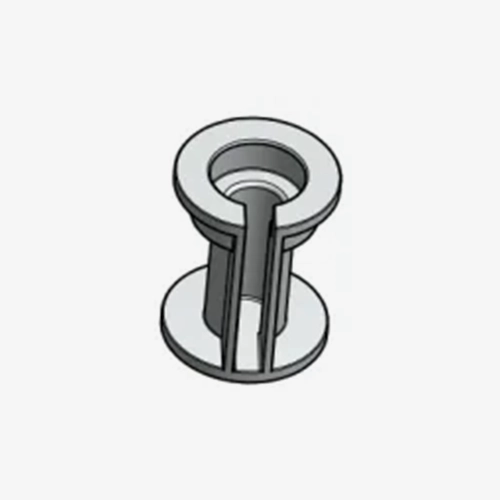
Plastic injection molding
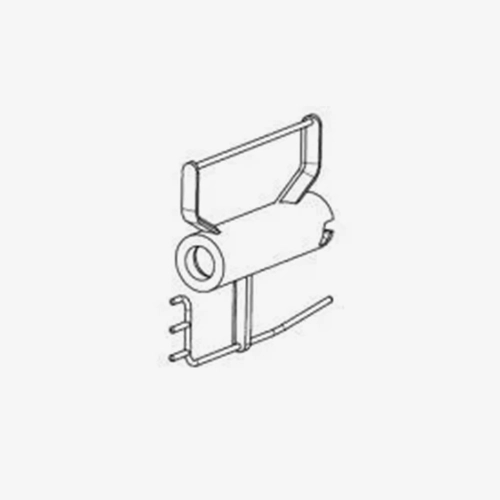
Rotary milling part with laser welding
More about manufacturing processes
Techpilot is Europe’s largest platform for the manufacturing industry.
For over 25 years, we’ve been connecting buyers, suppliers, and manufacturers that are the perfect match – enabling accurate price discovery for custom-made parts. Covering the full spectrum of mechanical components and supporting more than 280 manufacturing technologies, Techpilot is the market leader in Europe.Buyers gain instant access to qualified suppliers, full market transparency, and increased efficiency in their e-sourcing processes.
Suppliers benefit from high online visibility, extended media reach, and a profitable digital sales channel through Techpilot.
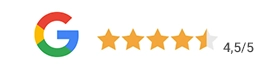
Lexicon Themes
- Metalworking (31)
- Plastic processing (8)
- Parts (8)
- Surface treatment (8)
- Welding (7)
- Machining (6)
- Sheet metal processing (6)
- Cutting (6)
- Turning (5)
- Manufacturing (5)
- Milling (4)
- Tool making (4)
- Suppliers (4)
- Casting (4)
- Procurement (4)
- Contract manufacturing (3)
- Profiles (3)
- Automation technology (2)
- Gearing & Thread (1)
- Forging (1)
- Wire processing (1)
- Heat treatment (1)