Friction stir welding
The friction welding (see: Friction Stir Welding) belongs to the group of friction welding processes and is particularly suitable for joining non-ferrous metals with low melting temperature and mixed compounds.
The method is based on the use of a rotating pin which is guided between the contact surfaces of two workpieces. The friction heat produced thereby ensures a plasticization of the material and allows welding of the workpieces. Stir friction welding produces particularly high-quality welded joints with excellent fatigue properties and is therefore very popular in the metal processing industry.
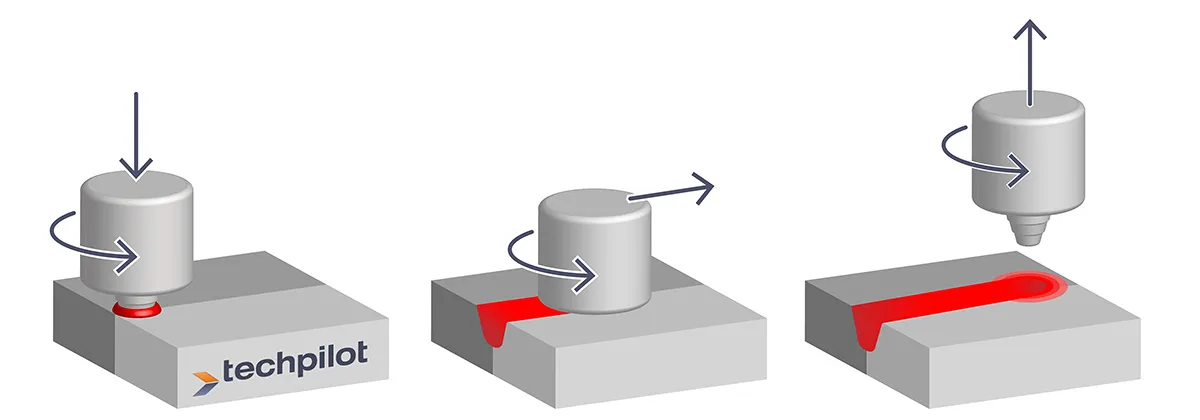
Technical foundations for agitating friction welding
The stirring friction welding is described in the standard EN ISO 4063 (process 43) and can be described in a simplified manner in six successive steps:
- The components to be welded are clamped in a device, subjected to pressure and pressed against one another. The rotating pin-like tool is pressed with high force into the gap between the components until the shoulder of the tool rests on the surface of the component.
- The rotational movement of the tool produces friction energy which heats the material in the joining gap at the immersion point. In the course of this heating, the material plasticizes, as a result of which the two materials are mixed together and joined together in the joining gap.
- The tool now moves along the joining gap with a further rotating movement, the high contact pressure being maintained. This process transports the already plasticized material around the tool, mixes there and forms a weld seam.
- When the rotating pin reaches the end of the provided welding seam, the feed movement is stopped.
- The tool is now removed from the joining zone of the two components, when the movement continues to rotate.
- In the course of the final quality check, the weld is examined by visual assessment or by non-destructive testing methods.
Which materials can be welded?
Stir friction welding is ideal for joining sheets with a depth of more than 30 mm. One of the challenges of the method is the high process force which arises due to the high contact pressure with simultaneous rotational movement. Since the attainable welding depths decrease with increasing strength, the agitating friction welding is predestined above all for joining aluminum components. In addition, however, mixed compounds of aluminum and steel and metal foams are also welded to the process.
Hardly weldable or other materials can also be provided. These include:
- Magnesium
- Copper
- Titanium
Spare parts of Rapid Technic AG:
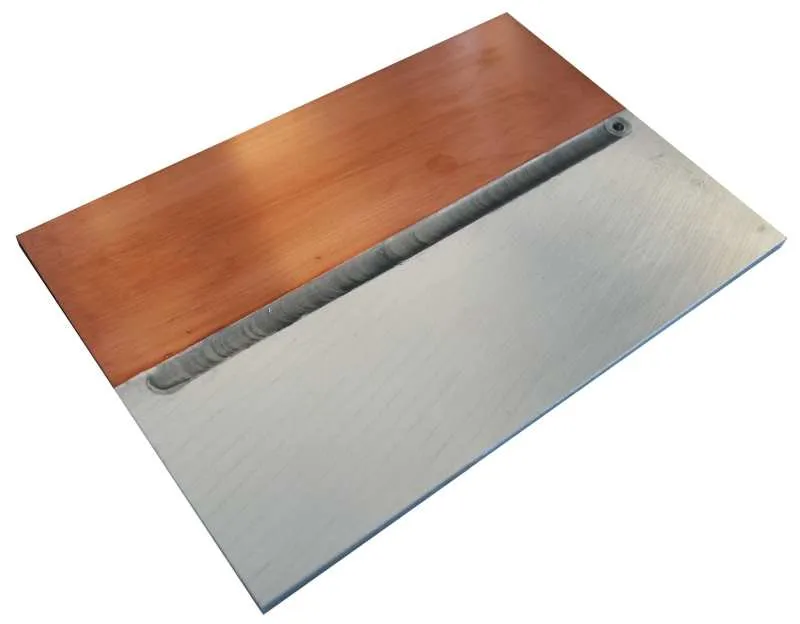
Aluminium and copper plate
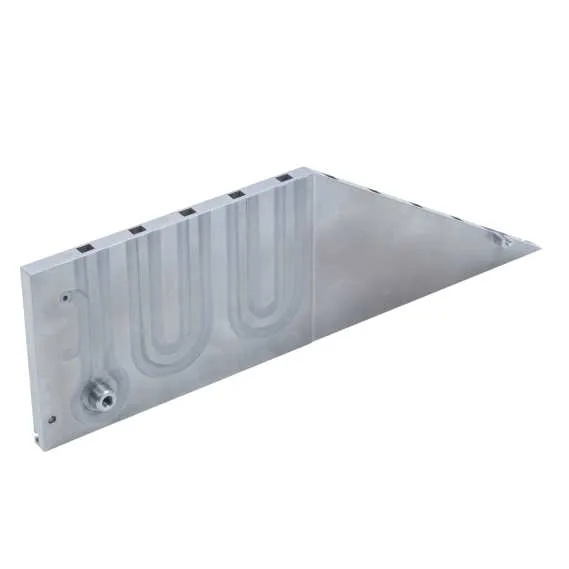
Aluminum Plate - Stirring Welding
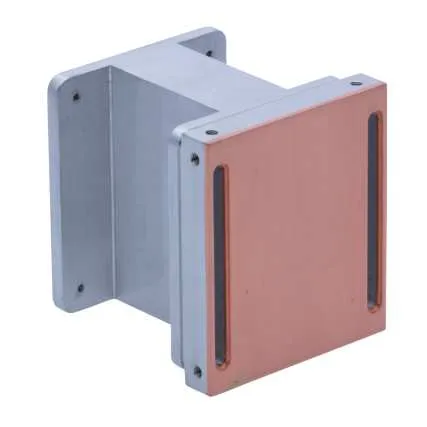
Aluminium copper connection - Stirring friction welding
Advantages of agitating friction welding
Compared to other welding processes, the stirring friction welding is distinguished by a number of decisive advantages. The main advantages of the process are:
- Quality: Due to the comparatively low introduction of heat, no cracks or pores are produced in the material during stirring friction welding. The resulting weld is distinguished by a high strength with minimal distortion.
- Economics: When using state-of-the-art machines, the agitator welding allows the economical joining of components with complex 3D geometries. Since no consumables such as protective gas or filling wire are required, the consumption costs are correspondingly low.
- Environment: In contrast to conventional welding processes, no flue gases or dangerous flashes of light occur during stirring friction welding. Furthermore, the environmental balance of the process is very friendly thanks to the low energy consumption.
In what areas do we use agitating friction welding?
Stir friction welding is used in various industries for joining aluminum and other materials. Customers for guided friction-welded components come mainly from the following areas:
- Automotive industry
- Aerospace Technology
- Railway technology
- Transport and transport
- Marine applications (e.g. shipbuilding)
- Production of heat exchangers
- Nuclear technology
- Medical technology
- Container construction
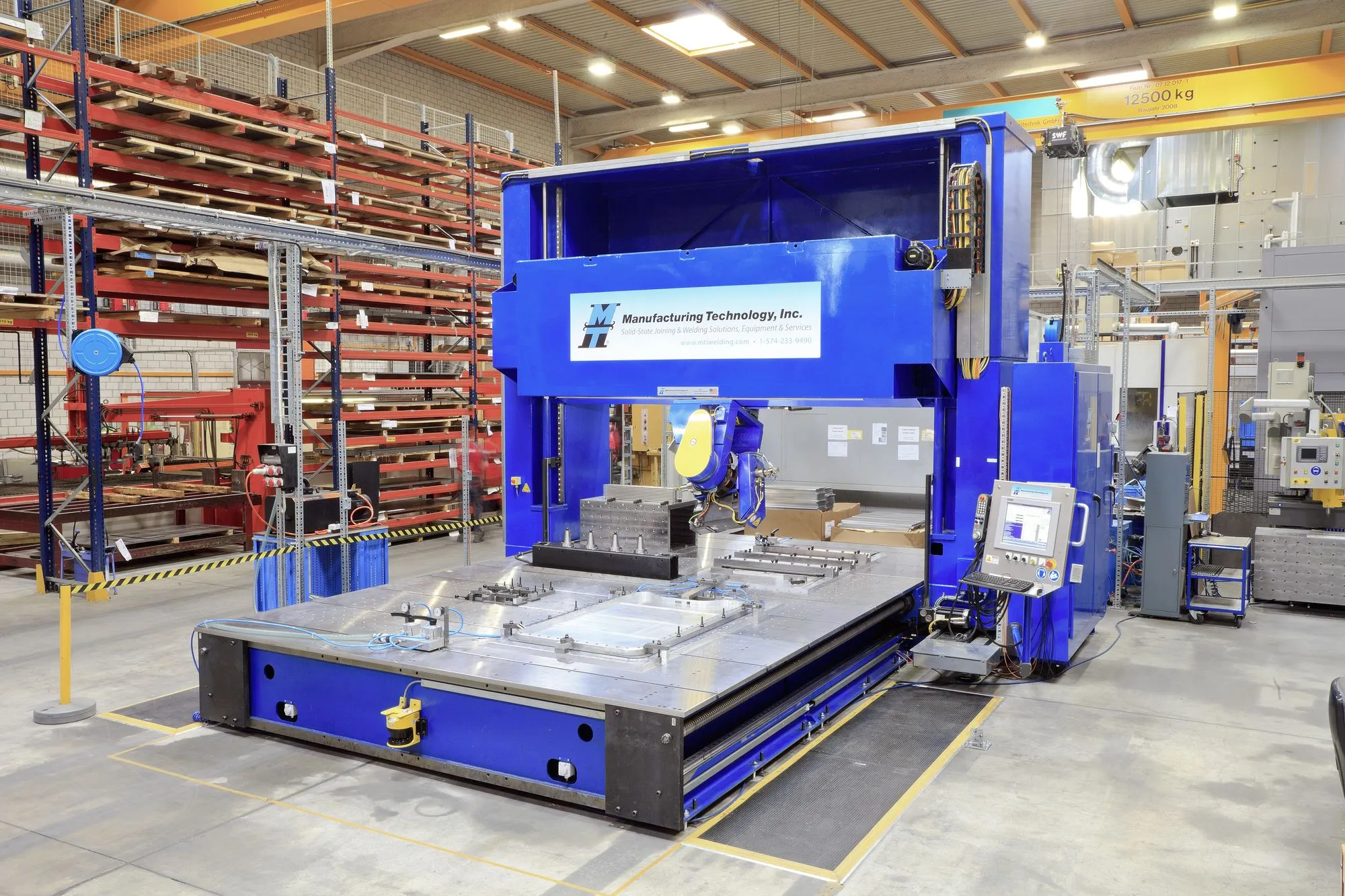
MTI stirrer welding machine at Rapid Technic AG
Find companies for agitator welding
If you are looking for a Friction Stir Welding, you will find a large number of contractors that meet your requirements at Techpilot. Techpilot offers the largest supplier pool for drawing parts in Europe and has registered over 24,000 suppliers.
As a buyer, use the platform for free. You have access to the extensive search function and can upload specific requests for your drawing parts requirement. The incoming offers from interested contract manufacturing companies compare you practically and easily with price, quality and delivery time. The tool will help you quickly find suitable suppliers.
At any time, you will be supported by Techpilot's service team by phone. The trained employees know very well in the industry and can provide you with numerous help, especially when creating your inquiries.
More on Stirring Welding
Techpilot is Europe’s largest platform for the manufacturing industry.
For over 25 years, we’ve been connecting buyers, suppliers, and manufacturers that are the perfect match – enabling accurate price discovery for custom-made parts. Covering the full spectrum of mechanical components and supporting more than 280 manufacturing technologies, Techpilot is the market leader in Europe.Buyers gain instant access to qualified suppliers, full market transparency, and increased efficiency in their e-sourcing processes.
Suppliers benefit from high online visibility, extended media reach, and a profitable digital sales channel through Techpilot.
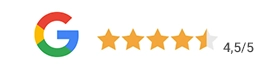
Lexicon Themes
- Metalworking (31)
- Plastic processing (8)
- Parts (8)
- Surface treatment (8)
- Welding (7)
- Machining (6)
- Sheet metal processing (6)
- Cutting (6)
- Turning (5)
- Manufacturing (5)
- Milling (4)
- Tool making (4)
- Suppliers (4)
- Casting (4)
- Procurement (4)
- Contract manufacturing (3)
- Profiles (3)
- Automation technology (2)
- Gearing & Thread (1)
- Forging (1)
- Wire processing (1)
- Heat treatment (1)