Spot welding
The spot welding is also referred to as resistance spot welding and is one of the welding methods without using protective gas. The method is based on the punctual heating and liquefaction of two workpieces pressed on one another by applying a strong voltage.
Compared to other welding processes, spot welding is characterized by good productivity, a high degree of automation and a low material distortion. For this reason, the joining method is used primarily in bodywork and vehicle construction, in sheet metal processing and in the electrical industry.
Technical basics for spot welding
The technical process of spot welding is relatively simple and can be simplified with four process steps:
- Setting of workpieces: In the first step, it is necessary to precisely align the two workpieces to be connected to one another with respect to one another. It is crucial to achieve high accuracy. Correction of errors is possible only at high expense after permanent welding.
- Mounting and pressing of electrodes: In the welding process, the electrodes are responsible for conducting the electrical current through the workpieces to be connected. For this reason, they must withstand high electrical and thermal loads and are preferably made of tungsten or molybdenum. The electrodes are pressed from both sides with pressure onto the welding points and hold the workpieces together.
- heating and liquefaction: After the alignment of the workpieces and the attachment of the electrodes, electrical welding current is conducted from electrode to electrode through the workpiece. The electrical resistance of the workpieces ensures that the electrical energy is converted into thermal energy and a strong heating up to liquefaction occurs locally. In the contact zone, the two workpieces are permanently joined together by this process.
- Removing electrodes: After both parts are firmly connected to one another, the electrodes are removed and pressed back at the next point. The duration of the current supply or the welding time depends on various factors and varies from case to case.
The process steps described here can be repeated as often as necessary, depending on the size of the workpiece.
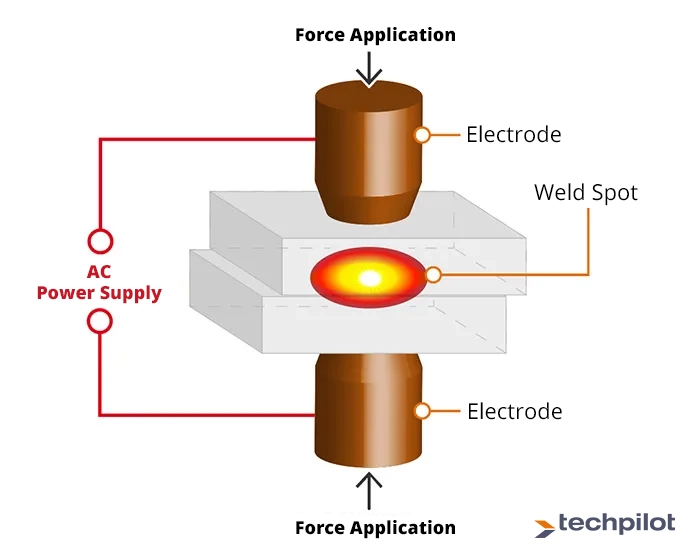
Point welding operation
The spot welding is now applied both manually and automatically. While automotive workshops or craftsmen work mainly with mobile resistance welding devices, welding robots with a high degree of automation are also used in series production. In mobile resistance welding devices, welding tongs are usually used.
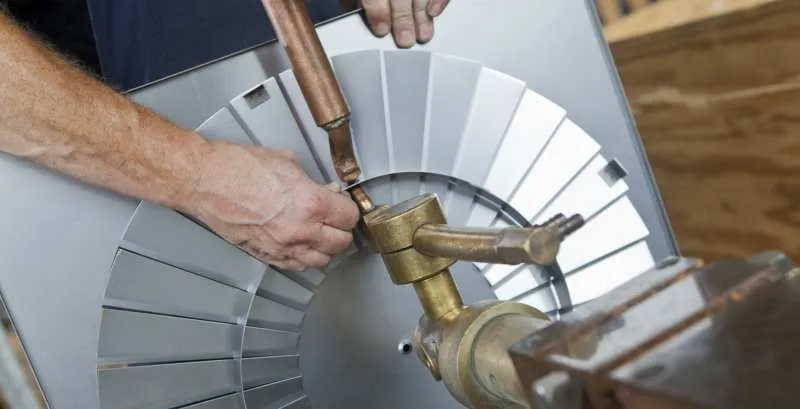
Manual spot welding at Wilvo metaalbewerking b.v.
What materials is the spot welding suitable?
During spot welding, various chemical interactions occur between the atoms of the two workpieces due to the strong punctual heating. This results in different types of connection: In addition to joining in the molten state, there is also a diffusion compound and a compound in solid phase.
Since the above-mentioned bonding properties depend to a great extent on the materials to be joined, not all materials can be welded equally well. While materials with high thermal and electrical conductivity are not suitable, for example, due to the rapidly flowing heat, brittle and hard materials tend to form fractures during the cooling process.
In principle, however, spot welding is suitable for a whole range of materials, provided the welding parameters are taken into account. These include:
- Aluminium
- brass
- Copper
- Gold
- Silver
- Bronze
- Nickel
- Titanium
- Platinum
- Chrome
- Iron
Molybdenum
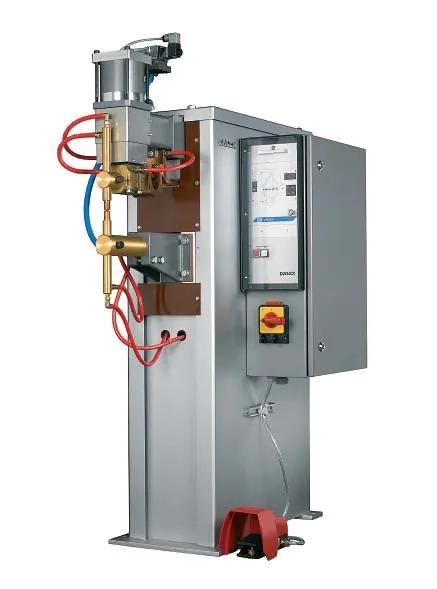
Point welding device from STAMM Blechtechnik GmbH & Co. KG
What is the spot welding used for?
The spot welding is very popular due to the fast cycle times and the high cost-effectiveness, especially when permanently connecting sheets. Thus, sheets and profiles with a sheet thickness of up to 3 mm can be joined together without restriction by spot welding. Both the intensity of the current flow and the welding time depend entirely on the thickness of the sheets to be connected.
The fields of application for spot welding range from pure sheet metal processing to joining steel sheets in bodywork and vehicle construction to repair and maintenance work in crafts. In the electronics industry, the method is used, for example, for the production of capacitors or relay contact sets.
What are the advantages of the process?
- Geringer component distortion due to welding heat
- High energy efficiency
- High efficiency
- More possibilities for automation
- No additional material required
- Suitable for various material combinations
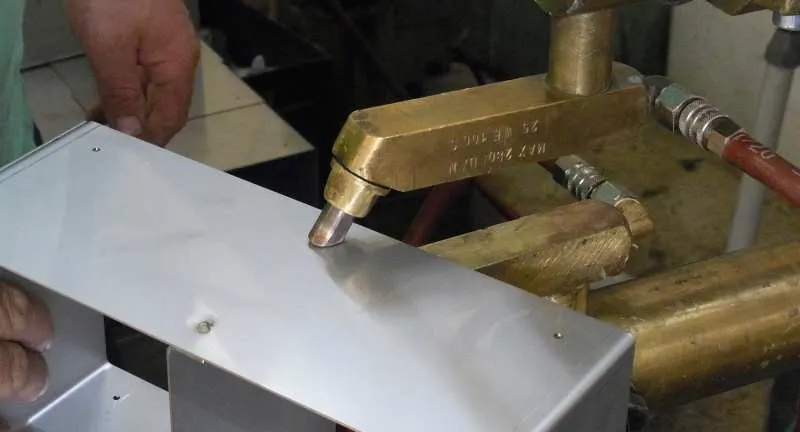
Point welding system from UNIKANTO GmbH
Find companies for spot welding
You are looking for a Spot Welding ? Techpilot, Europe's largest platform for the manufacturing industry, connects technical buyers and suppliers for 280 different technologies. As a buyer you register for free and have access to the extensive supplier pool, which includes among other things numerous companies specializing in spot welding.
Contact companies directly or make requests for your drawing parts publicly to reach as many companies as possible. Incoming offers compare quickly and easily to find a new supplier.
Techpilot will provide you with a technically trained team that will help you with all your activities on the platform. Staff provide both telephone support and help via e-mail. Especially when creating enquiries, you will receive helpful support.
Examples of jobs in the Techpilot marketplace
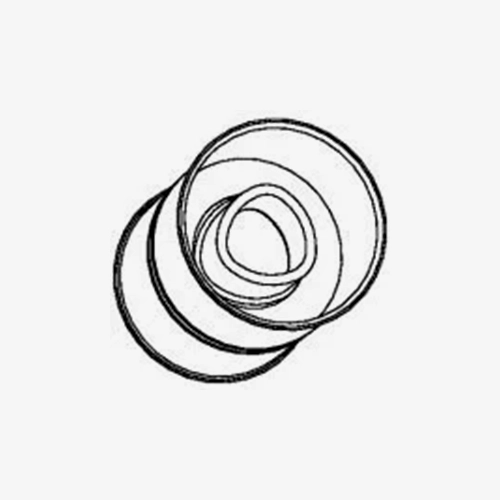
Deep drawing and spot welding
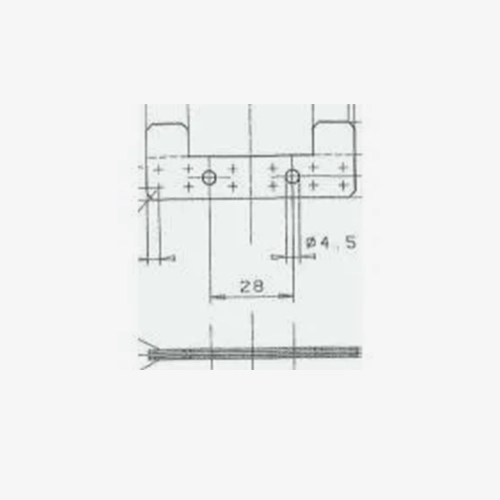
Request for laser cutting and spot welding
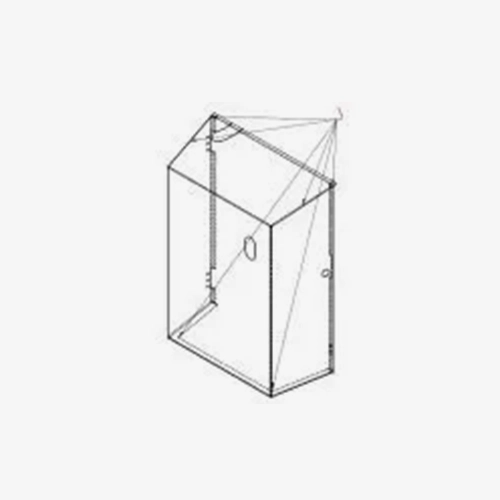
Sheet metal processing and spot welding
More about spot welding
Techpilot is Europe’s largest platform for the manufacturing industry.
For over 25 years, we’ve been connecting buyers, suppliers, and manufacturers that are the perfect match – enabling accurate price discovery for custom-made parts. Covering the full spectrum of mechanical components and supporting more than 280 manufacturing technologies, Techpilot is the market leader in Europe.Buyers gain instant access to qualified suppliers, full market transparency, and increased efficiency in their e-sourcing processes.
Suppliers benefit from high online visibility, extended media reach, and a profitable digital sales channel through Techpilot.
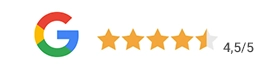
Lexicon Themes
- Metalworking (31)
- Plastic processing (8)
- Parts (8)
- Surface treatment (8)
- Welding (7)
- Machining (6)
- Sheet metal processing (6)
- Cutting (6)
- Turning (5)
- Manufacturing (5)
- Milling (4)
- Tool making (4)
- Suppliers (4)
- Casting (4)
- Procurement (4)
- Contract manufacturing (3)
- Profiles (3)
- Automation technology (2)
- Gearing & Thread (1)
- Forging (1)
- Wire processing (1)
- Heat treatment (1)