TIG welding
The tungsten inert gas welding (IG welding) belongs to the group of melt welding processes and is characterized by particularly clean processing, high seam qualities and almost universal applicability in the metal sector.
Due to the particularly precise tuning of the welding current to the respective welding task, the welding method is particularly suitable for root positions and forced positions. For this reason, WIG welding enjoys great popularity in tasks with high standards of precision and seam quality, such as pipeline and apparatus construction, power plant construction and chemical industry.
Technical basics for WIG welding
The WIG welding method is based on the generation of an electric arc between the workpiece and an electrode consisting of tungsten. In addition, an inert gas such as argon or helium is used to protect the arc from external influences.
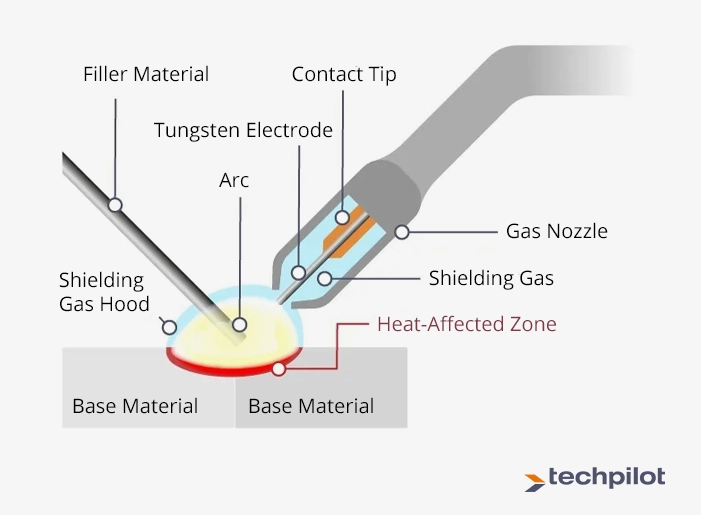
WIG welding operation
Compared to other welding methods such as the MIG or MAG welding, the WIG welding is distinguished above all by the fact that the tungsten electrode used does not melt, but is retained during welding. Instead, a welding additive is used as required to produce a seam between the workpieces to be connected. This additional material is usually a welding wire which is held at the contact point of the two workpieces and melts there.
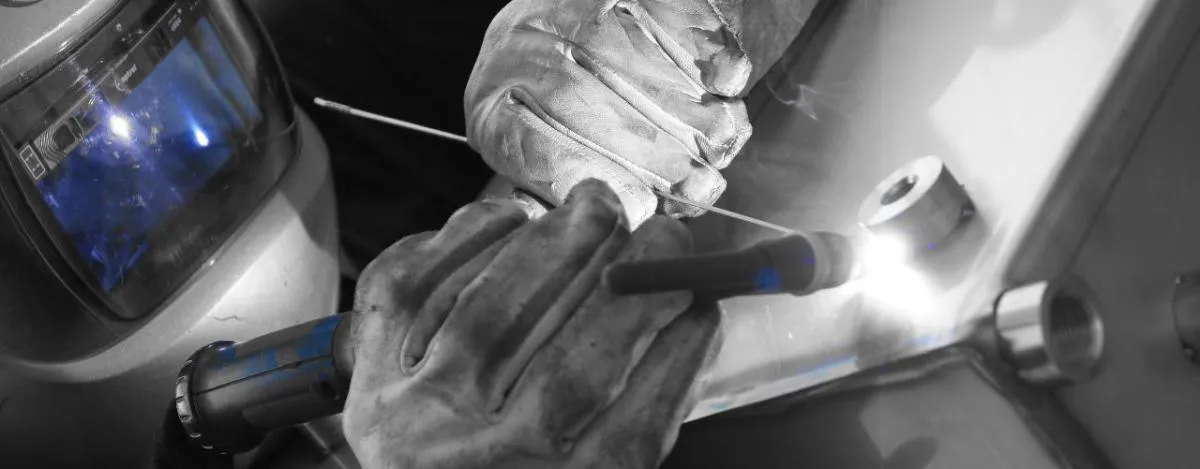
WIG welding at Heinz Röhrich Metall und Weldingtechnik GmbH
The construction of a WIG welding system
A WIG welding system consists essentially of a gas supply, a power source, a hose package, the burner and the minus pole. The power source is responsible for generating the voltage required for the ignition of the arc. If the short-circuit-based contact ignition was frequently used earlier, the high-frequency ignition has prevailed today. A high-voltage pulse generator is used to generate the high required voltage and to ionize the gas between the electrode and the workpiece. This procedure achieves a safer and efficient ignition process.
The hose package is not only responsible for the conduction of the welding current, but also includes the guidance of the protective gas and the control line. In the case of larger burners, it is also necessary to provide a cooling system for discharging the resulting process heat. In this case, the hose package also contains the supply and return of the cooling water.
Applications for WIG welding
The WIG welding is mainly used in applications where the requirements for the quality and optics of the weld are very high. These include, inter alia, the following fields of application:
- Pipe and apparatus construction
- Power plant construction
- Chemical industry
- Medical technology
- Bicycle frame construction
- Aerospace Technology
- Land construction
- Steel construction
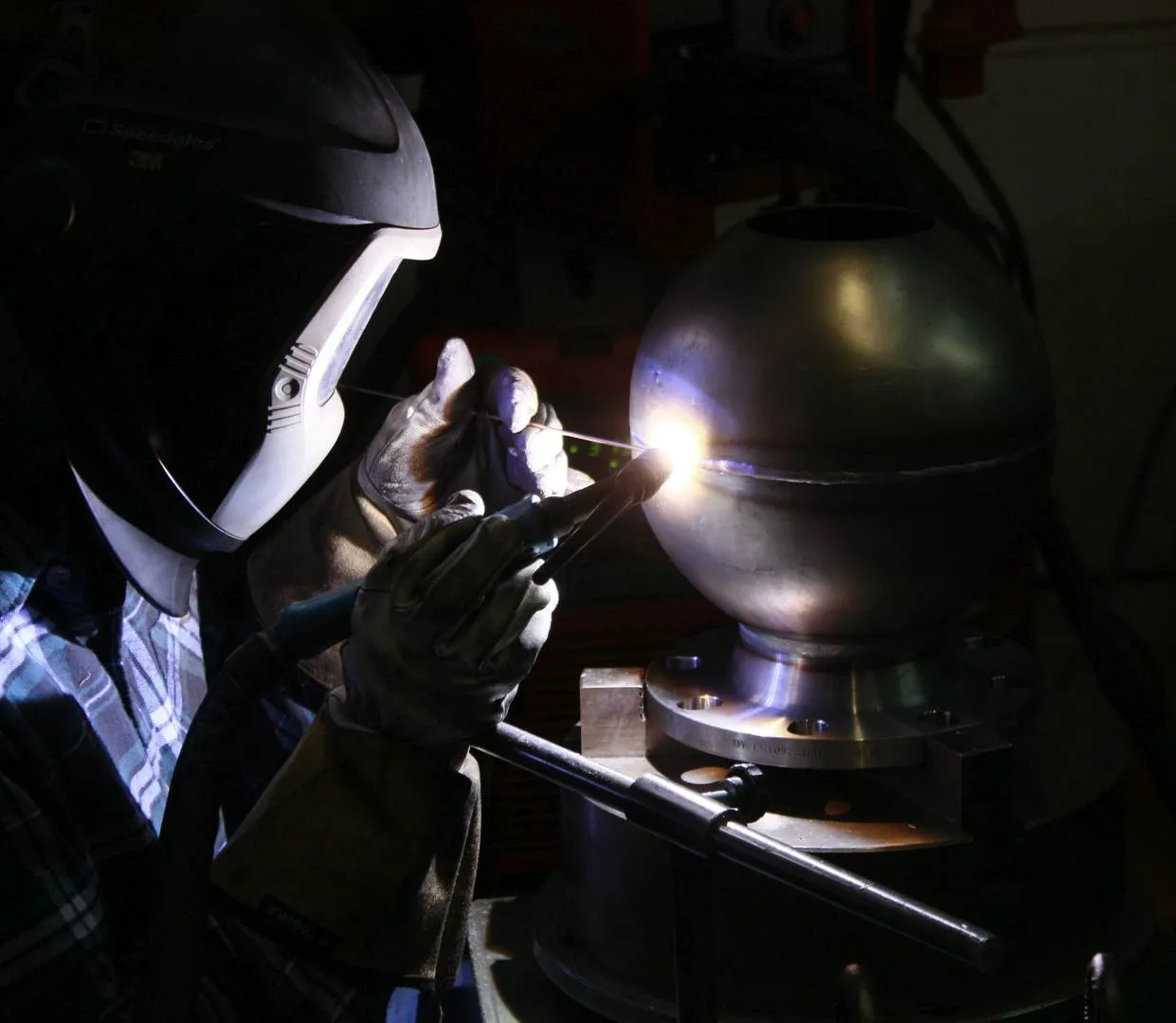
WIG welding at S.M.B.-Schweisstechnik GmbH
Which protective gas is used?
In WIG welding technology, the protective gas is responsible for protecting and stabilizing the electric arc from the influences of oxygen. The gas thus represents an important basis for the quality of the welds.
The selection of the protective gas is important that it is an inert gas. The inert gases do not undergo any chemical reactions with the materials involved and are therefore ideally suited for use in welding processes.
Due to the cost-effective procurement, the noble gas argon enjoys great popularity during WIG welding. Helium or a mixture of helium and argon is also used in applications with a high desired introduction of heat. If particularly high speeds are desired during welding, hydrogen can also be added in small amounts.
When supplying protective gas, it is important to determine a suitable flow rate. The flow rate depends not only on the material, but also on the desired seam shape of the welding, the welding position and the diameter of the gas nozzle.
Advantages
- Suitable for all weldable metals
- Precise addition of welding wire:
Thanks to non-melting tungsten electrode - No slag formation:
Thanks to inert gas - Hard material deformation
- Suitable for all welding positions
Disadvantages
- High wind sensitivity:
Therefore not suitable for outdoor areas - High energy requirement
- High initial investment
Find companies for WIG welding
WIG welding specialized companies can be found quickly and easily via Techpilot. Europe's largest platform for the manufacturing industry offers buyers and suppliers the opportunity to network and engage in new business relationships. Buyers use the extensive industry book with over 24,000 registered suppliers for free. Various filter functions allow the specific search based on the location, manufacturing technology, size of the part, material and many other criteria. This allows buyers to quickly and easily find exactly matching businesses for their parts. The selected companies can be sent directly online inquiries with drawing. If you want to broaden your request, you can write it out on the platform and receive offers from different companies. The practical offer comparison provides an overview of all points at a glance and thus facilitates the selection of a suitable supplier.
Examples of jobs in the Techpilot marketplace
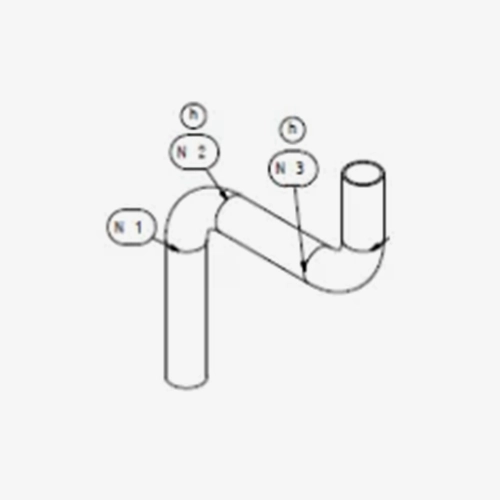
WIG welding holder
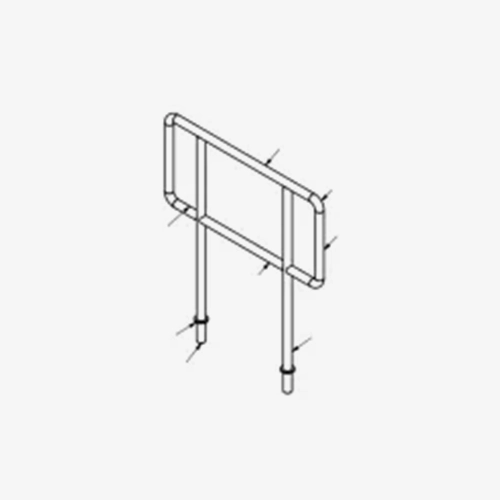
WIG-Schweissen Aluminium-Geländer
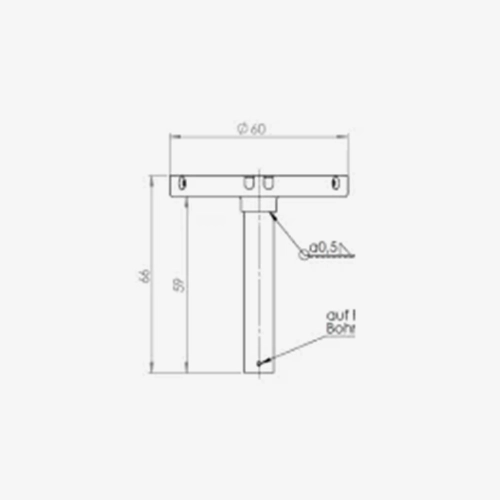
Turning and WIG welding
More about WIG welding
Find companies for
- Inert Gas Shielded Arc Welding Mig Mag
- Friction Stir Welding
- Welding
- Flash Butt Welding
- Electron Beam Welding
- Robot Welding
- Spot Welding
- Projection Welding
- Manual Electrode Welding
- Stud Welding
- Welded Constructions Weldments
- Inert Gas Shielded Arc Welding Tig
- Inert Gas Shielded Arc Welding Plasma
- Submerged Arc Welding
- Friction Welding
- Laser Beam Welding
Techpilot is Europe’s largest platform for the manufacturing industry.
For over 25 years, we’ve been connecting buyers, suppliers, and manufacturers that are the perfect match – enabling accurate price discovery for custom-made parts. Covering the full spectrum of mechanical components and supporting more than 280 manufacturing technologies, Techpilot is the market leader in Europe.Buyers gain instant access to qualified suppliers, full market transparency, and increased efficiency in their e-sourcing processes.
Suppliers benefit from high online visibility, extended media reach, and a profitable digital sales channel through Techpilot.
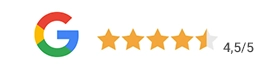
Lexicon Themes
- Metalworking (31)
- Plastic processing (8)
- Parts (8)
- Surface treatment (8)
- Welding (7)
- Machining (6)
- Sheet metal processing (6)
- Cutting (6)
- Turning (5)
- Manufacturing (5)
- Milling (4)
- Tool making (4)
- Suppliers (4)
- Casting (4)
- Procurement (4)
- Contract manufacturing (3)
- Profiles (3)
- Automation technology (2)
- Gearing & Thread (1)
- Forging (1)
- Wire processing (1)
- Heat treatment (1)