Injection molding tool
The injection molding tool is a continuous mold used to produce components with an injection molding machine. The injection molding tool usually consists of metal and has a cavity which determines the shape and surface structure of the produced part.
During injection molding, the injection molding tool is filled with plasticized plastic under pressure. Subsequently, the material cools down in the injection molding tool and thereby hardens. After the tool has been opened, the molded part can be removed. Injection molding tools are used to produce various components with weights of a few tenths of grams up to 150 kg. The process enables economical and efficient series production and therefore enjoys great popularity in the plastics processing industry.
The construction of an injection molding tool
Injection moulds generally have a two-part structure: One tool half is referred to as the nozzle side and the other as the ejector side. Both halves of the mold again consist of several plates which fulfill different functions. The components of an injection molding tool at a glance:
Nozzle side
- clamping plate
- Form plate
- Cooling system
- cavities
- Casting bush
- centering ring
- Guide elements
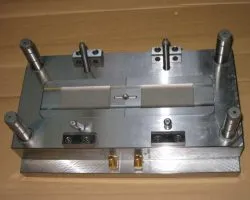
Nozzle side of an injection moulding tool from the company Washingke Formenbau - Kunststofftechnik GmbH
Ejection site
- clamping plate
- Form plate
- ejector bolt
- ejector plates
- Support bars
- Intermediate plate
- cavities
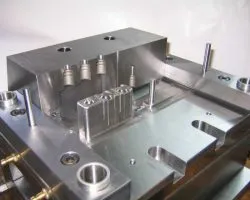
Ejector side of an injection moulding tool from Waske Formenbau - Kunststofftechnik GmbH
The nozzle side refers to the stationary side of the mold in the injection molding process. This side contains the cavity halves, also known as mold inserts, as well as the components of the gating system. Usually, a cooling distribution system is also located on the nozzle side to optimize heat dissipation after the melt is injected.
Injection molds are equipped with an interchangeable centering ring and are mounted on the clamping plate. The centering ring allows precise alignment of the nozzle during insertion, guiding it to the sprue bushing. For molds operating at high temperatures, an insulating plate is typically installed in front of the clamping plate to prevent excessive heat transfer.
The ejector side of the tool is characterized in that the ejector elements are positioned here. After cooling, hardening of the injection molding compound and opening the tool halves, the component is first located in the ejector side. With the aid of the ejector device, the finished part is freed from the mold in order then to be able to be reprocessed at the end and tested in quality assurance.
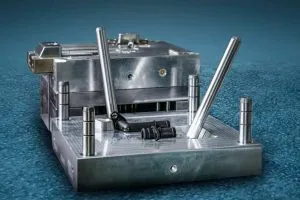
Injection moulding tool for cooling water connections from gloss matrix GmbH
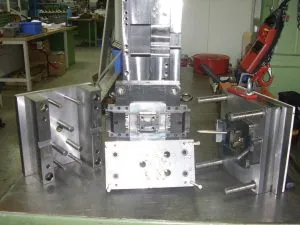
Injection moulding tool from Manufacturing Technology EU
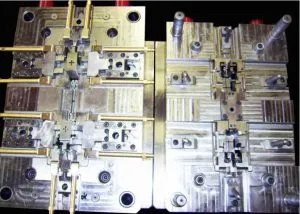
2-time injection moulding tool from U. Eitner Formenbau, Erodier- & Kunststofftechnik GmbH
The process for injection molding tool in mold construction
The development of an injection molding tool comprises a number of different working steps. Not only is the tool tuned to the later used plastic, but also the later injection process is optimized in the context of FEM calculations and simulations. Overview of the working steps from the first sketch to the finished injection molded part:
- Configuring a basic sketch
- Determination of tool technology
- Dimensioning and technical design of the tool
- Detuning the tool to the plastic material
- Development of the potting system
- Construction of tool elements
- Simulation of filling process
- Finite Element Analysis (FEM)
- Mechanical manufacturing
What material are injection molding tools made of?
Injection molding tools for the plastics processing industry are usually made of steel as permanent molds. Depending on the number of planned injection processes, more wear-resistant materials such as hardened or tempered tool steel or hard metals can be used.
In steel mold construction, a distinction is made between the standard shapes, jaw shapes and change molds. While standard shapes are suitable for very versatile applications, jaw shapes are equipped with a slide and are particularly suitable for components with large undercuts. Alternating shapes are, on the other hand, predestined for prototypes and small series, since the shape structure remains on the machine, while only the alternating inserts on the nozzle and ejector side are exchanged.
3D printing as an alternative to conventional tool
In the case of small quantities in which the development and production of a steel mold is not economical, 3D-printed molds are suitable. 3D-printed injection moulding materials are produced according to a drawing by a 3D printer and usually consist of particularly powerful plastics. In the development of 3D injection molding tools, care must be taken to select a high-performance plastic which is suitable for the later use and in particular the pressure and temperature levels during injection molding.
Find companies for injection moulding
Injection Moulds and Injection Moulds can be found in the simplest way through Techpilot, Europe's largest platform for drawing parts in Europe. With more than 24,000 registered suppliers, the database offers an extensive supplier search and enables new valuable contacts to be established.
All Techpilot functionalities are free of charge for purchasers. This includes creating online requests for your parts. Thanks to the integrated offer comparison, you can quickly and easily balance the incoming offers of the interested companies with respect to each other and find the right payroll for your company.
Techpilot staff will help you to use the platform at any time and help you create online requests. The broad industrial expertise of the team is particularly helpful.
Examples of jobs in the Techpilot marketplace
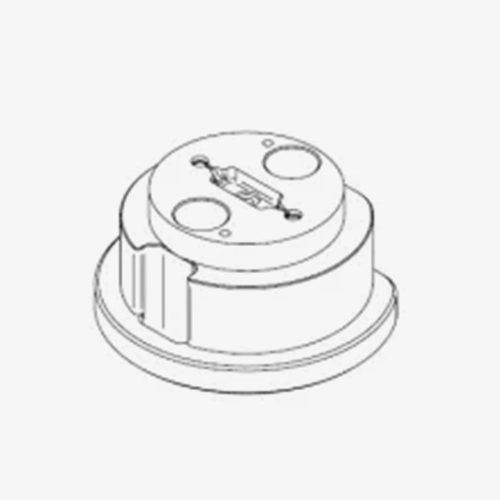
Order for mould inserts
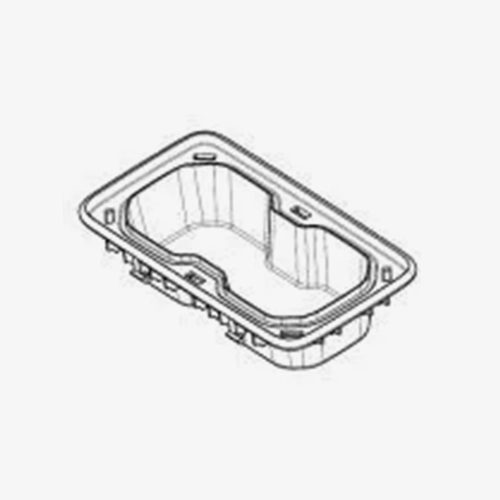
Application for plastic injection molding tool
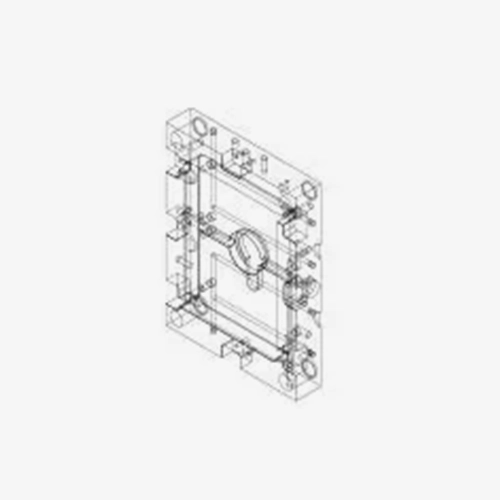
Application for form frames
More about injection molding tool
Techpilot is Europe’s largest platform for the manufacturing industry.
For over 25 years, we’ve been connecting buyers, suppliers, and manufacturers that are the perfect match – enabling accurate price discovery for custom-made parts. Covering the full spectrum of mechanical components and supporting more than 280 manufacturing technologies, Techpilot is the market leader in Europe.Buyers gain instant access to qualified suppliers, full market transparency, and increased efficiency in their e-sourcing processes.
Suppliers benefit from high online visibility, extended media reach, and a profitable digital sales channel through Techpilot.
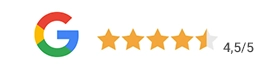
Lexicon Themes
- Metalworking (31)
- Plastic processing (8)
- Parts (8)
- Surface treatment (8)
- Welding (7)
- Machining (6)
- Sheet metal processing (6)
- Cutting (6)
- Turning (5)
- Manufacturing (5)
- Milling (4)
- Tool making (4)
- Suppliers (4)
- Casting (4)
- Procurement (4)
- Contract manufacturing (3)
- Profiles (3)
- Automation technology (2)
- Gearing & Thread (1)
- Forging (1)
- Wire processing (1)
- Heat treatment (1)