Tool making
In the case of tool construction, high-precision tools are produced which serve to produce workpieces in mass production. The tools must be made of a suitable material and produced in the highest quality.
Most manufacturers of such tools work in the machine park with modern CNC machine tools, by means of which precise and detailed contours can be realized. In this case, the production technology is frequently chosen to mill in order to machine a workpiece from which the finished tool emerges.
Similar to injection molding, the first production of the tool is very costly and time-consuming. The investment in the tool is therefore only worthwhile from a certain number of pieces. Tool technology is widely used, since there are hardly any limits in terms of geometry, complexity, size and weight of the tool. Special drilling tools or special carbide drilling tools are used, for example, for the application-specific production of drills for the production of special holes. Tools such as mould milling cutters, secondary composite tools or fine stamping tools each fulfill a specific purpose, but all serve to produce workpieces as inexpensive as possible while maintaining high quality requirements.
Typical customer industries for tool construction are primarily the automotive industry, mechanical engineering, electrical engineering, medical technology, apparatus engineering and measuring technology.
Stamping tools
Stamping tools consist essentially of a die and a die. The punch has the geometry of the desired inner shape and can be attached either to the upper or lower side of the tool. On the other hand, the die has an opening matching the desired contour. During punching, the punch represents the cutting tool, which is guided with high force on stamping plates and cuts them through. Punching tools are often used as secondary composite tools in complex punching systems.
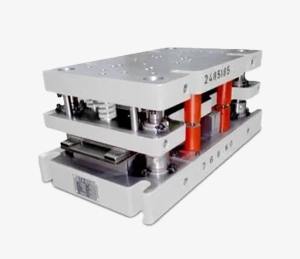
Punching tool by LITTEC
Following composite tool
A Following composite tool is produced in the tool construction and serves the Blech machining . It usually consists of a plurality of stations on which a processing step or an operation on the component is carried out in each case. A carrier strip transports the part to be processed from station to station. After the passage through the secondary composite has ended, the finished punching or sheet metal parts are cut off.
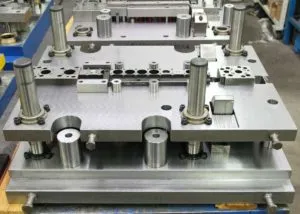
Progressive composite tool from Metalid d.o.o
Form milling cutter
Form milling cutters enable the production of any workpiece geometries whose contour is not restricted by the complexity. The surface profile to be produced is produced by means of the milling tools by performing a spatial or flat feed movement and is accordingly independent of the tool contour.
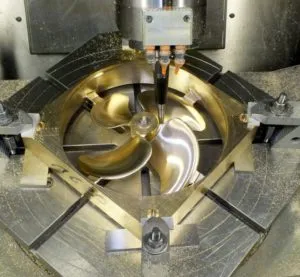
Milled ship propeller from Power Cut GmbH
Fine stamping tool
Fine punching tools or fine cutting tools enable the production of punching parts with high demands on the precision of the cutting in the punching technique. Fine stamping tools, similar to conventional punching tools, consist essentially of a die and a die. These are clamped into corresponding devices in a punching machine. In order to produce fine cutting parts or punching parts with precise cutting surfaces during the punching process, the sheet metal to be processed is pressed by means of the punch under high pressing force into the die, the negative contour of the die being cut out.
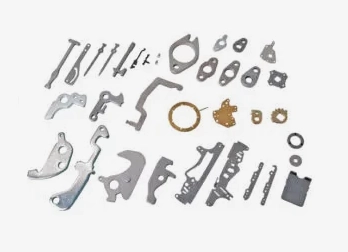
Fine stamping parts of Uebele GmbH Stanztechnik
Fine stamping tools can be used in almost all metallic materials with a sheet thickness of 0.5 to 16 mm. Manufacturers process fine cutting parts or stamping parts with weights between 0.001 and 3 kg. The production of fine cutting tools takes place under the highest demands on precision. In addition, the tool must consist of a harder material than the material to be punched. The fine punching can be well supplemented in the forming technique by secondary composite tools. As a result, the punched assemblies can, for example, undergo further processing as bending parts after the punching process. Modern eccentric presses can achieve a pressing force of several thousand tons in the follow-up joint punching machines.
Extrusion Technology
The extrusion technique essentially serves for the production of extruders for conveying solid to viscous masses.
Extruders are distinguished with respect to the conveying principle in piston and screw extruders. Piston extruders build up the pressure required for conveying the mass by means of a piston, which offers the advantage of a small contact surface with the extrusion mass and a simple cleaning.
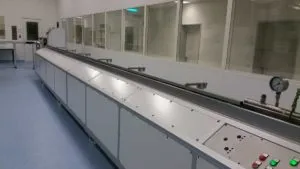
Extrusion - Company SEM-Plastomed GmbH
In extrusion technology, the extruders, extrusion tools and other plant components are designed for the highest thermal and hydraulic requirements. Depending on the process conditions during extrusion, pressures of 10 to 1,500 bar can occur at temperatures of 60 to 300° C. One of the characteristic features of extruders is the length designation indicated as a multiple of the extruder diameter. In extrusion technology, so-called quick-runners achieve speeds of up to 1,500 revolutions per minute.
Sintering tools
Sintering tools serve as a technical basis for the production of sintered parts. The sintering is one of the primordial processes and differs from the casting essentially in that the sintered metal is not melted, but is merely heated and compressed under high pressure.
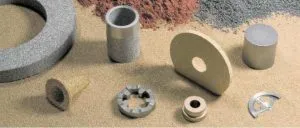
Sintering - Meyer Sintermetall AG
Sinter forming tools must meet high demands for durability and temperature resistance due to the challenging processing temperatures. The shape and design of the fixtures depend primarily on the type of sintering being used.
In sintering, the material to be processed is initially in a fine-grained form. This can include not only sintered metals but also ceramic materials. These are heated under high pressure, causing the volume to shrink. This shrinkage must be taken into account when manufacturing sintering tools in fixture construction.
Depending on the sintering process, the sintering tools have different forms. The so-called dry pressing is particularly suitable in the production of large quantities, in which the water content of the raw material is less than 7%. This method is distinguished above all by good reproducibility and an automated process sequence. On the other hand, a somewhat better compaction of the material results in dampening.
Extrusion tools
Extrusion tools are usually produced in tool construction and are typical industrial requirements in the field of forming technology. The forming tools are constructed technically similar to extrusion tools and pressing tools and enable the production of wires, rods, tubes and profiles of almost any length.
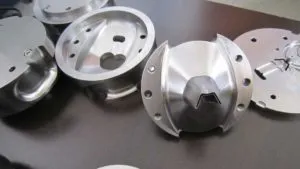
Extruding tools
In the production of extrusion tools, the two key components are the ram and the die. The extrusion die defines the outer shape of the extruded profile and has an opening shaped as the negative of the desired contour. The ram pushes the heated billet through the die, reshaping it in the process.
The extrusion-like process known as profile extrusion allows the production of profiles up to 60 meters long. Materials such as aluminum, aluminum alloys, copper, and stainless steel are used as billets. However, only hot-work tool steels are used to manufacture the extrusion tools, as they must withstand process temperatures of up to 500 °C and the high mechanical stresses that occur during pressing.
After completion by extrusion tools, the produced profiles can be reworked by CNC milling, protected by Breathing or phosphating with a coating or cut by lowering or wire erosion.
Extrusion Tools
Extrusion tools are used in the extrusion process to manufacture hollow or solid bodies from metallic materials. The forming tools are made from durable materials such as hard metal to withstand the high loads of bulk metal forming.
Extrusion tools – similar to cutting tools – generally consist of a punch and a die. The piercing or forming punch presses the raw material through shaping extrusion dies, applying enough pressure for the material to begin flowing. In order for the cross-section-reducing extrusion or reduction dies to shape the material correctly, it must be preheated.
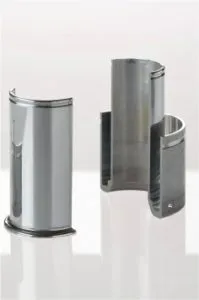
Extruded part - Neuman Aluminium Fliesspresswerk Slovakia s.r.o.
The temperature depends on the material and the desired mechanical properties. If the temperature is below 600 °C, experts refer to this as cold forming. Between 600 °C and 800 °C, it is called semi-hot forming. At higher process temperatures, the term hot forming is used. These temperatures must be considered during the production of forming tools for extrusion.
Extrusion tools are often made from hot-work tool steels that can withstand both the high temperatures and the high pressures of the process. The formed parts produced in this way can be further processed, for example, to improve wear resistance.
Deep-drawing tools
Deep-drawing tools represent the technical basis of the forming production process Deep-drawing and serve for the production of molded parts from sheet metal blanks. Deep-drawing tools normally have the shape of a hollow body open on one side and represent the negative of the geometries of the deep-drawing parts produced.
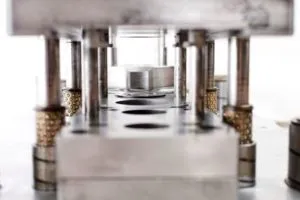
Deep-drawing tool
Punching tools and deep-drawing tools can be combined as follow-up tools for the production of complex punching parts. This approach allows large series of complex deep-drawing parts to be manufactured in a short time. Manufacturing technology can also be combined with other technologies such as the CNC milling.
Vacuum deep drawing tools
Vacuum deep-drawing tools serve to produce precise deep-drawing parts by vacuum deep-drawing. This is also referred to as thermoforming or deep drawing and allows the production of semi-finished products made of plastic.
In this case, a distinction is made essentially between plates and films. Thicker semi-finished products are called plates – thin semi-finished products with a thickness of less than 1.5 mm are referred to as films.
The molding tool is produced in each case as a function of the film thickness and of the selected plastic. The components developed in the tool construction usually consist of metallic materials such as aluminum, the melting temperature of which is far above the melting temperature of the plastics used.
The tools are positioned in the deep-drawing machine in an automatic molding machine and, like foundry models, original models or functional models, have the contour (neg or pos) of the desired semifinished product. In a first step, the film is unwound from rollers and heated in the heating station using heating radiators. The now soft material is fixed in the tool station by a clamping frame and is acted upon by compressed air from one side. From the other side, the material is sucked in pneumatically by vacuum. Thus, the plastic is pressed onto the water-cooled wall of the tool and solidifies there to form a molded part. In the next step, if desired, holes are punched into the plastic parts before the latter is removed.
Special drilling tools
The special drilling tools include solid carbide drills (VHM drills) which, in comparison to conventional drilling, are distinguished in particular by a higher achievable cutting speed, a higher feed rate and an optimized machining.
Drilling tools made of solid carbide or hard metal can have different shapes, and the typical constructions of the special drilling tools include stepped drills, spiral drills, turning plate drills and drills.
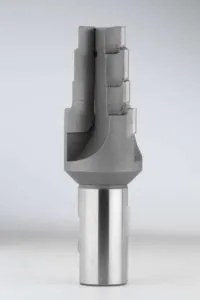
Special drilling tool from GEM Müllerleile GmbH
Step drills are usually made of solid carbide and feature a stepped shape with straight flutes, providing high stability and good hole cylindricity. Step drills can be used in various drilling processes and allow a depth-to-diameter ratio of up to 8.
During drilling, the special drill is clamped into a tool holder which rotates in a spindle in a manner similar to conventional drilling. A high degree of automation with low tool wear can be realized on cutting CNC machine tools. The method can also be combined with a milling cutter.
Embossing tools or Stamp
Embossing tools Stamps are to be assigned to the industrial requirements and are usually manufactured by suppliers in tool making in wage production. An embossing tool or embossing die allows the user to insert engravings into different materials such as paper, metal or leather. In this case, a distinction is made in principle between different types such as the firing punch, the punch, the needle stamp, the brass punch, the blind stamp, the hand stamp and the steel stamp. In the embossing mechanism, these embossing punches are clamped into a type holder and pressed with high force onto the workpiece to be embossed. The so-called patrize represents the counterpart to the die and is responsible for applying the required force.
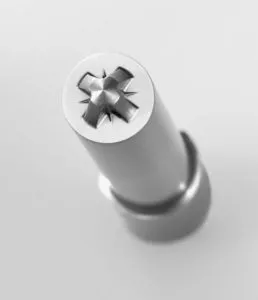
Torx stamp of the company Gebr. Bräm
Embossing tools are typically made of steel or brass and allow the user to engrave character combinations of numbers and letters. Additionally, relief engravings with special characters or logos can also be created. Blind embossing is another common type of industrial engraving.
In embossing shops, embossing tools are primarily used depending on the material to be processed. When embossing paper, special matrices are used to securely imprint patterns or motifs. For example, company logos can be embossed on blank paper in industrial applications.
As a rule, two tools are used for embossing coins which enable the simultaneous processing of both sides of the coin. For this purpose, the coin blank is pushed into the embossing ring by means of a feed tong and is embossed with a contact pressure of up to 200 tons.
Find companies for tooling
If you are looking for Tool Making, you will find a variety of companies specializing in various areas of tool construction. The database of the largest supplier pool for drawing parts comprises over 24,000 suppliers and offers a practical opportunity to find suitable manufacturing companies.
The features of the platform are completely free of charge as a buyer. This includes creating online requests for your parts. You can then send out offers that you can compare in no time with the practical offer comparison of Techpilot in terms of price, quality and delivery time.
You will receive telephone support from our trained service team at any time. Staff have a wide range of expertise in industry and can help you to create inquiries.
Examples of jobs in the Techpilot marketplace
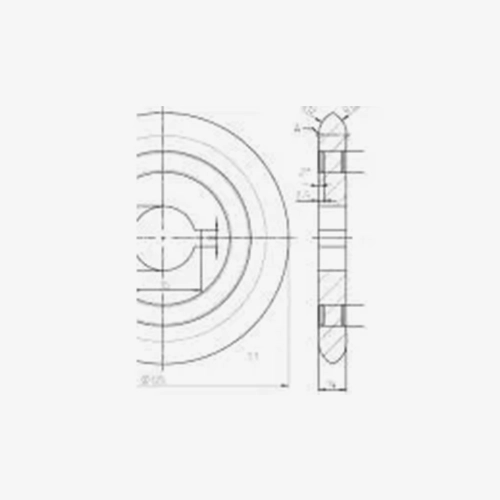
Request for windscreen cutters
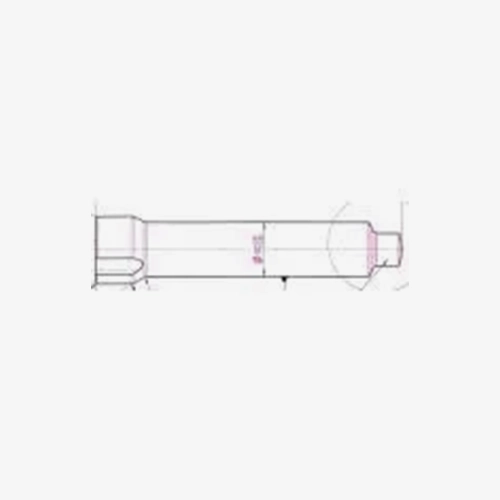
Contact us
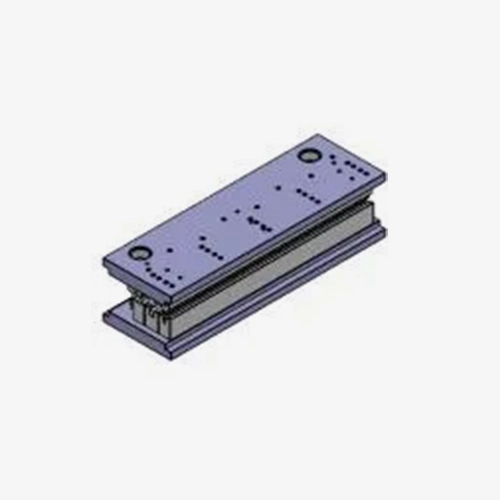
Request Punching tool
More about tool construction
Find manufacturers
Techpilot is Europe’s largest platform for the manufacturing industry.
For over 25 years, we’ve been connecting buyers, suppliers, and manufacturers that are the perfect match – enabling accurate price discovery for custom-made parts. Covering the full spectrum of mechanical components and supporting more than 280 manufacturing technologies, Techpilot is the market leader in Europe.Buyers gain instant access to qualified suppliers, full market transparency, and increased efficiency in their e-sourcing processes.
Suppliers benefit from high online visibility, extended media reach, and a profitable digital sales channel through Techpilot.
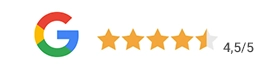
Lexicon Themes
- Metalworking (31)
- Plastic processing (8)
- Parts (8)
- Surface treatment (8)
- Welding (7)
- Machining (6)
- Sheet metal processing (6)
- Cutting (6)
- Turning (5)
- Manufacturing (5)
- Milling (4)
- Tool making (4)
- Suppliers (4)
- Casting (4)
- Procurement (4)
- Contract manufacturing (3)
- Profiles (3)
- Automation technology (2)
- Gearing & Thread (1)
- Forging (1)
- Wire processing (1)
- Heat treatment (1)