Plasma fusion cutting
The plasma cutting is one of the thermal separation methods and allows the user to precisely cut sheets. The widespread method uses the thermal and kinetic energy of a plasma gas stream for liquefying and blowing out the material.
The plasma cutting is used, in particular, when the material cannot be severed or only partially by conventional combustion cutting. The typical areas of application include cutting sheets of high-alloy steel, aluminium or copper. The method is distinguished by high cutting speeds, post-processing cuts, low heat input and low investment costs.
Technical foundations for plasma cutting
Plasma cutting is an energy-intensive process which, in its basics, is comparable to the various variants of arc welding. In addition to a power source with high voltage supply, plasma cutting systems are equipped with a power supply line, a compressed air line, a ground cable, a handpiece and a plasma cutting nozzle. In addition, a cooling medium is usually used for discharging the heat produced.
The electrical energy provided by the current source is first used in the process to generate an energy-poor plasma arc between the cathode and the nozzle. This arc ionizes the gas path between the cathode and the anode and ensures that the arc touches the workpiece and an automatic power increase can take place.
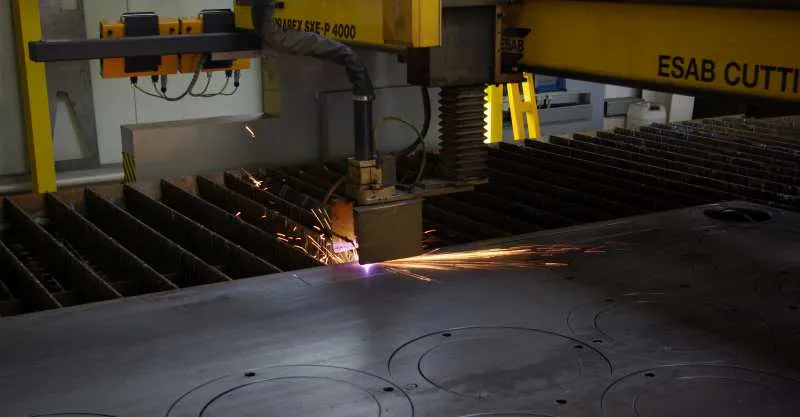
Plasma cutting machine from Ha-Beck Mathias Hasecke e.K.
In the separating manufacturing process, a distinction is made between direct and indirect plasma cutting depending on the type of anode:
- Direct plasma cutting: The arc burns directly between the cathode and the workpiece, which acts as the anode in this case. This method is predominantly used in industry.
- Indirect plasma cutting: The arc does not come into direct contact with the material but burns between the cathode and the nozzle or a sacrificial anode. The advantage of this method is that even electrically non-conductive materials can be processed.
The cutting process is explained in detail below using the example of direct plasma cutting: At the gas- or water-cooled nozzle, the main arc is tightly constricted. This significantly increases the energy density and raises the arc temperature to around 30,000°C with a high exit velocity. Thanks to these process parameters, it is possible to cut sheets of up to 160mm thickness at high speed, depending on the material.
When and where is plasma cutting used?
Plasma cutting is predominantly used in the metal processing industry for processing electrically conductive materials. The method is particularly popular when cutting steel, stainless steel, brass, aluminum and copper. It is used, for example, in the following industries:
- Industrial production
- Processing of thin metal
- Maintenance of factories and agricultural properties
- Car technology
- Restoration
- Industrial construction
- Welding technology
- Mines and scraps
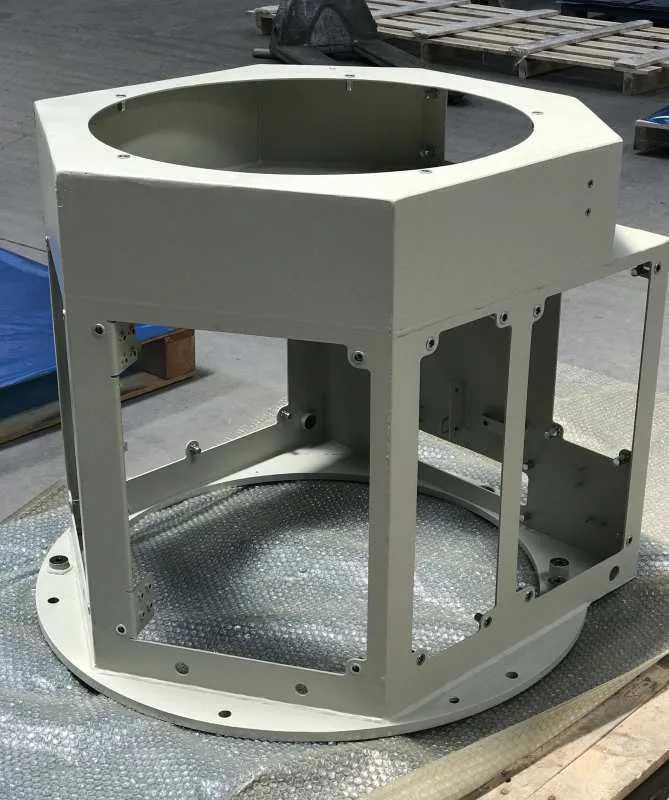
Plasma-cut part of KREA Ltd.
What are the differences to similar procedures?
Plasma cutting is comparable in its basics with similar thermal separation methods as autogen cutting and Laser cutting.
The plasma cutting essentially differs from the autogen cutting or burning cutting by the shape of the material removal. While autogen cutting burns the material by using highly pure oxygen and a special fuel gas, a plasma gas is used for liquefying the material during plasma welding. Plasma cutting achieves a higher accuracy than autogen cutting at material thicknesses below 160mm.
Laser cutting was developed after plasma cutting and is based on the generation of a high-energy laser beam for cutting the material. In contrast to plasma welding, the laser cutting can be applied to all conceivable materials and achieves the material removal by melting, burning or evaporation, depending on the method variant. Although laser cutting achieves a higher accuracy than plasma cutting, it is limited with respect to the cutting thickness.
What are the advantages of the process?
The advantages of the separating production process Plasma cutting at a glance:
- Suitable for all metals
- High cutting speed and productivity
- Smooth and low-working cut joint usually without burr
- Geringer input of heat into the material
- Can be used under the water surface
- Slow investment costs and high efficiency
- No pretreatment required
- Also suitable for markings
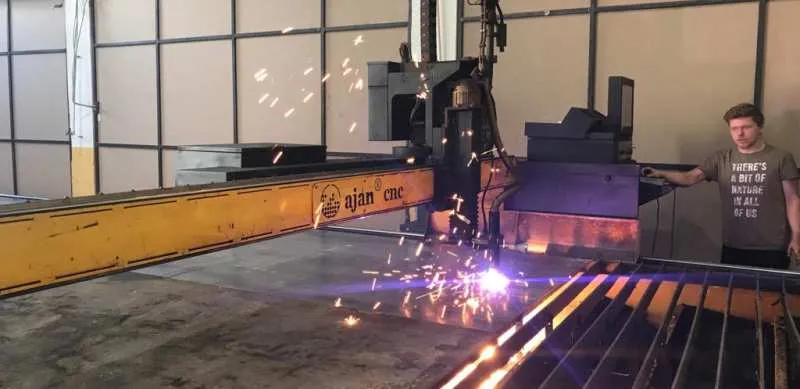
Plasma cutting system from Afec Makina Ins. San. Tic. Ltd.
Find companies for plasma cutting
If you are looking for a [Specialist in plasma cutting](/en/suppliers/plasma cutting), Techpilot will quickly find it. Europe's largest platform for the manufacturing industry connects technical buyers and suppliers to the Techpilot online portal. After free registration, buyers have access to the supplier pool where more than 24,000 companies are registered. Interesting contacts can be stored on your personal list or contact directly, if necessary also with a specific request. You can also make them public on the platform to achieve more reach. Incoming offers can be compared quickly and easily.
The Techpilot team consists of trained staff who are happy to help you with your concerns. In particular when creating enquiries, you will receive free phone support. The staff is well-known in the industry and is happy to support you.
Examples of jobs in the Techpilot marketplace
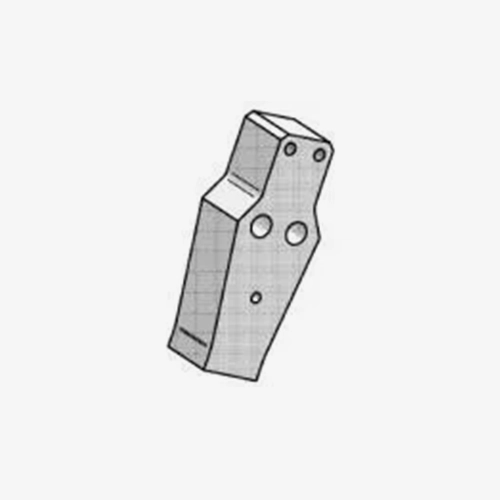
Plasma cutting impact plate
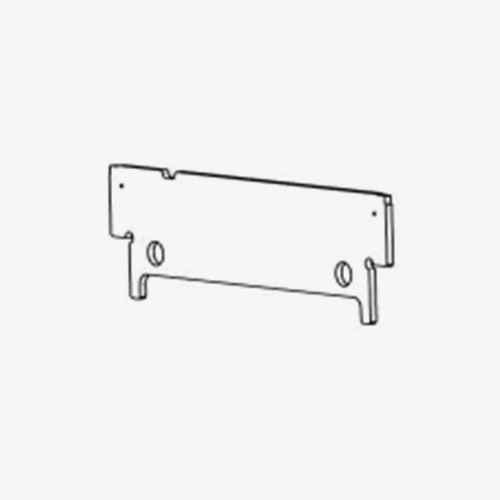
Plasma cutting traverse plate
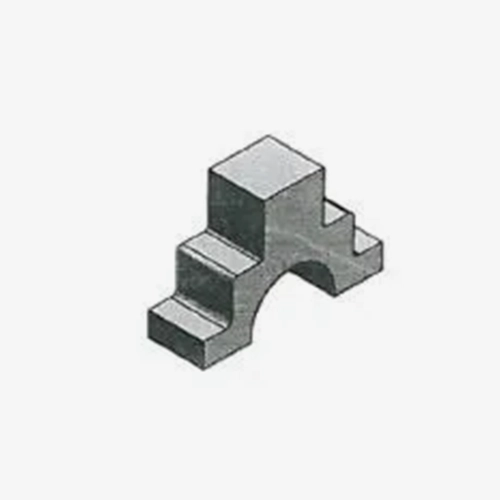
Plasma cutting raw parts
More about plasma cutting
Techpilot is Europe’s largest platform for the manufacturing industry.
For over 25 years, we’ve been connecting buyers, suppliers, and manufacturers that are the perfect match – enabling accurate price discovery for custom-made parts. Covering the full spectrum of mechanical components and supporting more than 280 manufacturing technologies, Techpilot is the market leader in Europe.Buyers gain instant access to qualified suppliers, full market transparency, and increased efficiency in their e-sourcing processes.
Suppliers benefit from high online visibility, extended media reach, and a profitable digital sales channel through Techpilot.
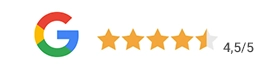
Lexicon Themes
- Metalworking (31)
- Plastic processing (8)
- Parts (8)
- Surface treatment (8)
- Welding (7)
- Machining (6)
- Sheet metal processing (6)
- Cutting (6)
- Turning (5)
- Manufacturing (5)
- Milling (4)
- Tool making (4)
- Suppliers (4)
- Casting (4)
- Procurement (4)
- Contract manufacturing (3)
- Profiles (3)
- Automation technology (2)
- Gearing & Thread (1)
- Forging (1)
- Wire processing (1)
- Heat treatment (1)