Water jet cutting
The water jet cutting is a separate Production process, where water is used under high pressure to cut through various materials. The water jet cutting is regarded as a particularly environmentally friendly, economical and material-friendly separation process.
Depending on the material to be separated, pure water or water with an abrasive addition is optionally used in water jet cutting. While pure water is suitable for cutting soft materials such as plastics, foams, films and paper, an abrasive water jet is required for separating steel, ceramics or glass. The water jet cutting has proven itself primarily in the cutting of composites and is applied across the industry due to its extensive advantages.
Technical foundations for water jet cutting
A water jet cutting machine is used for water jet cutting. This is a machine tool which is equipped with a CNC control and achieves a high degree of automation when cutting materials.
The water jet cutting machine consists essentially of the following components:
- Electric motor
- Valve
- Pure water and abrasive water nozzle
- Memory
- High pressure pipe
- Pressure transformer
- Water tank
- Water pump
- CNC-controlled guide rail
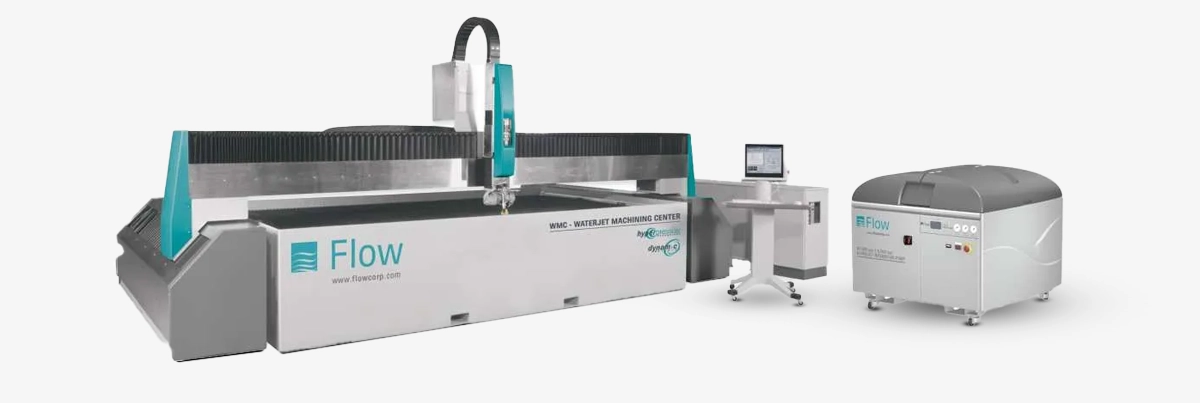
3D waterjet cutting machine at Arcut Waterjet cutting
The method of water jet cutting is technically relatively simple and differs mainly in dependence on the material to be cut. In principle, the process can be described as follows:
1. Generate high pressure
To cut materials with pure water, very high pressures are required. For this reason, the water jet cutting machine is equipped with an ultra high pressure pump. This is able to generate pressures of more than 6,000 bar. For comparison: Powerful water throwers from the police reach a pressure of about 20 bar.
2. Conversion of pressure into speed
In order that the water jet can be directed at the surface to be processed at the highest precision and speed, a nozzle converts the pressure into a high speed. Usually a tiny gemstone nozzle is used in this step. The resulting beam is not thicker than a human hair.
3.Addiction of abrasive (/enpending on material)
If harder materials such as steel, titanium or aluminum are to be cut, an abrasive agent is added to the water jet in an additional mixing chamber. These are usually pomegranate or olive sand. The abrasive agent significantly increases the cutting force and enables the precise separation of metallic and mineral materials as well as fiber composite materials.
4. exit at the cutting head
After the abrasive is sucked into the mixing chamber and mixed with the water, the mixture is concentrated and accelerated by the abrasive nozzle. At the cutting head, the beam finally emerges at almost four times the speed of sound and is directed onto the surface of the material.
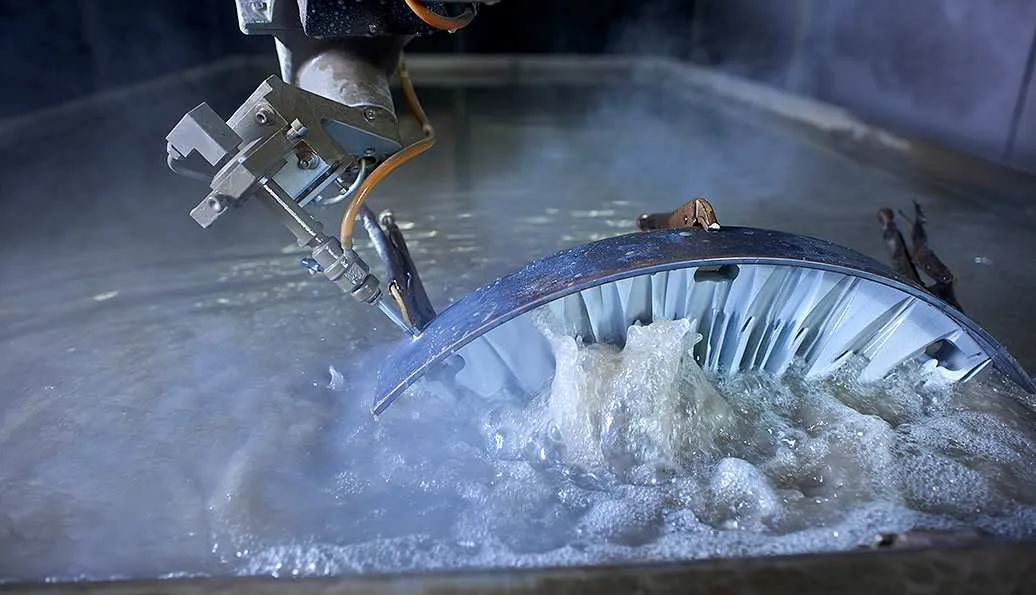
Waterjet AG waterjet cutting
Which materials can be cut?
When a pure water jet is used without the addition of abrasives, mainly soft and tough materials can be cut. These include:
- Paper, cardboard, carton
- Leather
- Rubber
- Plastics such as PVC
- Glass fiber reinforced plastic
- Carbon fiber reinforced plastic
- Insulating materials
- Steel
- Aluminium
- Fiber-plastic composite
- Natural stone
- Glass
- Concrete
- Ceramic
- Titanium
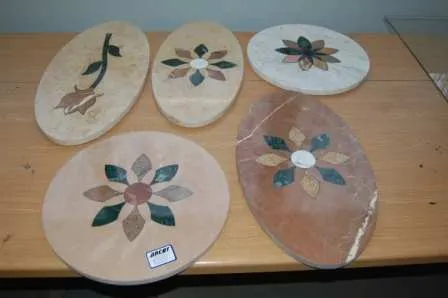
Marble table tops - company Arcut waterjet cutting
The various variations in water jet cutting
In addition to the method variants, pure water cutting and abrasive cutting is distinguished, in particular, between the two-dimensional and the three-dimensional cutting. In the case of two-dimensional water jet cutting, the water jet is always discharged at right angles to the workpiece surface. Accordingly, only flat cutting surfaces can be realized.
In addition, water jet cutting machines are also used whose axes permit multidimensional machining of the workpiece. Depending on the desired geometry of the cutting surface, the cutting head is guided over the component at different angles.
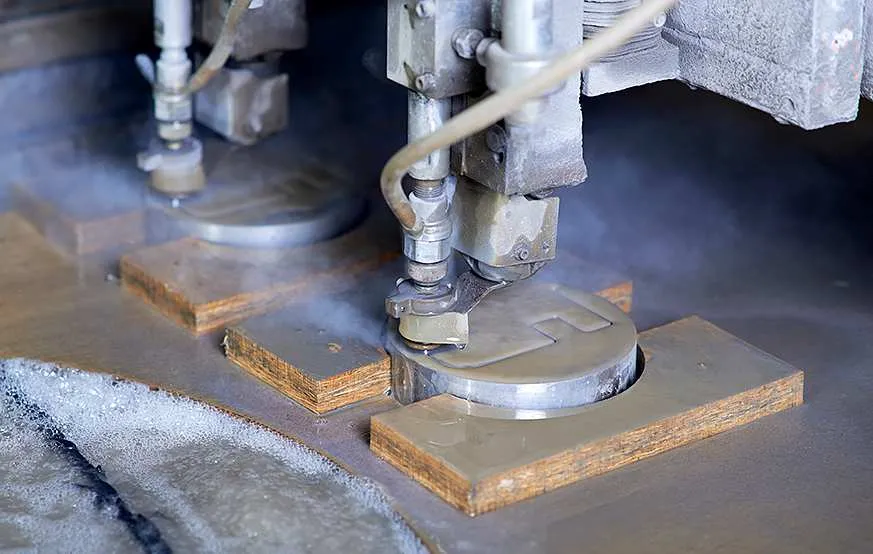
2D waterjet cutting - Company Waterjet AG
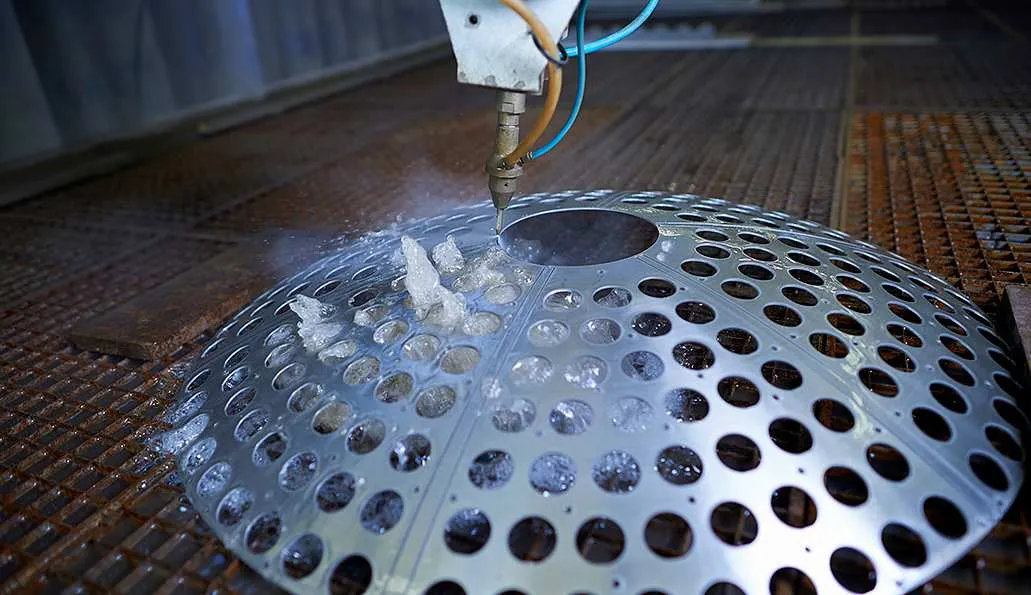
3D waterjet cutting - Company Waterjet AG
advantages of the method
The advantages of water jet cutting are diverse and have led to the fact that the process today enjoys great popularity across industries and materials. Among the most important benefits are:
- High environmental sustainability
- No cracking, structural change or material tension
- No formation of heat zones
- Multidimensional processing possible
- Fast production of prototypes
- Little material removal
- No expensive finishing required
- High economic efficiency
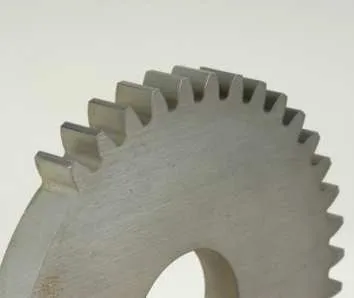
Alternative to milling - Company Arcut Waterjet Cutting
Find companies for waterjet cutting
If you are looking for a Company for water jet cutting, Techpilot will find a large number of specialized companies. Techpilot offers the largest supplier pool for orders from drawing parts in Europe and is therefore a suitable tool for finding new suppliers. Buyers use the platform completely free of charge. The useful supplier search function offers numerous filter functions and thus enables a quick and easy search for suitable contractors. Companies for complete machining with subsequent surface treatment can be found as well as companies specialized in technology.
You can either write orders publicly or send them to selected companies. The incoming offers are clearly compared and select the most suitable manufacturing operation for you. For all activities, the Techpilot team supports you by phone, chat or email. The technically trained staff has well-founded expertise in the industry and can help you in any way to create inquiries.
Examples of jobs in the Techpilot marketplace
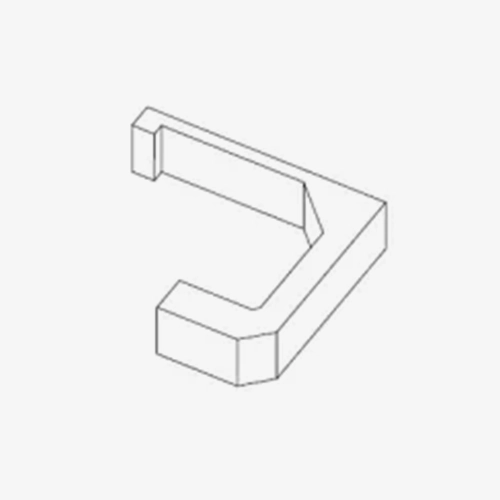
Waterjet cutting 2D construction steel
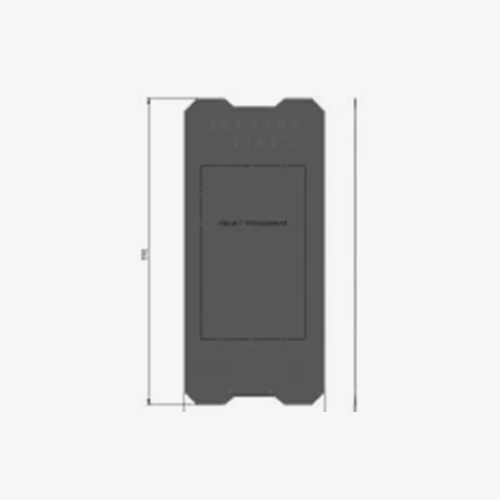
Water jet cutting 2D glass
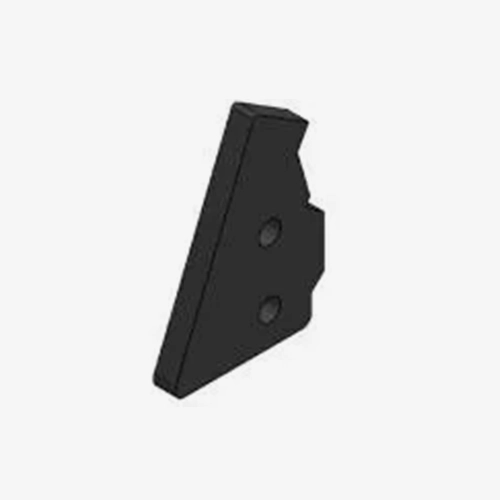
Request Water Stamping 2D Moosgummi
More about waterjet cutting
Techpilot is Europe’s largest platform for the manufacturing industry.
For over 25 years, we’ve been connecting buyers, suppliers, and manufacturers that are the perfect match – enabling accurate price discovery for custom-made parts. Covering the full spectrum of mechanical components and supporting more than 280 manufacturing technologies, Techpilot is the market leader in Europe.Buyers gain instant access to qualified suppliers, full market transparency, and increased efficiency in their e-sourcing processes.
Suppliers benefit from high online visibility, extended media reach, and a profitable digital sales channel through Techpilot.
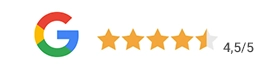
Lexicon Themes
- Metalworking (31)
- Plastic processing (8)
- Parts (8)
- Surface treatment (8)
- Welding (7)
- Machining (6)
- Sheet metal processing (6)
- Cutting (6)
- Turning (5)
- Manufacturing (5)
- Milling (4)
- Tool making (4)
- Suppliers (4)
- Casting (4)
- Procurement (4)
- Contract manufacturing (3)
- Profiles (3)
- Automation technology (2)
- Gearing & Thread (1)
- Forging (1)
- Wire processing (1)
- Heat treatment (1)