Powder coating
The powder coating is a coating process for conductive or conductive materials. In the process used above all for steel and aluminum, a powder coating is applied to the pretreated surface and subsequently crosslinked under the action of heat.
The powder coating protects the substrate from corrosion and scratches. In addition, the method of surface technology is used to influence the optical and functional properties of workpieces. Powder-coated products can be found in the following areas:
- Doors and windows
- Facade construction
- Machine and vehicle components
- Household nurses (white goods)
Classification of powder coating
The standard DIN 8580 assigns the powder coating of the 5th main group (coating). The process also counts as the subgroup of the electrostatic coating. This comprises all coating methods in which the coating material is attracted and applied to a grounded workpiece while simultaneously charging electrostatically. In addition to lacquer in the form of powder, liquid coating materials and short-stacked fibers (flake) are also used in electrostatic coating.
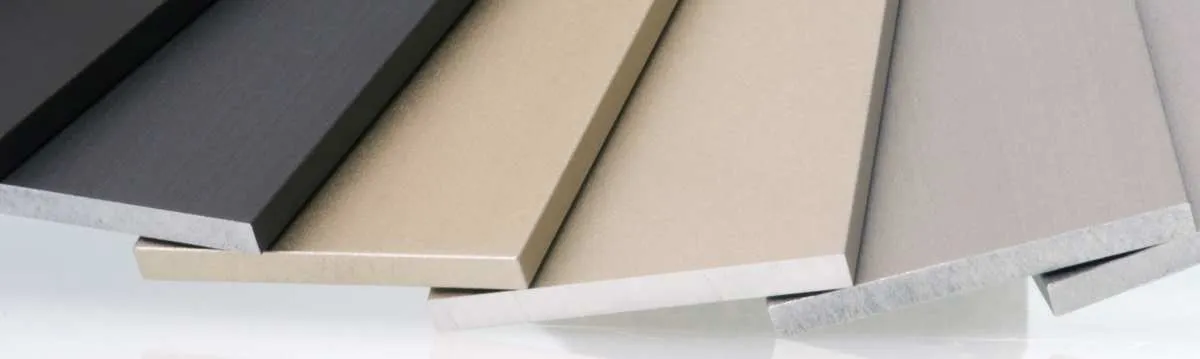
Powder coatings from Wilhelm Gronbach GmbH
Process sequence of the powder coating
The powder coating can be divided into three partial processes which are cross-linked in industrial production by automatic conveying devices. In this case, the workpieces often remain on the workpiece carriers during the entire process sequence. In addition, hand-painting systems are also used for applications with high flexibility.
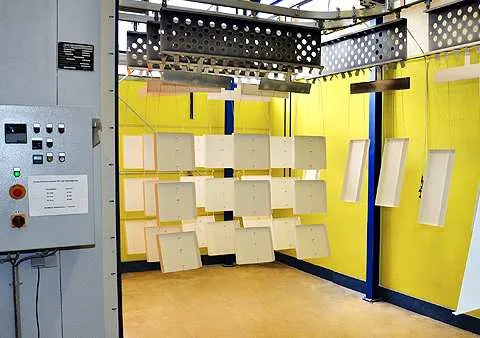
Powder coating system of the company HMT Rüffel GmbH
1. Pretreatment
The aim of the surface pretreatment is to create optimal starting conditions for the application of the paint. Only with this preparation can workpieces of high and constant quality be coated. The improper pretreatment leads to paint releases and craters in the lacquer layer. For this purpose, the workpiece must be freed from dust, adder, grate, fat and dirt, whereby the pretreatment can be distinguished between chemical and mechanical methods. In aluminum, the natural oxide layer is also removed. In this step, a conversion layer is likewise produced on the workpiece. This increases the corrosion protection of the base material and improves the adhesion of the lacquer to be applied. The finish of the pretreatment is the drying of the workpiece.
2. Application of the paint
The lacquer powder is applied to the surface by means of powder spray guns, the introduction of dust and dirt being avoided. The powder spray gun produces a charged powder cloud by means of various methods for charging. The lacquer particles adhere electrostatically and form a layer on the workpiece ground over the workpiece carrier.
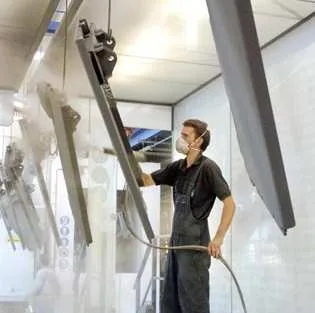
Powder coating by hand at Jud GmbH & Co. KG
3. Crosslinking and drying
The wetting of the powder coating layer takes place in an oven or dryer at temperatures between 110° and 250° C. The dwell time of the workpiece in the furnace is composed of the heating time, depending on the workpiece thickness, and the holding time, depending on the lacquer material. Low-temperature lacquers which crosslink at temperatures below 140° C. require increased baking time, with customary holding times being between 5 and 30 minutes. The workpiece throughput and plant-specific factors also affect the setting of the process. Layer thicknesses between 60 and 120 micrometers are produced with the powder coating, it being possible to deviate from this region both upwardly and downwardly.
Applications of powder coating
In addition to the high resource efficiency, the advantages of powder coating also include the great freedoms for surface design:
Wide colour spectrum, also multicolored coatings
Different degrees of gloss (matt to high gloss)
Structured surfaces (smooth to coarse structure)
Effects (metallic, glitter, etc.)
- Wide colour spectrum, also multicolored coatings
- Different degrees of gloss (matt to high gloss)
- Structured surfaces (smooth to coarse)
- Effects (metallic, glitter, etc.)
In addition to protecting the surface and increasing its optical quality, the powder coating also serves to influence functional properties. The process is suitable, inter alia, for producing antimicrobiological or antistatic surfaces.
Due to the requirements for temperature stability and conductivity, the powder coating is used primarily for metallic materials. The coating process is particularly widespread for the following materials, each of which requires a specific pretreatment:
- Steel
- Galvanized steel
- Aluminium
The development of lacquer systems which require a low baking temperature and are suitable for non-metallic workpieces made of plastic or composite materials is particularly important for automotive lightweight construction.
Find companies for powder coating
Techpilot, Europe's largest platform for drawing parts, connects buyers and contractors for concrete contracts or long-term partnerships. Numerous Powder Coating will find buyers with the Techpilot supplier search.
As a buyer, use all Techpilot functions for free. After your registration, start the search for suitable suppliers or upload your request directly. Incoming offers compare quickly and easily with price, delivery time and quality. So keep an overview and save time.
Techpilot will provide you with trained staff who will advise you by phone or e-mail at any time. The technically experienced team will help you to achieve ideally suited suppliers.
Examples of jobs in the Techpilot marketplace
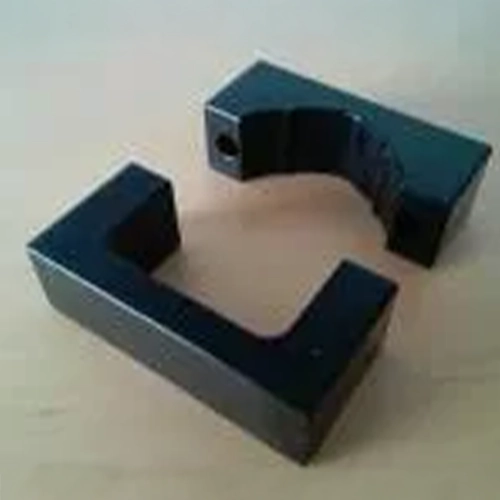
Powder coating of aluminum parts
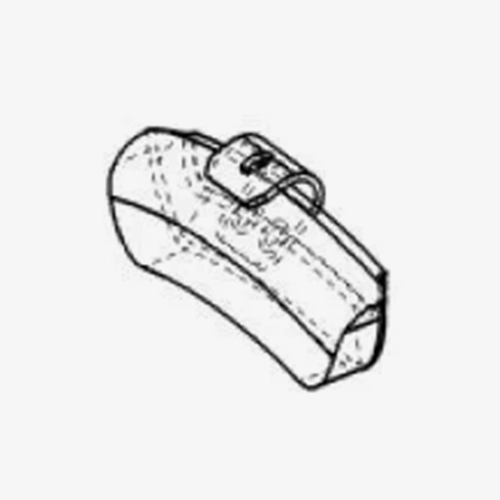
Powder coating of balancing weights
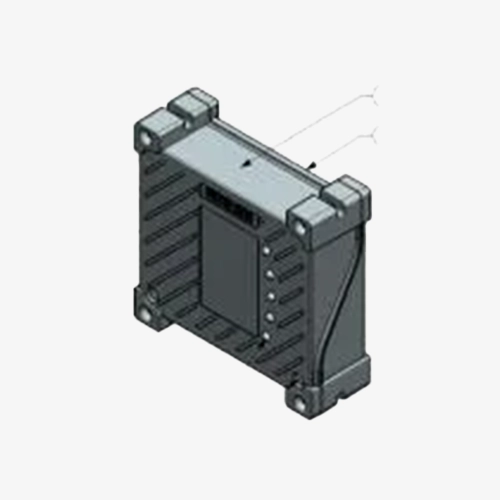
Powder coating with salt water resistance
More about powder coating
Techpilot is Europe’s largest platform for the manufacturing industry.
For over 25 years, we’ve been connecting buyers, suppliers, and manufacturers that are the perfect match – enabling accurate price discovery for custom-made parts. Covering the full spectrum of mechanical components and supporting more than 280 manufacturing technologies, Techpilot is the market leader in Europe.Buyers gain instant access to qualified suppliers, full market transparency, and increased efficiency in their e-sourcing processes.
Suppliers benefit from high online visibility, extended media reach, and a profitable digital sales channel through Techpilot.
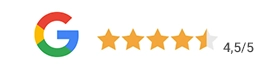
Lexicon Themes
- Metalworking (31)
- Plastic processing (8)
- Parts (8)
- Surface treatment (8)
- Welding (7)
- Machining (6)
- Sheet metal processing (6)
- Cutting (6)
- Turning (5)
- Manufacturing (5)
- Milling (4)
- Tool making (4)
- Suppliers (4)
- Casting (4)
- Procurement (4)
- Contract manufacturing (3)
- Profiles (3)
- Automation technology (2)
- Gearing & Thread (1)
- Forging (1)
- Wire processing (1)
- Heat treatment (1)