Punching
Stamping is a separation process for the production of flat parts from various materials such as sheet metal, cardboard and textiles with a punch press or by punching with a hammer head on a cutting tool.
Stamping is mainly used to hole flat materials. The minimum equipment of a punching device consists of two tool parts: a holder for punches and a holder for dies. When the punch is inserted into the die, the material is separated by a shear cut.
Punching methods in practice
Punching frequently occurs in the electrical and automotive industry. The stamping process is also common in the production of household goods and packaging for the food, medical and pharmaceutical industries.
How to punch
During punching, a distinction is made between two methods: stroke punching and rotational punching.
Hub dance:
The device for lifting punching consists of a press equipped with a Stamping tool. This is usually a flat upper and lower tool. The punch is located in the upper tool. A matching die is mounted in the lower tool. As a result of a precise alignment of the tools with respect to one another, the punch hits exactly into the die where the material is broken. Important to remember: During stroke punching, the full punching force acts on the entire surface to be machined.
Rotation dances:
During rotary punching, the punching tools are mounted in the so-called high-precision bearings. Here, too, the tools are clamped with dies above, the die is arranged at the bottom. The material to be machined is now continuously pushed between the two tools during rotation punching. Therefore also the name. It leads back to the rotating tools. Important to remember: Only a punctual load is produced, so the punching force is lower than in the case of the lifting punching. The advantage of this process: so-called continuous materials can be processed more precisely and more quickly.
The punching tool
There are two important tools: the stamp and the Matritze. The stamp represents the inner shape of the desired manufactured part. The Matritze has an opening matching the stamp. A practical example from everyday life would be the Locher.
Advantages
- Highest precision:
Stamping is more precise than Laser cutting when processing thin sheet metal. With guaranteed accuracy of +/-0.1 mm. No scaling at the cut edges. - Variety:
The stamping process is used to work with a wide range of different materials. - Very fast with many cuts:
With a large number of cuts in one sheet, stamping offers the highest speed. - Cost-effective:
Depending on order volume, stamping can be the most cost-effective solution – especially for relatively high quantities.
Disadvantages
- Limit at 8 mm:
Stamping is only suitable for cutting and forming thin sheets up to a thickness of 8 mm. - Deformation:
For particularly large parts that are heavily processed using the stamping method, the material may bend in some areas. - Too specific:
The stamping process often requires the purchase or development of special tools.
Learn more about stamping
Techpilot is Europe’s largest platform for the manufacturing industry.
For over 25 years, we’ve been connecting buyers, suppliers, and manufacturers that are the perfect match – enabling accurate price discovery for custom-made parts. Covering the full spectrum of mechanical components and supporting more than 280 manufacturing technologies, Techpilot is the market leader in Europe.Buyers gain instant access to qualified suppliers, full market transparency, and increased efficiency in their e-sourcing processes.
Suppliers benefit from high online visibility, extended media reach, and a profitable digital sales channel through Techpilot.
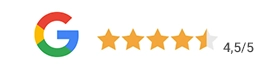
Lexicon Themes
- Metalworking (31)
- Plastic processing (8)
- Parts (8)
- Surface treatment (8)
- Welding (7)
- Machining (6)
- Sheet metal processing (6)
- Cutting (6)
- Turning (5)
- Manufacturing (5)
- Milling (4)
- Tool making (4)
- Suppliers (4)
- Casting (4)
- Procurement (4)
- Contract manufacturing (3)
- Profiles (3)
- Automation technology (2)
- Gearing & Thread (1)
- Forging (1)
- Wire processing (1)
- Heat treatment (1)