MAG welding
The MAG welding is part of the group of gas-protected metal arc welding processes, in which a wire electrode is melted under protective gas, and is widely used in industrial production for joining metallic materials.
In the case of MAG welding, the permanent connection of metals is achieved using strong heat and welding aids. The heat input for the melting welding process causes an electric arc. The inserted wire electrode flows together with the melted base material as a welding additive and contributes to the formation of the weld seam. The method is distinguished by a high processing speed and the possibility of automation. It is therefore particularly suitable for industrial applications.
Technical basics for MAG welding
The MAG welding is described by the standard EN ISO 4063 (process 135) and is named after the active protective gas used (metal active gas welding). Furthermore, the MAG welding is a group of protective gas welding, the processes of which are characterized by the use of protective gases to avoid unwanted chemical reactions:
- Metal protection gas welding (MSG)
- Tungsten inert gas welding (WIG/TIG)
- Orbital welding
- Plasma welding
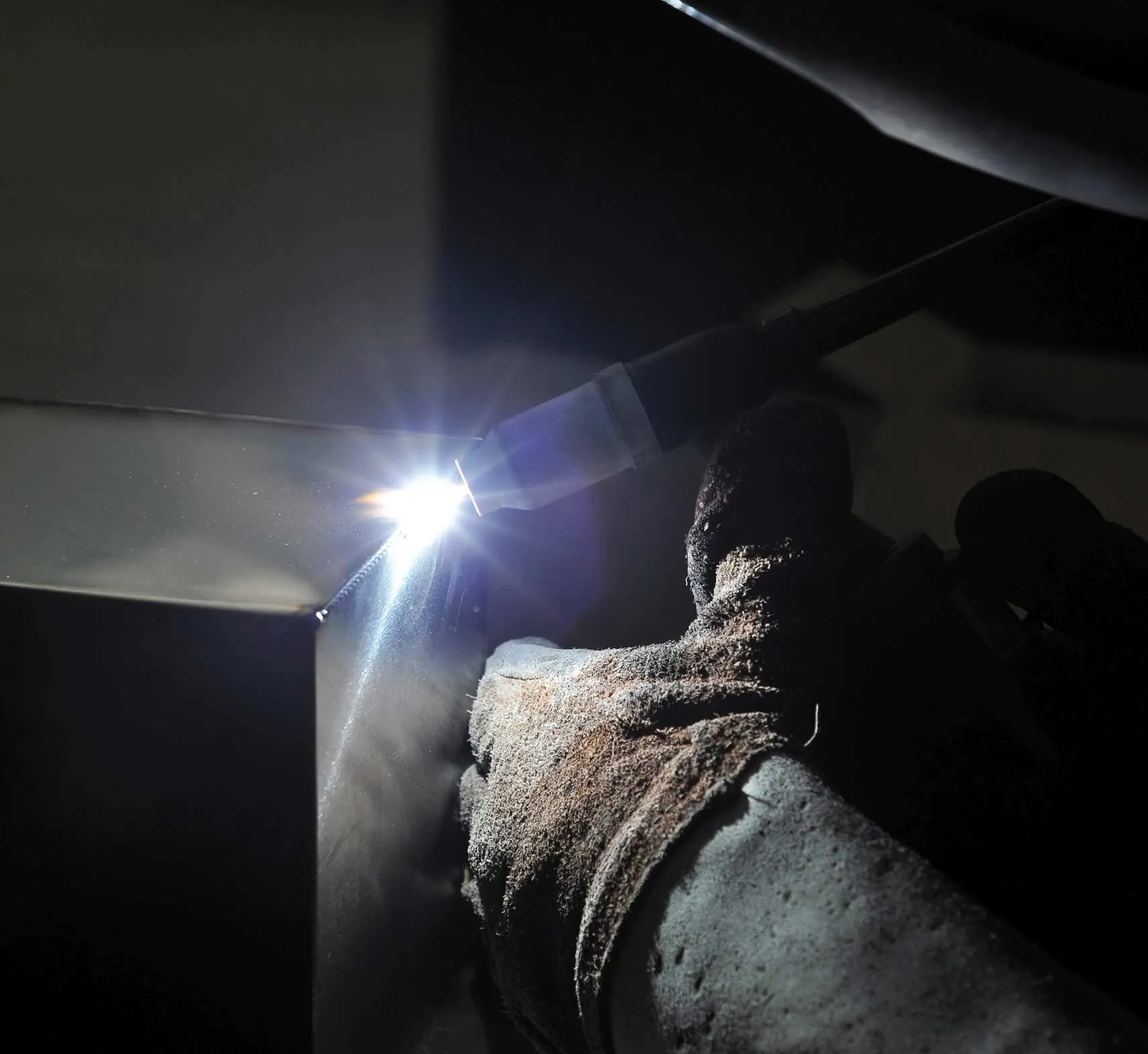
Protection gas welding at Stahlbau Mayr Heiz- und Energietechnik
MAG welding belongs to the subgroup of metal inert gas welding. It differs from other shielding gas processes through the use of consumable electrodes. With an otherwise identical process, the primary distinction lies in the type of shielding gas used.
- Metal Active Gas Welding (MAG)
- Metal Inert Gas Welding (MIG)
In these welding methods, a continuously supplied wire electrode is supplied with current shortly before the outlet from the burner. As a result, an arc can burn between the electrode end and the workpiece. At the same time, the protective gas flows out of the protective gas nozzle, which concentrically surrounds the electrode.
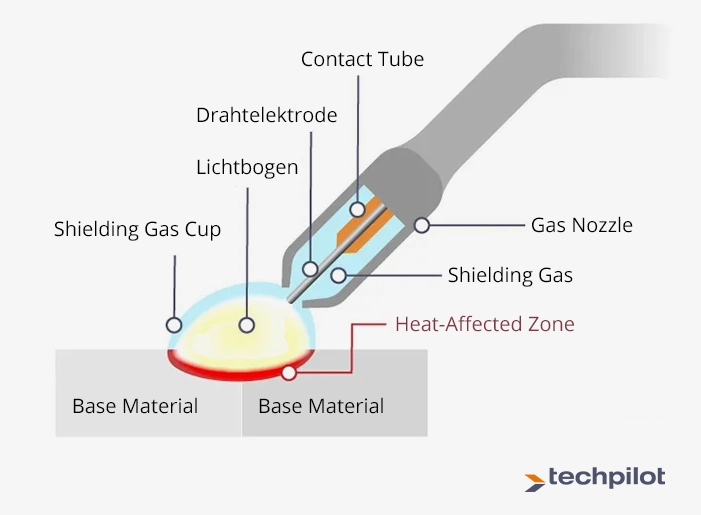
MAG welding operation
The thickness of the welding wire may vary, but diameters of 1 mm are common. In addition to solid wire electrodes, so-called filling or tube wires are also used in MAG welding. Depending on the requirements of the welding task, they are filled with rutile or basic powders. These weld additives serve the same purpose as the sheathing of the rod electrode during E-hand welding, i.e. for example the increase in the welding volume or the oxidation protection of the melt.
The role of the protective gas in MAG welding
The MAG welding is characterized by the use of active protective gases. In particular, pure carbon dioxide or argon are used as mixing gas. In the case of MAG welding, the protective gas not only has a protective function, but also serves for the purposeful design of the welding connection by influencing the following parameters:
- Inflammation behaviour
- arc stability
- Metallurgy of the workpiece

MAG welding systems at Bunorm AG
Applications for MAG welding
With the MAG welding, thin sheets can be welded. At the same time, the process is suitable for use with steels of almost all varieties:
- Steel construction
- Stainless steel
- Other high-alloy materials
On the other hand, the MIG welding is used primarily in non-ferrous metals (NE-metals) such as aluminum or copper. The inert protective gas ensures that the welding bath does not react with the atmosphere. From the MIG welding, the MAG welding is also eliminated by the arc types used. If long or short arcs are used in the MAG welding, the MIG welding spray or pulse arc is used.
MAG welded components
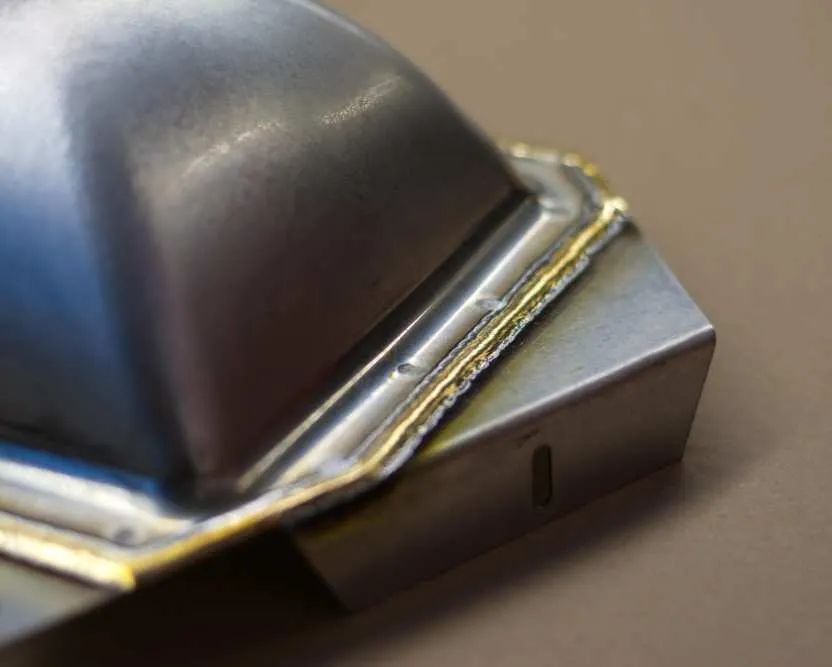
MAG welding at Dino Welding GmbH
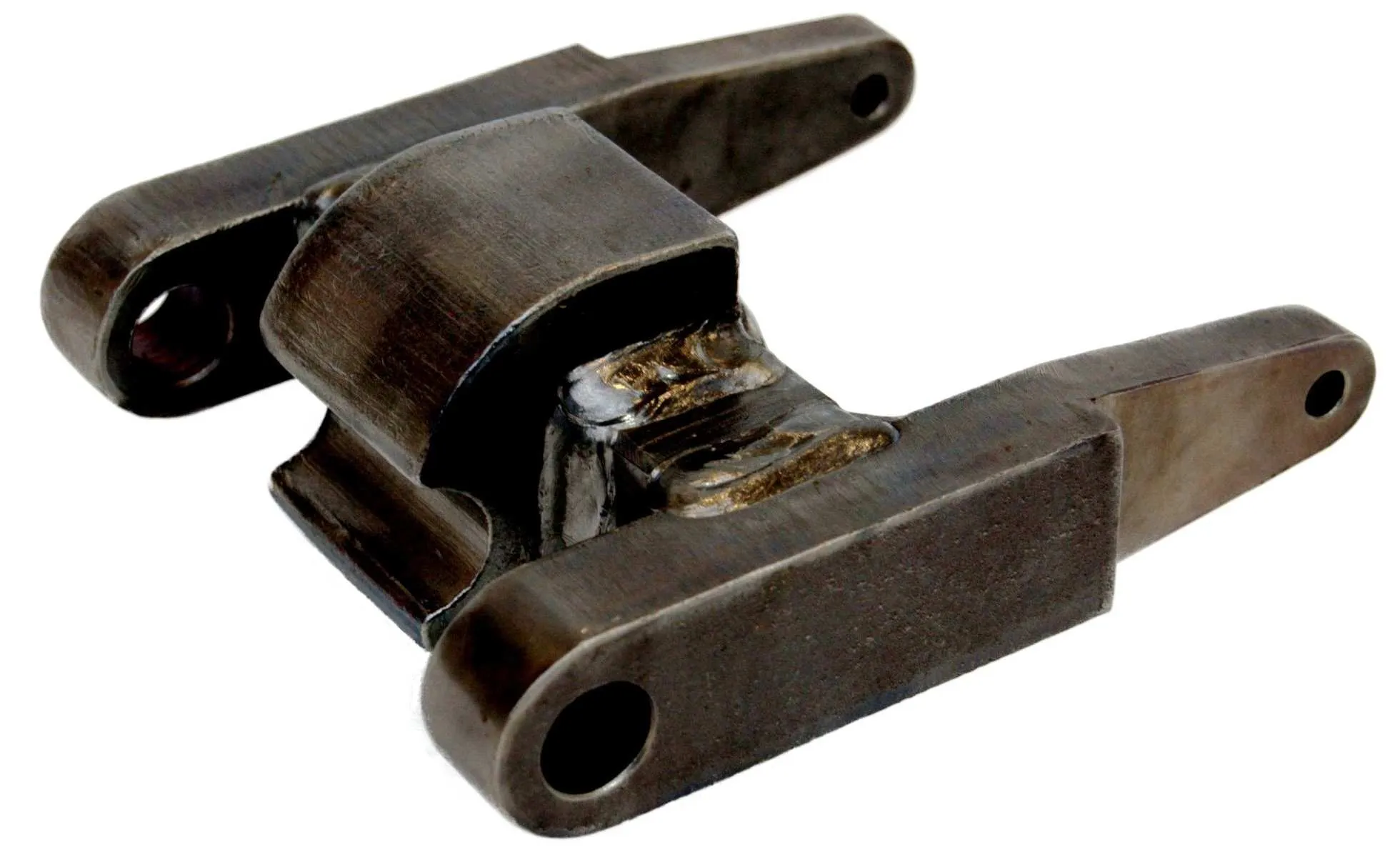
MAG welding at the company Lehnen GmbH
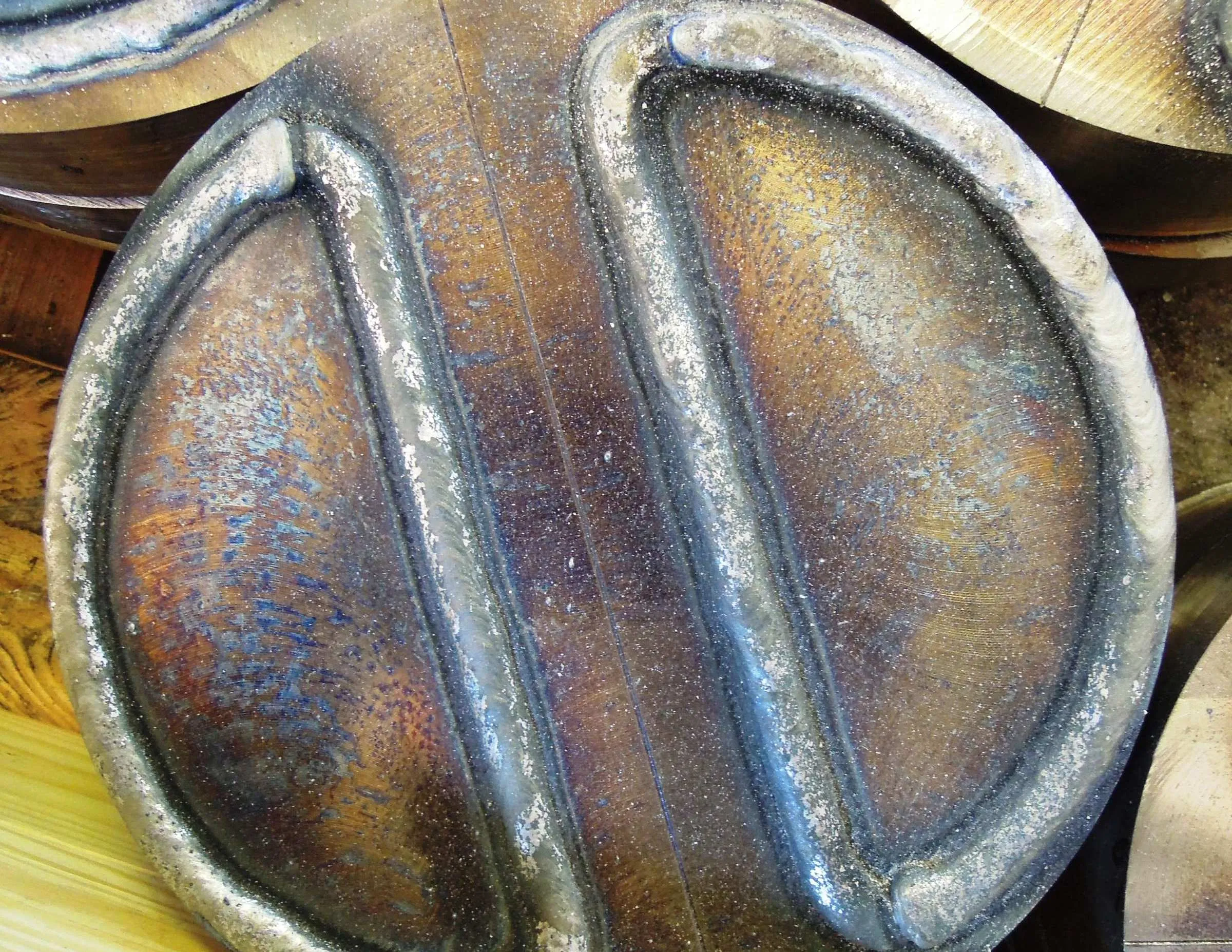
MAG welding at the company innojoin GmbH
Advantages of MAG Welding
In industrial applications, the disadvantages of the method, such as the limited suitability for use outdoors and the comparatively complicated setting of the process parameters, can be well controlled.
Find companies for MAG welding
Inert Gas Shielded Arc Welding Mig Mag can be found at Techpilot. Europe's largest platform for orders from drawing parts provides an application for buyers and suppliers to find new contacts and write out orders. Buyers use all Techpilot functions free of charge. After registration they have access to the extensive supplier search with various filter options. Interesting supplier profiles can be stored on the personal list to contact them and send inquiries directly.
Orders for MAG welding are either sent to suitable companies or posted on our website. The offers of interested companies are clearly managed and compared in the Techpilot account. This saves laborious manual search for appropriate operations and offers an excellent opportunity for networking in the corresponding industry.
Examples of jobs in the Techpilot marketplace
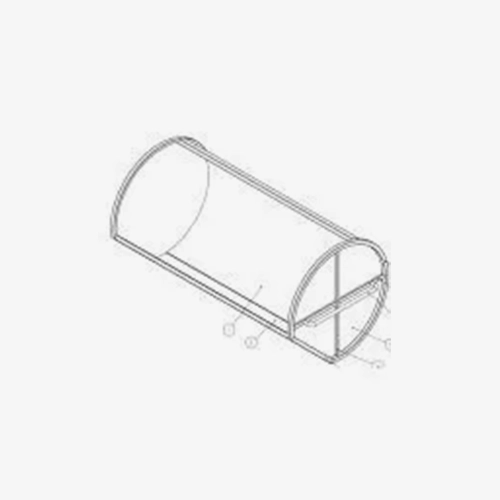
MAG welding stainless steel
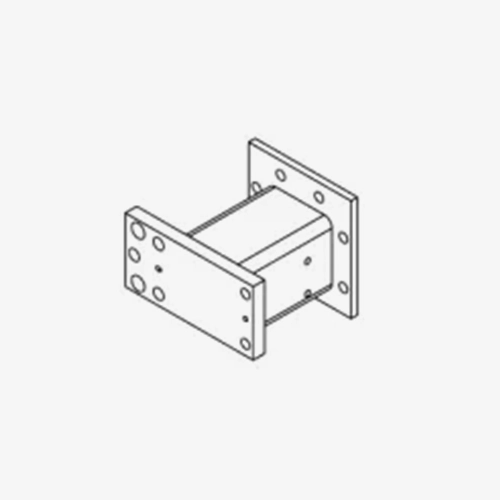
MAG welding construction steel
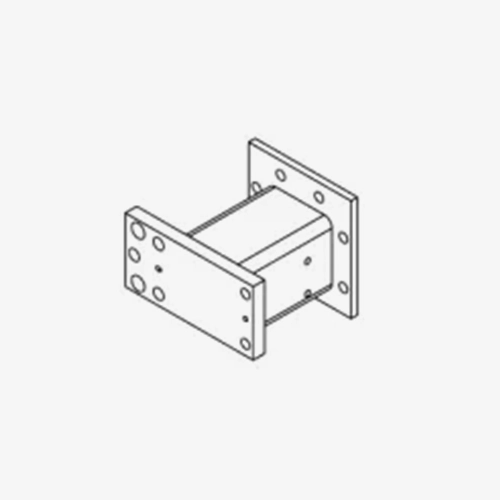
MAG welding construction steel
More about MAG welding
Techpilot is Europe’s largest platform for the manufacturing industry.
For over 25 years, we’ve been connecting buyers, suppliers, and manufacturers that are the perfect match – enabling accurate price discovery for custom-made parts. Covering the full spectrum of mechanical components and supporting more than 280 manufacturing technologies, Techpilot is the market leader in Europe.Buyers gain instant access to qualified suppliers, full market transparency, and increased efficiency in their e-sourcing processes.
Suppliers benefit from high online visibility, extended media reach, and a profitable digital sales channel through Techpilot.
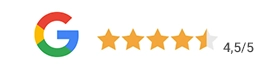
Lexicon Themes
- Metalworking (31)
- Plastic processing (8)
- Parts (8)
- Surface treatment (8)
- Welding (7)
- Machining (6)
- Sheet metal processing (6)
- Cutting (6)
- Turning (5)
- Manufacturing (5)
- Milling (4)
- Tool making (4)
- Suppliers (4)
- Casting (4)
- Procurement (4)
- Contract manufacturing (3)
- Profiles (3)
- Automation technology (2)
- Gearing & Thread (1)
- Forging (1)
- Wire processing (1)
- Heat treatment (1)