Laser beam welding
The laser welding is one of the following Production methods and is used in the industry to connect metallic components and thermoplastics. The method is based on the punctual energy supply via a laser beam, wherein usually no additional material is used.
Thanks to the energy-intensive laser beam, laser welding is characterized by a very high welding speed, a low thermal distortion in the component and a narrow and precise welding seam. It is therefore used in high-precision applications in Tool construction, in the automotive industry, in steel construction, in shipbuilding, in aerospace and in other industries.
Technical foundations for laser welding
The basis of laser beam welding is a high-performance laser that generates an energy-intensive light beam with several kilowatts of power. In laser welding, Nd:YAG lasers or carbon dioxide lasers are generally used. In addition, however, diode lasers are also becoming increasingly important, since very high energy intensities can be realized with high efficiency.
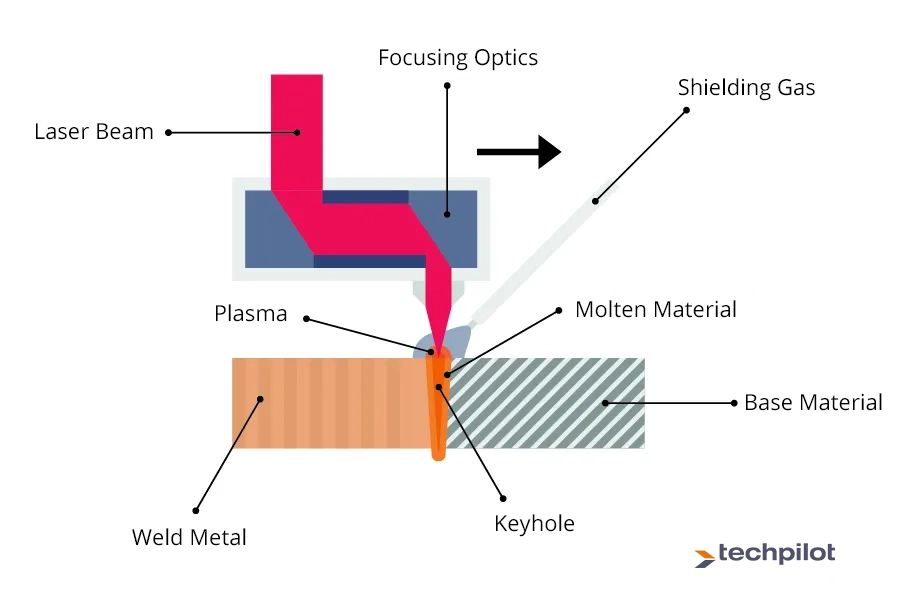
Laser welding operation
The generated light beam is focused by optics onto a spot approximately 0.2 to 0.3 mm in diameter. The high energy density of the laser beam causes the material to melt quickly at that point. At the same time, shielding gas is supplied to protect the workpiece from harmful effects of the surrounding air, such as oxidation or moisture absorption. High-purity argon is commonly used as a shielding gas in laser welding.
Once the melting point of the material is reached, increasing absorption in the workpiece leads to vaporization. This process creates what is known as a keyhole—a vapor channel that absorbs nearly all of the laser energy and thus generates laser-induced plasma.
From the vapor channel, heat spreads through the workpiece, creating a molten zone around the channel. As the laser beam moves along the desired contour, the melt solidifies to form a weld seam. Due to the high energy density, melting and solidification occur within fractions of a second, allowing very high welding speeds. Under ideal conditions—for example, with a continuous straight seam—welding speeds of up to 60 meters per minute can be achieved.
Laser welding can be used to join not only metallic materials but also thermoplastic plastics and ceramic components.
The Laser cutting follows a similar method construction, wherein the high energy intensity of the laser beam is used for separating solid bodies and not for connecting.
When and what is laser welding used for?
In the metal and partly also in the plastic processing industry, laser welding has prevailed in the precise and fast joining of components. The typical applications of the method include, for example, the production of:
- Transmission parts of car and truck
- stone extractors for medical technology
- gastight sensor housings
- pole tubes
- Engine housings
- Cranks with internal toothing
- Sheet metal assemblies
- Roller levers
- AGR valves
- Heart pacemakers
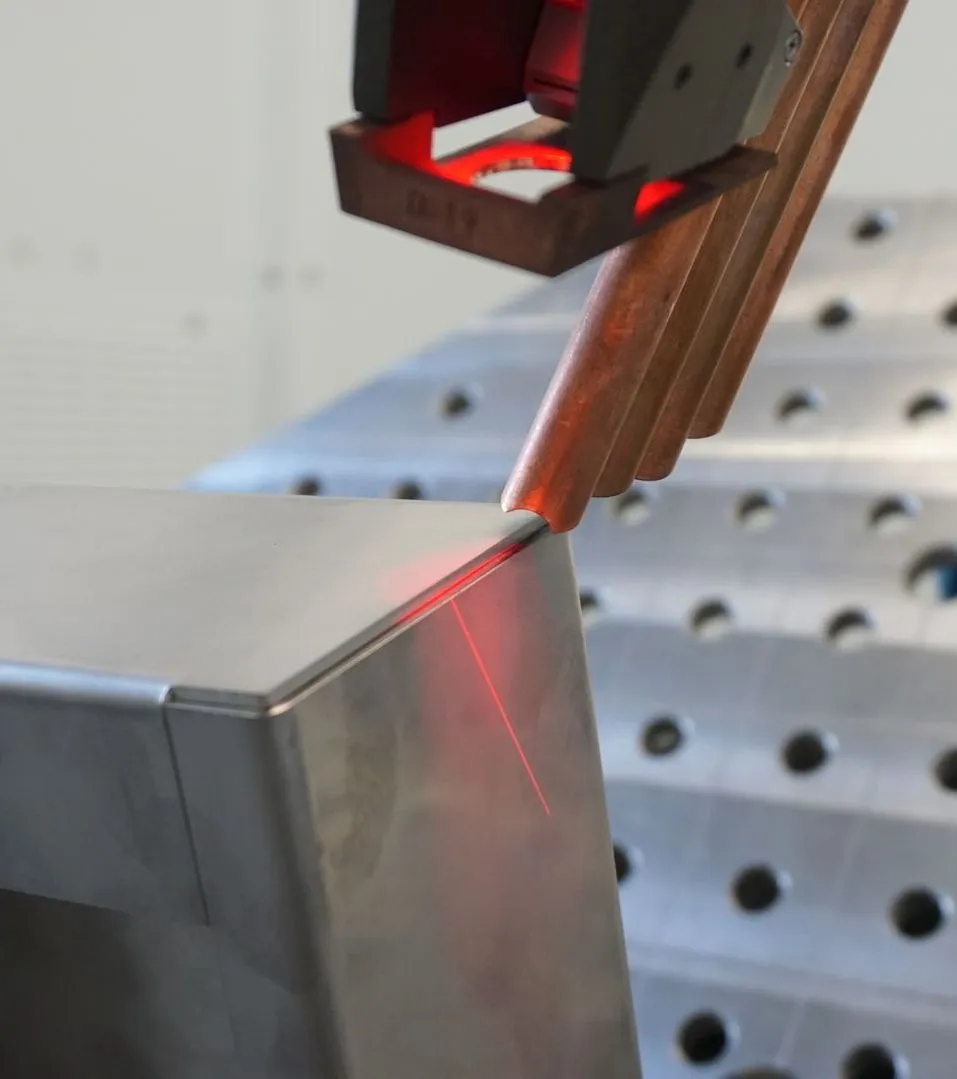
Laser welding at the company Laserschweisscenter.de
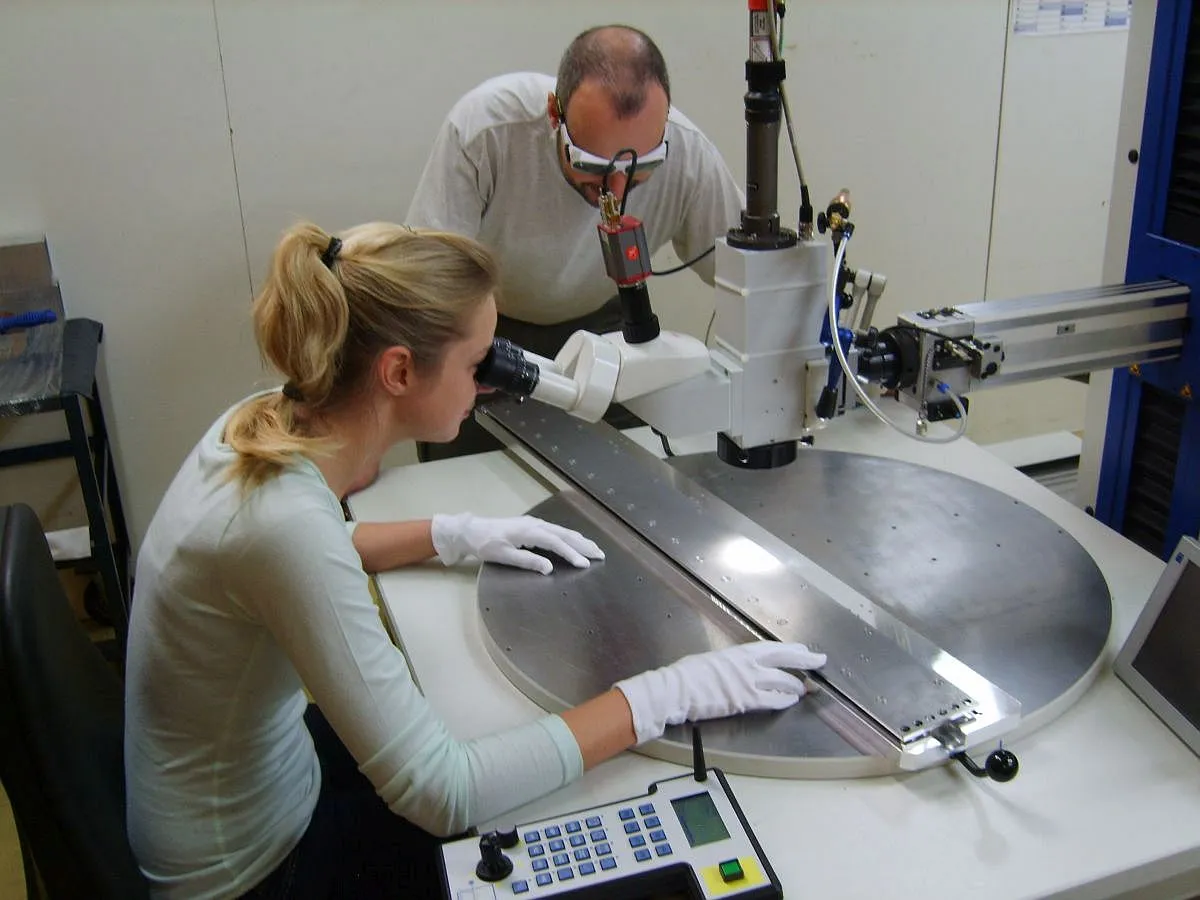
Laser welding plant at REUTER Vacuumlöttechnik GmbH & Co. KG
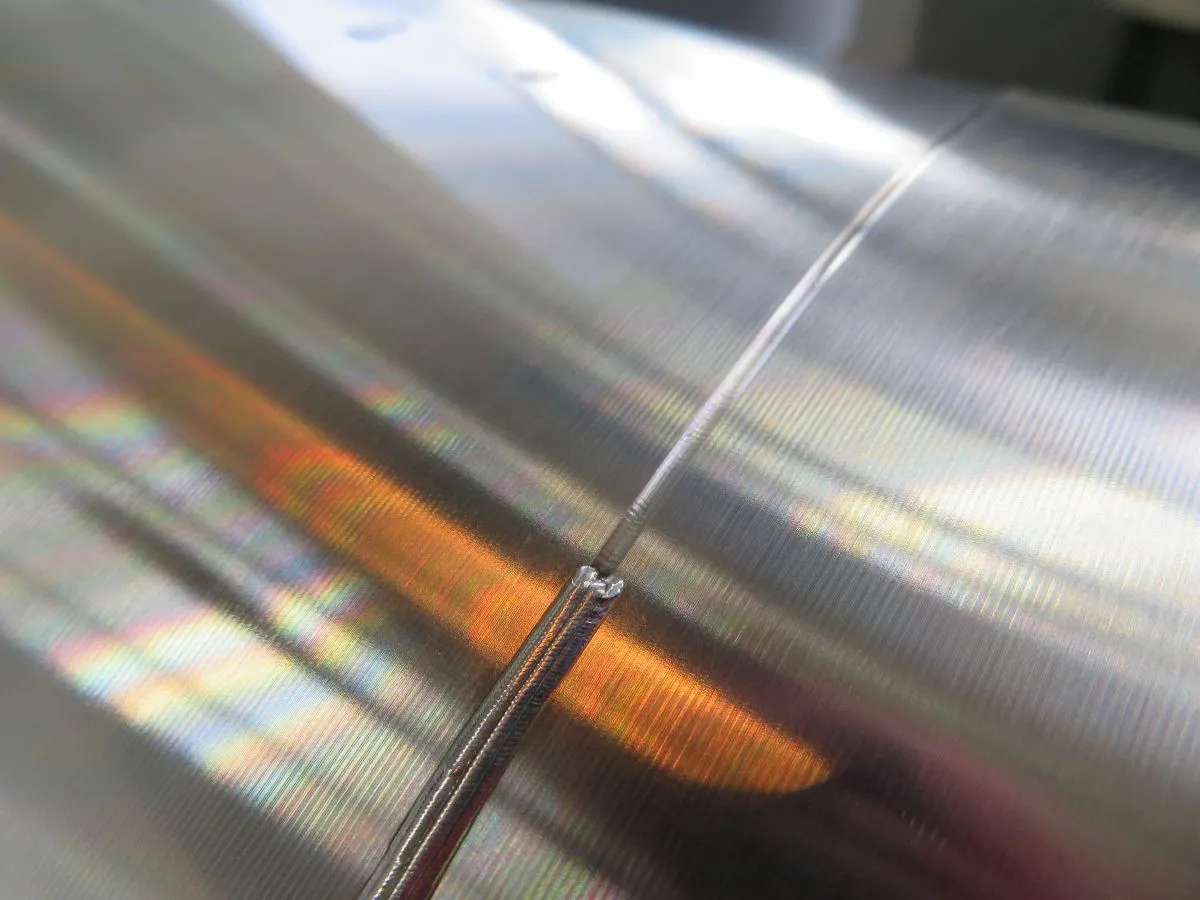
Laser welding of a damaged roller - BLT GmbH Bergmann Laser Technik
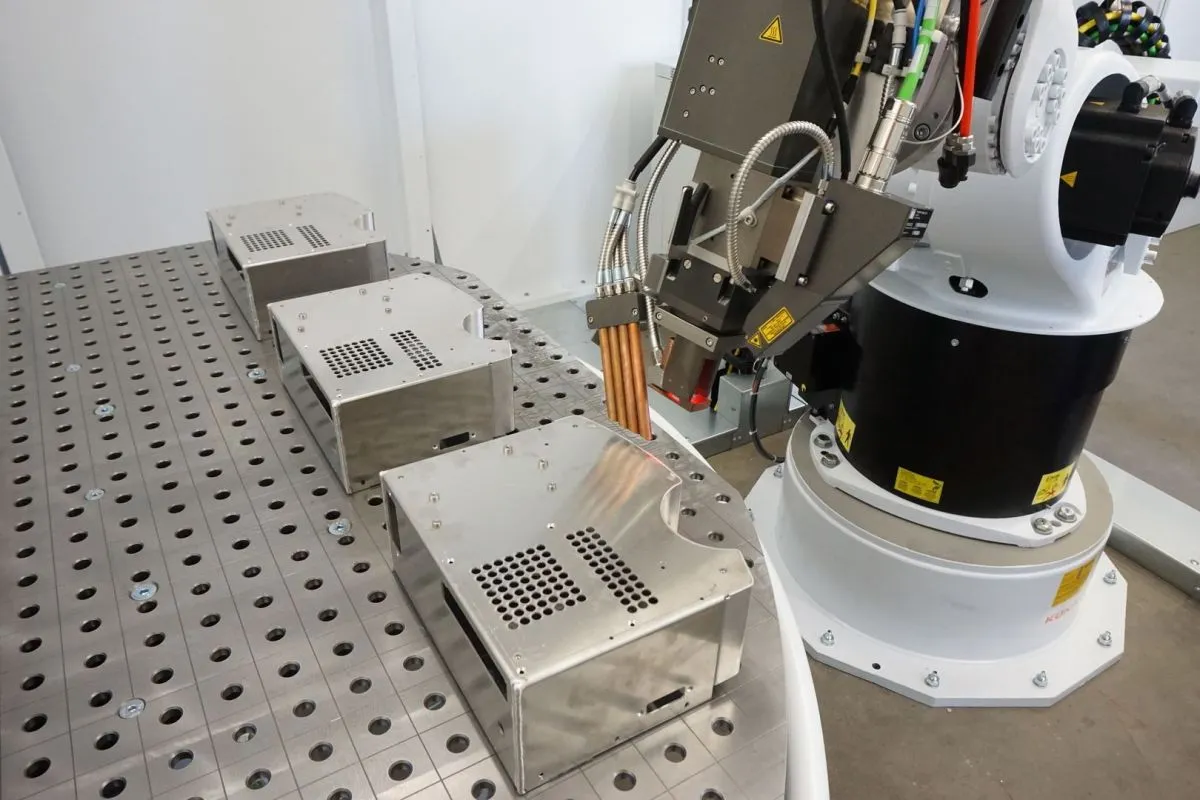
Laser welding robot at BSW-anlagenbau GmbH
Technical Variants of Laser Welding
Laser welding allows the shape and quality of the weld seam to be varied by adjusting energy intensity or other process parameters. The following provides a brief overview of the key technical variants of the welding process.
Conduction Welding: In this variant, the laser intensity is kept below the critical threshold, preventing the formation of metal plasma. As a result, there is no deep welding effect, and the weld penetration remains particularly shallow.
Deep Penetration Welding: This is the most common variant of laser welding. The intensity is higher than in conduction welding, causing the described vaporization effect and the formation of laser-induced plasma.
Spot and Seam Welding: This variant produces either tiny weld spots with diameters under 0.1 mm or long weld seams with very narrow geometry. Spot and seam welding provides high-strength connections with minimal heat input.
Scanner Welding: In scanner welding, neither the processing head nor the workpiece needs to be moved to position the laser beam. Instead, a galvanometrically controlled rotating mirror is used to deflect and position the beam.
Advantages and Disadvantages of the Process
Laser welding has proven itself in industry due to its many advantages in joining components where high speed, precision, and minimal thermal distortion are required. The main pros and cons of the process are outlined below:
Advantages
- High welding speed
- Contactless joining of components
- Slim weld geometry with high depth-to-width ratio
- Low thermal input, resulting in minimal thermal distortion on the component
- High degree of automation possible with modern laser welding systems
- Various materials can be welded
Disadvantages
- Large gap widths usually cannot be bridged
- High equipment costs
- Enclosed and secure working environment required
Find companies for laser welding
You are looking for [Suppliers for Laser Welding](/en/suppliers/laser Welding) ? At Techpilot, Europe's largest platform for the manufacturing industry, you will quickly find solutions. Over 24,000 plants are registered and easy to search thanks to extensive filter functions. You store interesting contacts in your personal address book and contact the contact persons – if necessary also directly with your specific request. Techpilot offers a practical tool with its web solution for tendering processes, which facilitates work with inquiries. Get market transparency by comparing incoming offers and find directly new suppliers that suit you.
The Techpilot team is available by phone or e-mail. The trained staff are technically trained and will be happy to provide you with tips for creating enquiries and the general handling of the platform.
Examples of jobs in the Techpilot marketplace
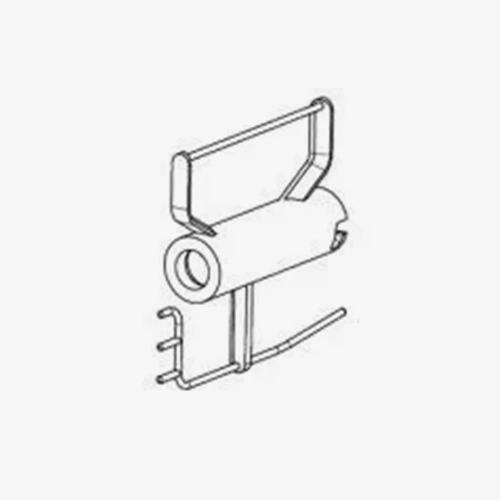
Rotary milling part with laser welding
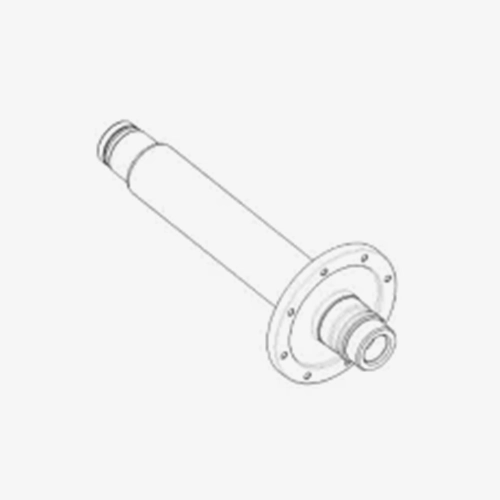
Laser welding of a rotor shaft
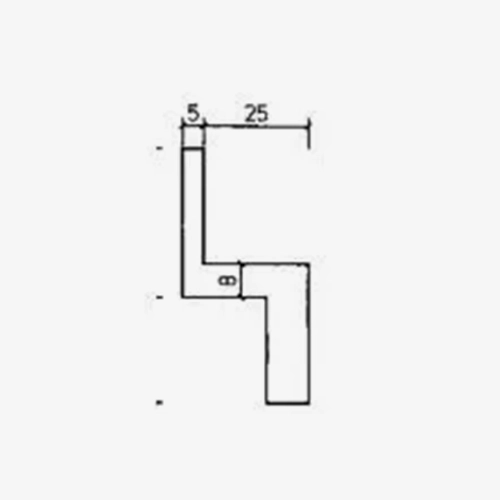
Laser welding of a Z-profile
More about laser welding
Techpilot is Europe’s largest platform for the manufacturing industry.
For over 25 years, we’ve been connecting buyers, suppliers, and manufacturers that are the perfect match – enabling accurate price discovery for custom-made parts. Covering the full spectrum of mechanical components and supporting more than 280 manufacturing technologies, Techpilot is the market leader in Europe.Buyers gain instant access to qualified suppliers, full market transparency, and increased efficiency in their e-sourcing processes.
Suppliers benefit from high online visibility, extended media reach, and a profitable digital sales channel through Techpilot.
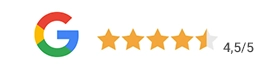
Lexicon Themes
- Metalworking (31)
- Plastic processing (8)
- Parts (8)
- Surface treatment (8)
- Welding (7)
- Machining (6)
- Sheet metal processing (6)
- Cutting (6)
- Turning (5)
- Manufacturing (5)
- Milling (4)
- Tool making (4)
- Suppliers (4)
- Casting (4)
- Procurement (4)
- Contract manufacturing (3)
- Profiles (3)
- Automation technology (2)
- Gearing & Thread (1)
- Forging (1)
- Wire processing (1)
- Heat treatment (1)